Wear-resistant refractory materials for boilers generally refer to refractory materials with Al2O3/SiC/SiO2 as the main component that has excellent wear resistance under service conditions. Wear-resistant refractory materials are divided into wear-resistant refractory bricks, wear-resistant refractory castables, wear-resistant refractory plastics, and wear-resistant refractory mortar. Wear-resistant refractory materials are generally suitable for circulating fluidized bed boilers, municipal solid waste incinerators, and industrial waste incinerators. Wear-resistant refractory materials for medical waste incinerators, general solid waste incinerators, hazardous waste incinerators, and petroleum catalytic cracking.
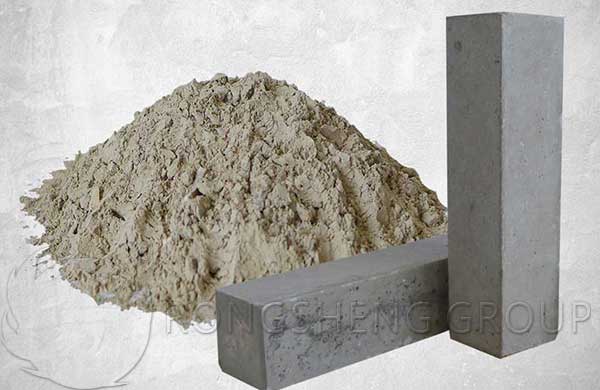
Wear Resistance of Refractory Materials for Boilers
Wear resistance is the ability of refractory materials to resist external wear (such as friction, impact, peeling, etc.). The transition zone of the cement rotary kiln, the circulating fluidized bed boiler, and the cooling section of the dry quenching coke oven all put forward certain requirements on the wear resistance of the refractory material.
Abrasion of wear-resistant refractory materials in the use of boiler inner lining
Wear is divided into corrosive wear, abrasive wear, adhesive wear, and fatigue wear. Its mechanism is a cutting mechanism, adhesion mechanism, and fatigue mechanism. Influencing factors of friction and wear:
- (1) Load: Generally, the greater the load, the more serious the wear.
- (2) Speed: Generally, the higher the speed, the more serious the wear.
- (3) Temperature: Low-temperature wear is mainly fatigue, adhesion, and delamination mechanisms. The main mechanisms of high-temperature wear are oxidation, adhesion, and delamination.
- (4) Abrasive concentration: Generally, the greater the abrasive concentration, the more serious the wear.
Factors Affecting Wear Resistance of Refractories
The strength, hardness, and density of the refractory material itself, the bonding strength, and the microstructure between particles have a great influence on the wear resistance of the material. The service temperature of the refractory also has a certain influence on its wear resistance. A lot of research work has been carried out on how to improve the wear resistance of refractory materials. In addition to improving the density of materials and reducing the defects of materials, the main research ideas are divided into the following parts. (1) Refine the grains, thereby improving the overall uniformity of the material. (2) Introduce the reinforcing phase, and the components are compounded to form a multi-phase material. (3) Phase transformation toughening. Generally speaking, under the same hardness, materials with higher strength have better wear resistance. The wear resistance of the sample can be improved by selecting materials with good wear resistance, introducing a second phase with high hardness and strength, and selecting a reasonable particle gradation.
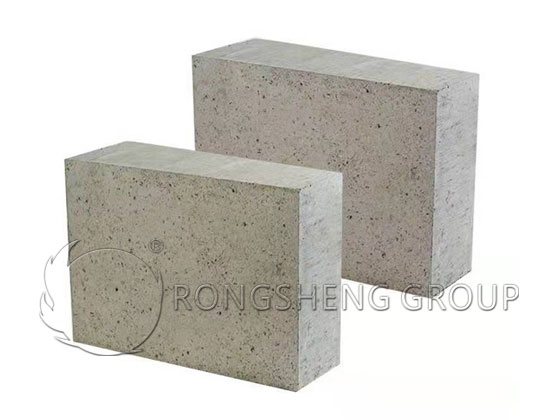
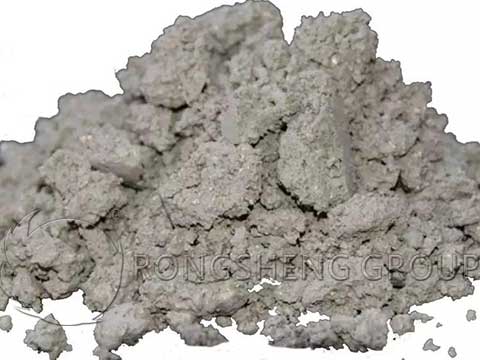
The strength of wear resistance of refractory materials
According to the wear resistance of various refractory materials, they can be roughly divided into three categories. Silicon carbide refractories have the strongest wear resistance, high alumina refractories, and corundum refractories have intermediate wear resistance, and alkaline refractories, silicon, and clay refractories have the worst wear resistance.
