Refractory ramming materials are composed of refractory aggregates and powders, cementing agents, or additional additives. When mixed in proportion and constructed by ramming, it is called refractory ramming material. The maximum particle size of the aggregate of refractory ramming materials is generally 5 mm, which can also be enlarged to 10 mm, and the dosage is 60~70%. The dosage of refractory powder is 30~40%, and the dosage of cement or water is 6~10%. When using bonded clay as the cementing agent, its dosage is about 10%. Admixtures should be selected and added as appropriate according to the requirements of thermal equipment and construction. RS Refractory Factory is a refractory material manufacturer with rich production and sales experience. We will share 7 phosphoric acid combined refractory ramming material formulas for reference. The specific construction use needs to be determined based on the actual working conditions of the high-temperature industrial furnace.
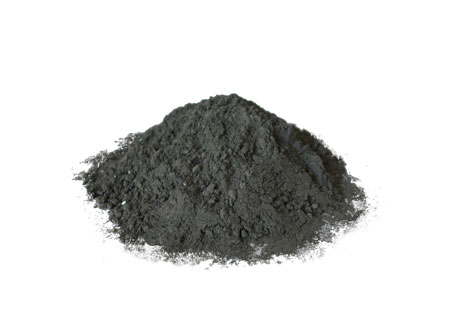
The performance of refractory ramming materials is better than that of vibration-formed refractory concrete of the same material and is lower than or equivalent to unfired bricks. For example, sodium polyphosphate magnesia refractory concrete adopts machine-pressed specimens. After burning at 1000℃, the compressive strength is 430kg/2cm. The pounded one is 395kg/2cm. Vibration molding is 360kg/2cm. However, the ramming construction efficiency is low and the labor intensity is high.
Sharing the formulas of 7 kinds of phosphoric acid combined with refractory ramming materials
Regarding the proportioning method of phosphate-bonded refractory castables and plastics. According to the different working conditions of different high-temperature industrial kilns, RS refractory material manufacturers can customize the formula of unshaped refractory ramming materials. In the production of refractory ramming materials, phosphoric acid is used as a binding agent. The following is a sharing of the formulas of 7 kinds of phosphoric acid combined with refractory ramming materials for reference.
- Use phosphoric acid combined with high aluminum ramming material for steel drums
A steel factory produced phosphoric acid-bonded high-aluminum ramming materials for steel drums. The formula ratio (w) is 60% to 65% of grade II high alumina clinker ≤8mm. 35%~40% of Class I high alumina fine powder <1.25mm. Mass concentration 40%~50% industrial phosphoric acid 7%~10%. The measured moisture content is 6%~7.5% in summer and 5%~6.5% in winter. If the material is trapped for more than 16 hours, when the material is dry, it can be moistened with dilute phosphoric acid with a mass concentration of 25% to 35% before use, and then tamped into shape. The wind pressure of the tamping machine is 0.5MPa. The properties of the ramming material are as follows: the compressive strength at 1100℃ is 59.9MPa. At 1450°C, the apparent porosity is 24.9%, the bulk density is 2.32g·cm-3, and the compressive strength is 54.7~57.7MPa.
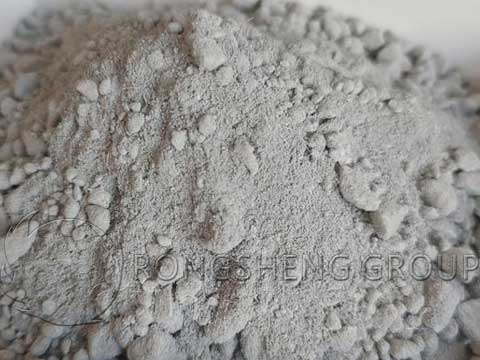
- The ladle working for the converter is lined with ramming material combined with phosphoric acid
Another steel plant used special-grade bauxite clinker from Mi County, Henan Province to produce ramming materials bonded with phosphoric acid for converter ladle work. The ratio is 40%~50% for 8~3mm, 30% for ≤3mm, and 20%~30% for <0.088mm. The concentration of externally processed industrial waste phosphoric acid is 45%~51%, and the additional amount is 10%~12%. Mixing is carried out in a J4-1500 liter forced mixer, feeding 1.5~2t each time and dry mixing for 2~3 minutes. After the granules and powder are evenly mixed, slowly add phosphoric acid and wet mix for 4 to 6 minutes. To prevent agglomeration, the phosphoric acid should be added slowly without stopping, and the dryness and humidity of the material should be such that it does not agglomerate after loosening the hand.
