Induction furnace lining materials are one of the most challenging of all refractory applications. The performance of refractory materials used in induction steelmaking is also constantly improving.
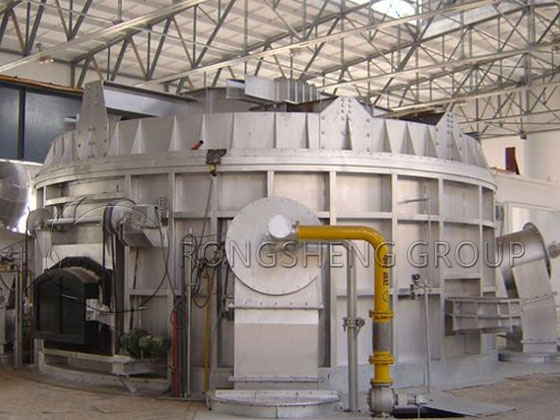
Refractory Lining Materials for Induction Furnace
Refractory materials for induction furnaces need to be selected based on the furnace type, furnace structure, type of steel being smelted, smelting process, and operating conditions. At the same time, the material of the refractory material, the change process and mechanism of the phase and physical properties from room temperature to working temperature, and the application conditions of the refractory material should also be considered.
(1) When melting cast iron and non-ferrous metals in a coreless induction furnace, SiO2, ZrO2·SiO2, and complex phase refractory materials composed of them are generally selected. Because ZrO2·SiO2 is thermally decomposed at high temperatures to generate ZrO2 and fSiO2. It is evenly distributed in the material, thus giving the material high-temperature plasticity and corrosion resistance, indicating that ZrO2 can extend the service life of SiO2-based refractory materials.
(2) The coreless induction furnace can use either the acid steelmaking method or the alkaline steelmaking method. Refractory materials used in acid steelmaking are the same as those used in smelting cast iron. Alkaline steelmaking uses neutral or alkaline refractory materials.
(3) When making steel in a small coreless induction furnace, magnesia refractory materials are usually used to build the lining. However, this kind of refractory material has poor thermal shock resistance and is easily penetrated by molten slag, resulting in structural spalling and premature damage. Therefore, it is difficult to adapt to the use environment of large capacity and intermittent operation.
(4) When making steel in a medium-sized coreless induction furnace in normal operation, refractory materials made of MgO-Al2O3 or MgO-Spinel mixture are used. They all belong to MgO-spinel refractory materials.
(5) Medium-sized coreless induction furnaces that use a variety of scrap steel as raw materials to make steel use Al2O3-MgO (about 10% MgO) refractory materials to achieve a long life.
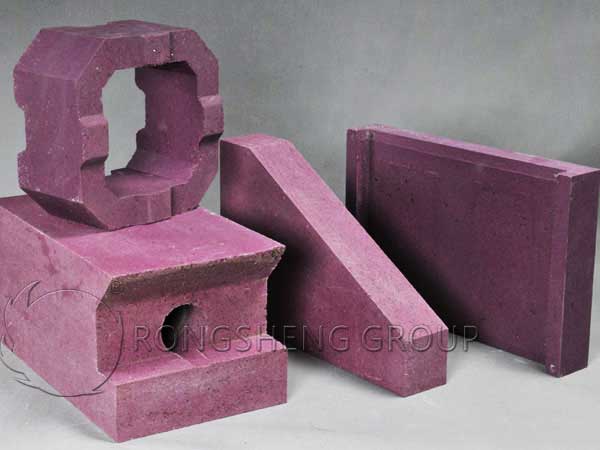
(6) Medium-sized induction furnaces using direct reduced iron balls as additives should use MgO-Al2O3-Cr2O3 (added chromium ore) refractory materials. Because MgO, Al2O3, Cr2O3, etc. react to form composite spinel when heated at high temperatures, it has high fire resistance and strong corrosion resistance. Improved adaptability to highly corrosive high-grade iron/manganese slag, resulting in long service life.
(7) Large coreless induction furnaces use spinel refractory materials made of pre-synthesized Spinel granules, or can also use MgO (coarse particles, fine powder), Spinel (medium particle fine powder) and Al2O3 particles. Mixture. At the same time, MgO-Spinel refractory materials are made by carefully balancing the ratio of pre-synthesized Spinel and in-situ Spinel. Both types of refractory materials can adapt to the operating conditions of large coreless induction furnaces.
(8) The operating temperature of cored induction furnace for smelting gray iron and cast iron is 1450~1550℃, which is not very high. Although the temperature at the inductor molten trench and water jacket is as high as 1600~1700°C, the selection of refractory materials is not very difficult because water cooling is implemented.
(9) Coreless induction furnaces mainly use knotting methods to build linings, while cored induction furnaces mainly use pouring methods to build linings. Knotted lined refractory materials form a sintered layer during the sintering process. In order to obtain high adaptability, it is expected that the expansion of the sintered layer and the increase in strength proceed slowly. Therefore, the formula design and raw material selection of refractory materials should ensure that the working surface in contact with the high-temperature melt during lining operation can be sintered to form a sintered layer with a certain strength. The non-working layer should maintain the bulk structure before sintering. This structure can prevent the migration of cracks in the working layer and absorb cracks, laying a good foundation for extending the service life of the lining.
