High alumina bricks for calcium carbide furnaces should be selected in different parts. The quality of high alumina bricks used around the furnace wall, furnace bottom, and furnace door is different.
Grade I High Alumina Bricks for Calcium Carbide Furnace Walls
Under normal circumstances, the furnace wall temperature of a calcium carbide furnace is high, so high-aluminum bricks with an aluminum content greater than 75% should be selected, especially since the density should not be less than 2.5. The size of the bricks used for the furnace wall should not be less than 345mm long. Bricks that are too short will have a short service life. Some manufacturers also use double layers, that is, two 345mm long bricks are used as linings. Some manufacturers also design bricks to be 450mm long in order to increase their service life.
However, regardless of whether the bricks are built in a single layer or double layer, the material must not be less than 75% aluminum content, and the density cannot be too low. If you use dialumina bricks or high alumina bricks with too low density, no matter how long the bricks are, the red kiln phenomenon will occur in a short time. Therefore, the material of the bricks used for the furnace wall cannot be ignored.
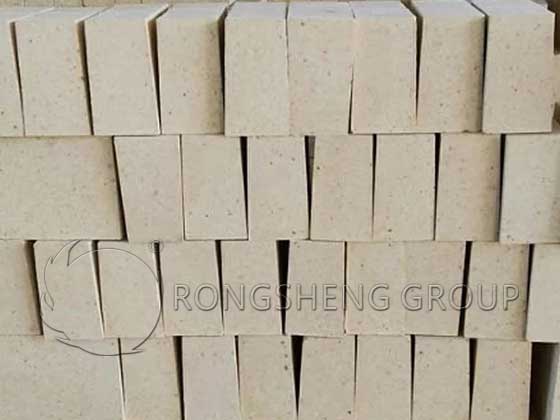
High Alumina Bricks for Calcium Carbide Furnace Bottom
The bottom of the carbide furnace can be made of clay bricks or secondary high alumina bricks. The furnace bottom generally needs at least 6 layers of bricks as the permanent layer, and there must be carbon bricks as the working layer on top. There are also manufacturers that use clay bricks for the bottom layers and secondary high alumina bricks for the layers near carbon bricks. However, some manufacturers have designed ten layers of permanent layers at the bottom of their calcium carbide furnaces, all of which use secondary high alumina bricks. This is based on the usage requirements of the manufacturer.
The clay bricks or secondary high alumina bricks used in the furnace bottom are T3 bricks or 345mm long G2 bricks. If you want to reduce the mortar joints, you can use 345mm bricks. You can also use standard bricks. There is not much difference. It’s just that there are more or less gray seams. The key is that the size is accurate and there is no misalignment.
Dimensional Requirements for High Alumina Bricks for Calcium Carbide Furnaces
Whether it is high-alumina bricks for furnace walls or furnace bottoms, while the material is important, the size is also very important. Because the sizes are different, the masonry effect is not good, which also affects the service life. Therefore, the brick size must be within the national standard.
High Alumina Brick LZ75 Standard Brick Size 230*114*65mm
- Product name: 75 high alumina refractory bricks, high alumina T-3 bricks
- Regular size: 230*114*65
- Product material: high aluminum (aluminum trioxide)
- Product name: High alumina T-38 brick (knife edge)
- Product specifications: 230*(65/55)*114
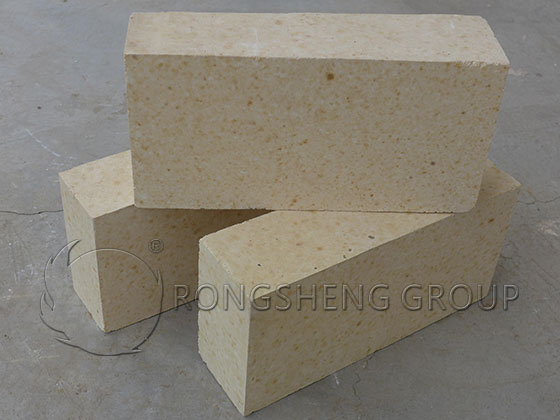
Rongsheng refractory material manufacturer mainly provides refractory lining solutions for high-temperature industrial furnaces. Customized furnace lining refractory materials for high-temperature industrial furnaces. It mainly processes and produces drying equipment dryers, pulverized coal furnaces, hot blast furnaces, and other industrial furnace refractory raw materials, and refractory products. Refractory lining products are shipped directly from Rongsheng manufacturers at competitive prices. High-alumina refractory aggregate, fine powder, is divided into grades one, two, and three, with alumina content of 80%, 75%, 70%, and 65% respectively. Product specifications range from 20 mm to 200 mesh and can be used to make refractory bricks, refractory castables, etc.
Lightweight refractory aggregate, refractory degree greater than 1580 degrees, bulk density 0.8-1.2, high strength. Mainly used as raw material for lightweight thermal insulation bulk materials. Refractory products include lightweight insulation refractory bricks.
High alumina, clay refractory standard bricks, special-shaped clay, high alumina refractory bricks T3, T38, T39, T43, T44, and other specifications, clay high alumina fire clay, available in stock. Shipping is fast. Widely used in kilns such as forging furnaces, heating furnaces, drying furnaces, activated carbon furnaces, trolley furnaces, annealing furnaces, etc.
Production Technology of High Alumina Bricks for Calcium Carbide Furnaces
Class I bauxite clinker and fused white corundum powder are used as raw materials and an appropriate amount of expansion agent is added. After forming and heat treatment at 800°C, high alumina bricks with good thermal shock stability can be produced. Class I bauxite clinker and fused white corundum powder are used as raw materials and an appropriate amount of expansion agent is added. After forming and heat treatment at 800°C, high alumina bricks with good thermal shock stability can be produced.
In order to reduce the porosity of high alumina bricks, corresponding measures must be taken in each process from the selection of raw materials, batching, and mixing to shaping and firing. The water absorption rate of the selected first-level high-alumina bauxite clinker should be less than 5%, and the water absorption rate of the second-level high-aluminum material should be less than 7%. Mix soft clay with a moisture content of less than 4% and bauxite clinker and grind it finely. Using this mixture of finely ground powder ingredients can reduce the porosity of the bricks. The particle gradation during batching is preferably 4:2:4 between coarse, medium, and fine, and the largest particle should not exceed 5mm. The feeding sequence during mixing is as follows: add coarse particles first, then add sulfite pulp waste liquid and premix for 3 minutes. Finally, high aluminum fine powder is added and mixed.
Rongsheng High Alumina Refractory Brick Manufacturer
Rongsheng High Alumina Refractory Material Manufacturer is a powerful manufacturer and seller of refractory bricks. Our refractory products have been sold to more than 100 countries and regions around the world. Contact us to get a free quote for the solution of refractory materials for calcium carbide furnaces.