For tamping, 2 to 3 D10-11720 tamping machines are used. Use a 1.5-inch high-pressure hose to connect the compressed air nozzle and the hammer handle. The air pressure is 0.4~0.5MPa. Place the mold core (wooden mold or steel mold) in the ladle, and the height of the ladle is 1800mm. The mold core consists of three sections, each section is 560mm high. Place the first section first, and make the distance between the mold wall and the package wall equal to 160mm. Then circle the fabric evenly about 100mm thick. Two people control the pneumatic hammer to pound along the circle. When the reduction amount is 50mm, the second cloth tamping is carried out. When the first section of the mold core is flat, put down the second section of the mold core and the third section of the mold core, cloth the cloth in turn, and pound until the bag mouth. It is not advisable to stop midway when tying the knot and take off the mold core immediately after tying the knot. The bulk density of the knotted layer is 2.09~2.13g.cm-3. Bake with gas baking equipment. Bake at low heat (200°C) for 4 hours, medium heat (300~400°C) for 4 hours, and high heat (600°C) for 8 hours. It is best to use it promptly after baking.
- Use high-aluminum plastic ramming material for the top of the electric furnace
A refractory material manufacturer has produced high-aluminum plastic ramming materials for electric furnace roofs. The raw materials are <5mm special grade high alumina bauxite clinker, fused corundum fine powder, and Suzhou porcelain clay. Use phosphoric acid as a binding agent and oxalic acid as a preservative. The ramming material has a shelf life of 3 months, and its flexural and compressive strength are improved after 15 days of storage. It decreased slightly at 30 days, then basically remained unchanged, until a significant decrease occurred at 90 days.
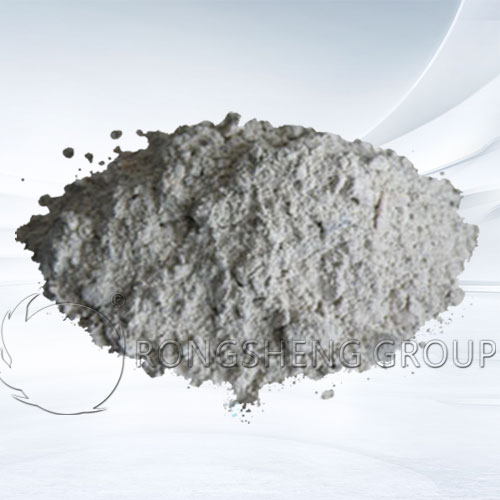
- Application of refractory castables in steel drums and walking heating furnaces
Some steel mills have also studied the application of refractory castables in steel drums and walking heating furnaces. The raw materials and proportions (w) are II grade high alumina clinker 10~1mm55%, 5~1mm15%. ≤1mm cylinder grinding powder 30%, industrial phosphoric acid with a concentration of 60% 6.7%~7.2%, alumina cement 2%. The process is: mix with a wet mill, dry mix coarse and medium particles for 1 to 2 minutes, pour in all the phosphoric acid, and mix wet for 3 to 5 minutes. After grinding, the materials are piled together and covered with wet sacks. The temperature is 5~35℃ and the materials are trapped for 20~44 hours. After the materials are trapped, they are mixed twice in a small mixer, and 2% (w) alumina cement is added at the same time. If the material is too dry, add 0.1%~0.3% water and stir for 5~10 minutes. For ramming, the wind pressure is 6 atmospheres, the thickness of the material is 25~35mm, and finally, the steel plate is added for tamping, and the mold is de-moulded immediately after completion. Next, dry, naturally dry at room temperature >5°C for 1 day, and can be stacked. It can be used directly without baking. It is built with mud and placed on the heating furnace. After the furnace is built, it is baked for a week. Observed in good condition after two years of use.
- Wear-resistant plastic ramming material for waste heat power generation
The process of using wear-resistant plastic ramming materials for waste heat power generation. The raw materials and proportions (w) used are 55% fused brown corundum aggregate, brown corundum powder, SiC powder, and SiO2 micro powder. 45% of fine powders such as Guangxi white mud and expansion agent, plus 0.15% of corrosion inhibitor. The binding agent is aluminum dihydrogen phosphate. The composition of aluminum dihydrogen phosphate (n(H3PO4): n(Al(OH)3)=3, 4, 5) was studied. Mixing process. A: After stirring the above raw materials evenly in the mixer, add the binding agent aluminum dihydrogen phosphate at one time. B: After stirring the above raw materials evenly in the mixer, add 1/2 of the binding agent aluminum dihydrogen phosphate, stir for 3 minutes, and seal the material for 24 hours. Then, add the remaining binding agent aluminum dihydrogen phosphate twice and stir. The influence of the additional amount of cement accelerator (mass fraction: 0.5%, 1%, 1.5%, 2.0% respectively) on the performance of the ramming material. It was found that (n(H3PO4): n(Al(OH)3)=5, using the B mixing process and adding 1.5%~2% (w) cement has better performance.
