The longevity of the blast furnace is a systematic project, in which the refractory materials of the blast furnace body play an important role. Therefore, the blast furnace lining must select appropriate refractory materials according to the location. The principle of selecting refractory materials for blast furnace lining must be based on the fact that the refractory lining corresponds to the heat flow intensity of this part, and the refractory material corresponds to the corrosion mechanism of this part. This can alleviate and delay the damage rate and extend the life of the blast furnace. Choose refractory materials with low prices and high-cost performance. Commonly used long-life refractory lining materials for blast furnaces include various refractory bricks and unshaped refractory materials.
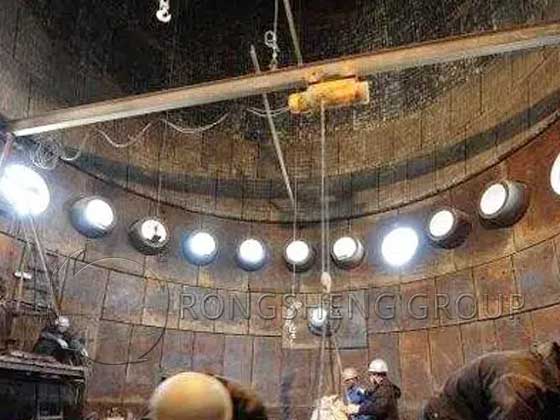
Monolithic Refractory Materials for Blast Furnaces
(1) Castable. Some small blast furnaces are lined with castables. A typical case is that a blast furnace of a steel pipe company used high-density castables on the upper part of the furnace body. After 6 years, only a small amount of peeling was found. At present, blast furnaces use clay castables for the internal cavity of the steel brick in the furnace throat and the gap between the steel brick and the furnace shell. High-aluminum self-flowing castables are used behind the furnace throat steel bricks, furnace top sprinkler pipes, and short pipes.
(2) Spray paint. Spray paint can be used on the inside and above the middle part of the furnace belly. It can improve the air tightness of the blast furnace body and protect the steel shell of the furnace body.
(3) Grouting material. Mainly caulking, lining, and quick repairs.
(4) Ramming mass material. There are carbon ramming mass materials and silicon carbide ramming mass materials. It is used for filling the gap between the carbon bricks and the cooling stave, as well as filling and pounding the leveling layer above the center line of the water-cooled tube at the bottom of the large blast furnace and above the furnace bottom sealing plate. It is also suitable for filling between the cooling staves of the hearth and filling and ramming between the cooling staves above the hearth.
(5) Fire-resistant buffer material. It is mainly used to buffer expansion stress. Blast furnace buffer materials include high aluminum and silicon carbide buffer materials.
(6) Carbon filler. Filling is mainly composed of carbon materials such as metallurgical coke and coal tar. It is mainly used to fill the bottom of the blast furnace floor and both sides of the cooling plate.
(7) Iron filings filling. It is a bulk material made of clay clinker fine powder, iron filings, and iron concentrate powder as the main raw materials, with ultrafine powder added and combined with cement or water glass. It is used to fill the gaps between the cooling staves, between the furnace throat steel bricks, and between the cooling staves and the taphole frame, air, and slag opening sleeves.
(8) Refractory mud. There are many types of refractory slurry for blast furnaces. One is bonding and repairing the joints of refractory bricks used to build the furnace body. Generally, mud is made of the same material as refractory bricks. If you are building carbon bricks, use carbonaceous mud or carbonaceous mud. Clay bricks are built using clay clinker as the base material and clay refractory slurry is combined with soft clay or chemical binders. There are also insulating refractory mud for building insulating refractory products, silicon carbide refractory mud for building silicon carbide bricks, etc. The other is a paste-like or slurry-shaped unshaped refractory material that is pressed into mud and constructed using extrusion methods. It is composed of refractory powder, binder, and admixture. It can be used after mixing with water or liquid binder. Press-in materials are made of different materials in different parts of the blast furnace. For example, high-aluminum press-in materials are mostly used for the furnace body, while the furnace hearth, furnace belly, and other parts are mostly used for carbon-based press-in materials. In addition, there is a buffer refractory slurry based on compressible refractory raw materials to buffer the thermal expansion stress of refractory brick masonry.
