The forging heating furnace is a key equipment in the forging industry. It is characterized by intermittent operation, large temperature changes, and often works under conditions such as high temperature and strong vibration, collision of loading and unloading machinery, and chemical erosion of iron oxide scales. It seriously damages the lining bricks of the furnace, shortens the service life of the furnace, and also causes the heat loss of the furnace to increase. Self-flowing refractory castable for heating furnace is a high-strength refractory castable used for the overall structure of forging heating furnace. It has a certain positive effect on extending the life of the heating furnace and reducing energy consumption.
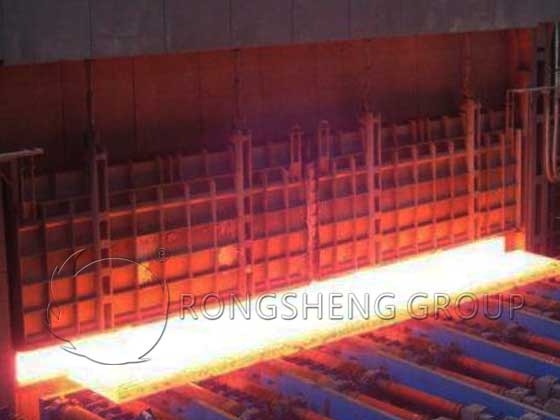
High-Strength Refractory Castables for Forging Heating Furnaces
The heating furnace uses high-strength refractory castables. The water consumption of self-flowing castables is slightly higher than that of low-vibration cement refractory castables of the same material. However, the performance of self-flowing refractory castables is still good, especially its high strength and small linear change after burning. Because this material is self-leveling and well-ventilated, its particle gradation is reasonable and can achieve the tightest packing density. The binder, ultrafine powder, and water-reducing agent are selected reasonably and the dosage is optimal. Therefore, it can overcome the defects caused by large amounts of water and improve its performance.
The self-flowing refractory castable for the heating furnace is made of bauxite clinker as refractory aggregate, mixed with first-grade bauxite clinker and mullite aggregate. Refractory powder uses special-grade bauxite clinker powder, corundum powder, and mullite powder. Add α-Al2O3 and SiO2 ultrafine powder and expansion agent at the same time. Use aluminate cement as a binder and add a phosphate water-reducing agent.
When the composition, mix ratio, and water consumption of the self-flowing refractory castable remain unchanged, adjust the addition amount of the two to ensure that the combined amount is 7%. As the amount of uf-SiO2 increases, the flow value begins to increase sharply and then levels off. The flexural strength after burning does not change much and has an optimal value. After burning, the line change first increased from negative to positive and then shrank sharply. The dosage of uf-SiO2 is generally 3%~5%. That is, when the dosage of α-Al2O3 ultrafine powder is 4%~2%, the flow value of the castable is ≥180mm. The physical and mechanical properties are also better.
The composition materials and water consumption of self-flowing castables remain unchanged. When the cement consumption is increased, the fine powder consumption is correspondingly reduced. As the amount of CA-70 cement increases, the flow value of the castable decreases. The linear change after burning at 1450℃ changes from a positive value to a negative value, that is, from linear expansion to linear contraction. Because the amount of cement is large, the free water consumed during hydration increases, causing the viscosity of the castable to increase. As the flow value decreases, the density also decreases, and the linear change after burning changes from positive to negative. Then the optimal dosage of cement is 2% to 6%, and the flow value and physical properties of the castable are the best.
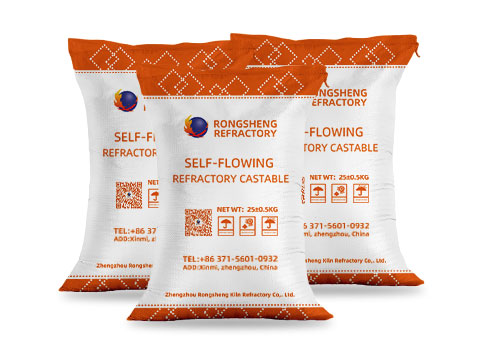
Improvement Measures for Furnace Lining Structure of Chamber Heating Furnace
High-strength refractory castables are good lining materials for forging heating furnaces, which extend the life of the furnace, reduce energy consumption, and achieve good economic results. According to the actual production and practical needs, the overall furnace structure of the chamber heating furnace can be improved in the design. The improvement measures can be carried out gradually according to the furnace top, furnace wall, furnace bottom, expansion joint reservation, and other parts.