Due to the large difference in alumina content of high-alumina refractory materials, the wear distribution range is wide.
The higher the hardness of the mineral, the stronger its wear resistance. It can also be said that the silicon carbide refractory wears the least amount. Therefore, some key corrosion parts are made of wear-resistant refractory materials.
The silicon nitride combined with silicon carbide material has high hardness and high strength. The hardness of the bonding phase of mullite and the glass phase of the clay-bonded silicon carbide material is relatively small. Therefore, silicon nitride-bonded silicon carbide materials have better wear resistance than clay-bonded silicon carbide materials.
Why are monolithic refractory materials of the same material better than refractory bricks in wear resistance?
The wear resistance of high alumina castables prepared with the same high alumina bauxite clinker is better than that of high alumina bricks. The amount of wear between the two differs by about 60%-90%. Also, the wear resistance of clay castables will be better than that of clay bricks.
Castables adopt micro-powder technology and the density of low cement castables is usually greater than that of corresponding refractory bricks. Because the castable uses aggregates with a larger particle size, and the aggregate ratio of the castable is larger. The aggregate is usually denser and more wear-resistant than the matrix.
The phase composition and organizational structure of refractory castables after drying are different from those after roasting and high-temperature use, which is also characteristic of amorphous castables. In the laboratory, after heat treatment of high-alumina refractory castables, the wear resistance of high-alumina refractory castables at higher temperatures is poor.
Now some castables are generally made of silicon carbide to improve the wear resistance of castables in order to achieve wear resistance. And many castable manufacturers have changed from black silicon carbide to green silicon carbide. Because the black silicon carbide is 200 mesh and the green silicon carbide is 320 mesh, especially the green silicon carbide combined with micro-powder technology, the castable has good fluidity and stronger wear resistance.
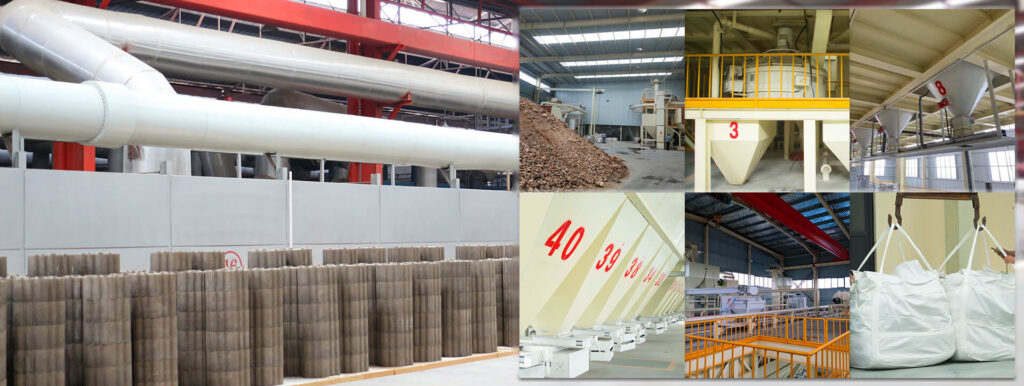
Rongsheng Refractory Material Manufacturer
Rongsheng refractory material manufacturer is a powerful refractory material production and sales manufacturer. Our wear-resistant refractory materials are widely used in the wear-resistant layer of kiln lining. Whether it is in hazardous waste incinerators, rotary kiln incinerators, or circulating fluidized bed boilers, there are application examples. Moreover, we provide wear-resistant or material products that are most suitable for boiler production conditions according to the working conditions of different kilns. In addition, we also provide high-quality kiln insulation refractory lining design and the supply of corresponding refractory materials. Contact us for free samples and prices of wear-resistant refractory materials.