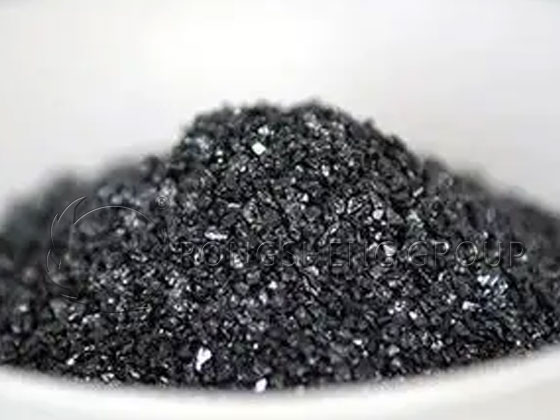
Silicon Carbide Lining for Induction Furnace
With the widespread promotion of electric furnace smelting, two non-metallic materials, silicon carbide and carburizer, are increasingly used in cast iron smelting.
Silicon carbide (SiC) is an artificial ore due to its corrosion resistance, high-temperature resistance, high strength, good thermal conductivity and impact resistance. It can be used for various smelting furnace linings, high-temperature furnace components, silicon carbide plates, lining plates, supports, saggers, silicon carbide crucibles, etc. In the foundry industry, the strong reducing properties of C and Si elements in silicon carbide are mainly used as refining agents and deoxidants for foundry metallurgical smelting. When an induction furnace is used to smelt cast iron and a large proportion of scrap steel is used in the furnace lining, SiC is used as a carburizing agent and silicon-increasing agent. It can improve the metallurgical quality of electric furnace smelting and improve the mechanical properties of castings.
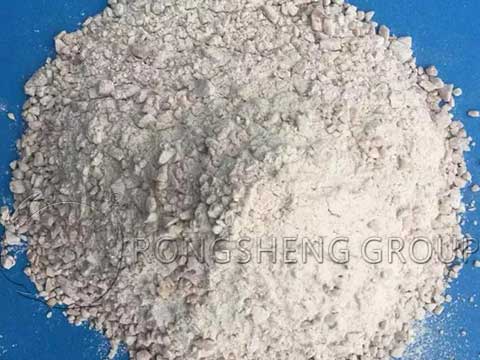
Medium Frequency Induction Furnace Silicon Lining Refractory Material
The medium frequency induction furnace lining material is referred to as electric furnace charge, also called acid charge or siliceous charge. It is made of silicone materials with a silicon content of more than 99.9% and several chemical materials. The service life of a good furnace charge can reach about 50 furnaces, and the age of the furnace is related to the type of steel being made!
During the initial and subsequent use of the intermediate frequency electric furnace, the furnace body needs to be lined and sintered. Furnace lining is to use the electric furnace material to create a protective layer along the wall of the furnace body to isolate the melting material and the induction coil in the furnace body to protect the induction coil. When punching the furnace lining, you should pay attention to using even force to hit it firmly. It can be finished in one go and formed in one go. After the furnace lining is laid, it needs to be baked at low temperature for a long time. It condenses into a solid whole with considerable strength and can withstand the impact of melt stirring and feeding. When sintering, the method of using an empty furnace with low power and slow heating should be followed, and baking should be continued for more than 36 hours to fully solidify. The quality of the knotting of the furnace lining is an important prerequisite for ensuring the service life and safety of the intermediate frequency carburizing furnace.
After the furnace lining is knotted, how to operate it correctly and reasonably is the key to extending the service life of the intermediate frequency electric furnace and ensuring life safety. Under normal circumstances, before operating an intermediate frequency electric furnace, you must first check whether the water flow in the water cooling system is smooth, whether the cooling water pressure and temperature are normal, whether there is water leakage, and whether the hydraulic system can work normally. During operation, be careful not to touch randomly. One person operates and one person supervises. And it is strictly forbidden for idle personnel to enter the computer room to prevent electric shock. During the smelting process, dry molten materials should be used, and materials should be discharged gently and added frequently. When the molten material in the furnace reaches the required level, it should be poured out in time to avoid high temperature and increased furnace lining loss. Observe frequently. If you find redness on the outside of the furnace body, this is a sign that the furnace will leak. Measures such as shutting down the intermediate frequency power supply and pouring out the molten material in the furnace should be taken promptly to avoid furnace leakage accidents. It should also be noted during use that when it is found that the furnace lining has become very thin and cannot be used anymore, the old furnace lining should be smashed and a new furnace lining should be made to prevent furnace leakage accidents. Note: The electric furnace charge is acidic, and alkaline materials cannot be added to the furnace.
To purchase high-quality refractory furnace lining refractory materials, please choose Rongsheng Refractory Materials Manufacturer. We have rich production and sales experience. Our refractory furnace lining materials have reliable quality and guaranteed customer service. Contact us to get free samples and quotes.