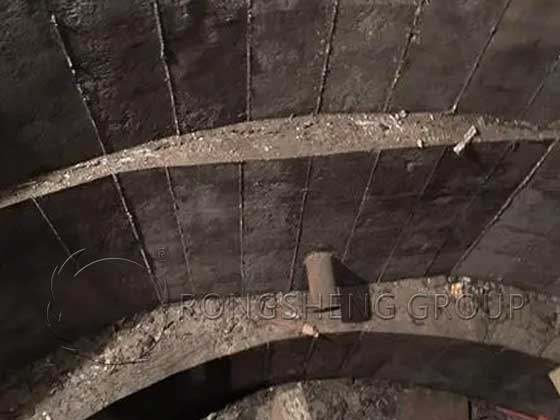
Blast Furnace Bottom Carbon Ramming Mass Material Long-life Refractory
The function and application of furnace bottom carbon ramming material for the longevity of blast furnace. Carbon ramming mass materials are widely used in blast furnaces. Carbon ramming material is used in the gap between the carbon bricks in the blast furnace bottom and the furnace bottom sealing plate and in the leveling layer above the center line of the furnace bottom water-cooling tube. It is required that the carbon ramming mass material after arrival has a certain strength and density. Fill every nook and cranny to ensure no leakage of molten iron. Moreover, the thermal conductivity of the carbon ramming material must be consistent with the performance of the high thermal conductivity carbon bricks, so as not to affect the life of the blast furnace and ensure the normal production needs of the blast furnace.
Functions of carbon ramming materials
Carbon ramming mass material plays an important role in transferring heat. Blast furnace cooling needs to transfer the heat of carbon bricks through blast furnace carbon ramming material. It is taken away by cooling water to slow down the erosion rate. If the thermal conductivity of the carbon ramming mass material is too low and inconsistent with the performance of the furnace bottom carbon bricks, it will affect the smooth transfer of heat, cause the temperature of the carbon bricks to rise, and accelerate the erosion of the carbon bricks.
Carbon ramming material plays the role of refractory brick lining. Carbon ramming mass material is made of the same material as carbon bricks. In the later stages of the blast furnace, if the carbon bricks burn through or leak molten iron and slag, the carbon ramming material can act as a refractory brick lining to protect the furnace bottom and maintain normal production.
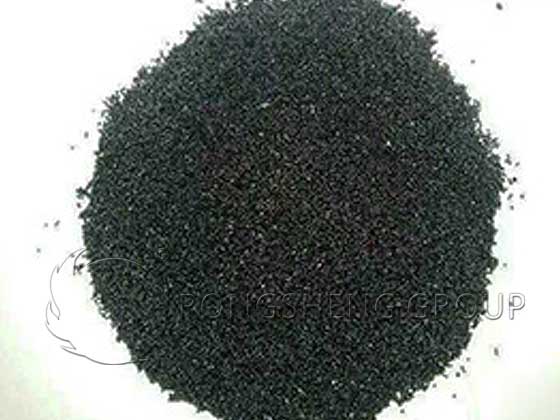
Application of carbon ramming materials in the furnace bottom
The blast furnace bottom is subjected to high temperature, high pressure, slag, and iron erosion and penetration, and the working conditions are very harsh. Therefore, carbonaceous materials with excellent performance must be used. Graphite materials have extremely high thermal conductivity, high-temperature resistance, lubricity, plasticity, slag resistance, and chemical and thermal stability. Therefore, carbon ramming mass uses in the leveling layer between the blast furnace bottom carbon bricks and the furnace bottom sealing plate and above the center line of the furnace bottom water-cooling pipe.
Construction of carbon ramming material
The construction of carbon ramming materials is mainly based on the ramming method, but the construction methods will be different in different use parts and construction body structures. The construction of carbon ramming mass material at the bottom of the blast furnace must wait until the control flat steel is installed and inspected before starting the ramming construction. In order to prevent damage to the leveling flat steel, the ramming mass material must be evenly spread in the leveling flat steel belt during construction. Use a flat vibrating rammer to continuously pound back and forth along the space between the steel strips until it is dense. The pounded surface must be shaved first, then a layer of material is added and the pounding continues. The thickness of each layer of paving material is 100mm. After 2-3 times of adding material (adjust according to the design size of the drawing), it can be compacted continuously. The rammed carbon ramming material must be higher than the top surface of the flat steel. Finally, use a scraper to level the top surface of the steel strip one by one. Use a spirit level to check whether it is on a horizontal plane. Only after the test reaches the standard can the next step of carbon brick laying be carried out.
Precautions for construction of carbon ramming materials
Construction should be carried out strictly in accordance with the construction instructions of the carbon ramming material. During construction, the edges such as the four corners should be pounded tightly to avoid deterioration in thermal conductivity and erosion.