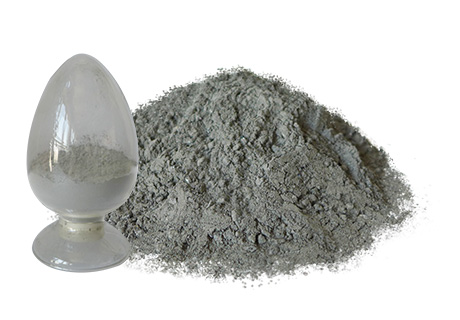
- High aluminum-silicon carbide-carbon ramming material for tap trough
A refractory material factory produced high-aluminum-silicon carbide-carbon ramming materials for tap troughs. The mixing ratio (w) is 50% grade I high alumina clinker ≤10mm, 25% black silicon carbide, and 10% asphalt. Fuzhou soft clay is 15%, and the binding agent is 10% industrial phosphoric acid with a specific gravity of 1.26~1.28. Keep the material trapped for more than 24 hours at >15℃ and then put it into barrels. 0.4MPa air hammer for layered ramming.
- Performance of phosphate-bonded graphite-silica ramming material
A steel company studied the effects of graphite content, binder, and FeSi additive addition on the properties of phosphate-bonded graphite-siliceous ramming material. Wherein,
Graphite content, the mass fraction of graphite is 0, 10%, 20%, 30%, and 40% respectively;
Binder, aluminum phosphate is prepared by using aluminum hydroxide and orthophosphoric acid at a ratio of 1:7; magnesium phosphate is prepared by using magnesium hydroxide and orthophosphoric acid at a ratio of 1:4;
The added amounts of FeSi additives are 3%, 5%, 7%, and 10% by mass respectively.
Finally, the formula (w) was determined to be 90% silica sand, 10% flake graphite, 5% FeSi, 4% aluminum phosphate, and 4% pulp waste liquid. To ram the inner lining of a 34t ladle, the tamping equipment is a TP-1 pneumatic vibrator. After demoulding, the lining should be smooth and crack-free and then baked with a gas burner over an open flame until the surface reaches 500°C for 12 hours. The molten steel pouring temperature is 1575~1625℃, the time is 35 minutes, the slag basicity is 2.5~2.9, and the average life is 19 furnaces.
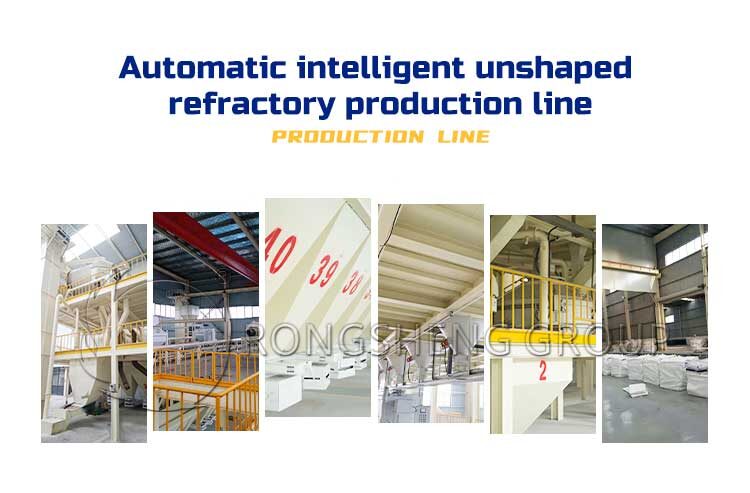
RS Refractory Materials Factory
Ramming materials are like plastics. To extend the shelf life, preservatives and corrosion inhibitors such as oxalic acid must be added. Ramming materials are usually rammed with a pneumatic hammer, and the pressure of compressed air is 4 to 5 atmospheres. There are square and round hammerheads with a diameter of 80~100mm. A square hammer head is better because it can pound the corners of masonry and precast blocks better. The construction is done in layers, with each layer 50~80mm thick. After each layer is compacted, the surface needs to be loosened by about 10mm so that the layers can be better connected. Finally, smooth the surface of the construction body.
RS Refractory Materials Factory can provide high-quality, customizable refractory services for high-temperature industrial furnaces. Our products are of reliable quality and our after-sales service is guaranteed. Contact us for a free sample and quote for monolithic refractory ramming materials.