(1) Stovetop.
The furnace top is a composite flat furnace top. 48 high-aluminum hanging anchor bricks are evenly buried in the furnace roof, and the brick length is 460mm. The anchor bricks and refractory castables form a whole, and the thickness of the cast layer is 300mm. The furnace top adopts a metal hanging structure, and the hanging bolts are connected to the metal hanging beams. The force on the hook is adjusted evenly, keeping the overall force on the hook in a free-hanging state. The upper surface of the furnace roof is covered with a layer of 70mm thick refractory fiber to enhance the furnace’s thermal insulation performance.
(2) Furnace wall.
The furnace wall is composite. A δ=8mm steel plate is added around the furnace wall. A 40mm thick refractory fiber is pasted on the inside of the steel plate. A 114mm lightweight refractory brick is built on the inside of the refractory fiber. The lining is cast as a whole with high-strength refractory castables. The casting layer is 300mm thick. The burner hole is reserved during pouring, and the burner brick is embedded after the castable solidifies. The gap between the burner brick and the castable is filled with fine powder, and the furnace wall is poured at one time. Compared with brick furnace walls, it has good impact resistance and thermal insulation effects, reduces heat loss, and saves energy.
(3) Bottom of the furnace.
In order to improve the wear resistance of the furnace bottom, steel fiber-reinforced castables are used and integrally poured into the pit surface. The working layer at the furnace bottom is 280mm thick, and 210mm thick refractory clay bricks and lightweight refractory clay bricks are laid underneath. Some of the clay bricks were laid up to the ground level in the parts that withstand lower temperatures. Three flue holes are left in each room to communicate with the main flue, and the flues are all built with refractory sticky bricks.
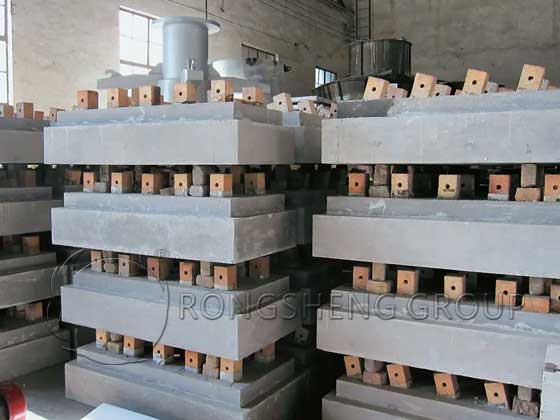
(4) The connection between the furnace top and furnace wall.
The furnace wall does not bear the weight of the furnace top, and there is a 20mm gap between the two to allow the furnace wall to expand due to heat. In order to prevent flames from escaping from the joint between the furnace wall and the furnace top, the two should overlap by at least 150mm. Clay bricks are built on the side of the stovetop to isolate the flame, and clay bricks are wet-laid on top. Seal the gaps between the furnace top castables, refractory clay bricks, and refractory fiber fillers to prevent fire escape.
(5) Expansion joints are left.
Leave an expansion joint at the four corners of the furnace wall, at the center of the middle partition wall, and at the joint between the partition wall and the front and rear. The width of the expansion joint is 3~4mm, and a flammable corrugated board is used as the filling material. There is no expansion joint left on the furnace top itself. 20mm refractory fiber is laid around the working layer of the furnace top to replace the expansion joint.
(6)Construction.
The construction of high-strength refractory castables is different from ordinary refractory castables. Therefore, careful construction must be carried out in accordance with relevant regulations, and the burner, flue, and furnace door membrane must be installed before installing the formwork. Then set up the furnace wall formwork, and connect the hole membrane to the furnace wall formwork. The furnace top formwork will be set up after the furnace bottom castable has a certain strength. After the installation is completed, the anchor bricks are hung. The gap between the lower end of the anchor brick and the formwork is 0~5mm. The formwork support must be firm and must not be loose. High-strength refractory castables are finished materials that must be stirred evenly by a forced mixer before pouring. Put the material into the mixer and mix it dry for 1 minute, add 6.5%~7.2% water, and mix it wet for 3~4 minutes before discharging the material. The mixture poured out from the mixer must be used within 30 minutes.
Buy high-quality refractory castables for heating furnaces, refractory precast shapes, precast refractory blocks, etc. Please contact us or leave us a message on this page.