Refractory Gunning Mix is a kind of unshaped refractory material used when repairing the lining of thermal kiln equipment by spraying construction method. It is composed of 0-5mm particle gradation, with a chemical binding agent and admixture. Refractory Gunning Mix coatings can be used to spray new linings, and can also be used to repair furnace pipes. It is not only convenient for construction but also has a good effect in extending the service life of the kiln and reducing the consumption of refractory materials.
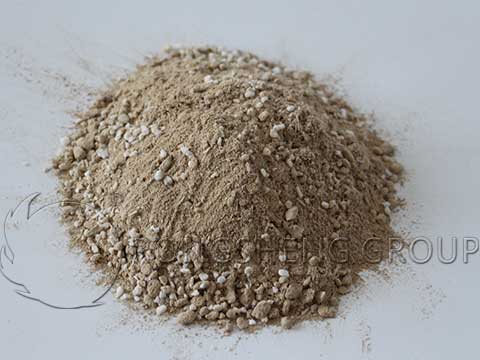
Get Free Quote
Types of Refractory Gunning Mix Coatings
Refractory Gunning Mix coatings are divided into light Refractory Gunning Mix coatings and dense Refractory Gunning Mix coatings. The materials selected according to different use environments include corundum, high alumina, mullite, clay, SiC, and magnesia. Mainly used in hot blast stoves, heating furnaces, and soaking furnaces, blast furnaces, flues, and chimneys, etc. However, the price of light-weight is relatively more expensive than dense Refractory Gunning Mix coatings.
The body density of dense Refractory Gunning Mix is generally 1.6-1.8g/cm3. However, the different requirements in different furnace pipes, especially the sintering machine pipes, must be much better than other parts, that is, the Refractory Gunning Mix paint with a density of 2.2g/cm3. Of course, the price of Refractory Gunning Mix coatings for sintering machines is much higher than that of Refractory Gunning Mix coatings for other parts.
The Characteristics of Rongsheng Gunning Mix Coating
- Low rebound rate, good high-temperature performance, and strong thermal adaptability. When using Gunning Mix to repair various industrial kilns, there is no need to stop the furnace to cool down. It can be sprayed directly or sprayed with a spray gun. It greatly shortens the repair time of the furnace lining and reduces the production cost.
- The Gunning Mix has high bonding strength with refractory materials under the action of a high temperature of 1000℃. Wear-resistant, shock-resistant, peel-off, firm, and durable.
- Convenient on-site construction. Spraying is not affected by seasonal climate and temperature and is quick and convenient.
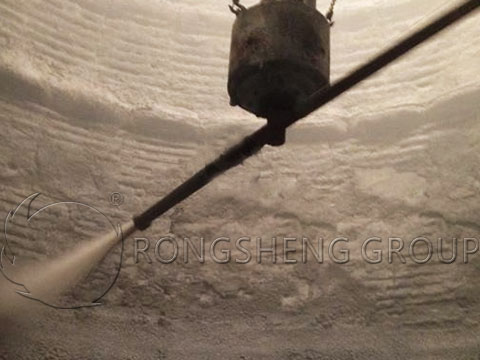
Get Free Quote
Common Spraying Methods of the Gunning Mix Coatings
Gunning Mix is sprayed with a spray gun to spray the refractory mixture onto the sprayed surface, that is, the materials used for spraying are called refractory gunning mix. Spraying is carried out by spraying machine or spray gun, which is a new process in furnace building and repairing. Refractory Gunning Mix relies on compressed air or mechanical pressure in the pipeline to obtain sufficient speed and then spray onto the sprayed surface through the nozzle to form a firm spray coating. The spraying methods are divided into three types: wet method, dry method, and flame method. According to the state of the receiving surface of the material, it is divided into two types: cold material spraying method and molten material spraying method.
Wet spraying refers to the refractory gunning mix sprayed onto the sprayed surface after adding water or liquid binder. According to the order of adding water or liquid binder and its dosage, it is divided into four types: mud method, wet method, semi-dry method, and false method. Among them, every two methods are mixed and used, it is called a hybrid method. The mud method is to mix the refractory mixture into mud before spraying and is mainly used for thermal gunning furnace lining. In the wet method, the refractory mixture is mixed into pumping mud and then sprayed. The semi-dry method is to first add a small amount of water to the refractory mixture to mix it evenly, transport it to the nozzle and add the remaining water before spraying. The false dry method is to mix the refractory mixture through a mixer, and then transport it to the nozzle to add water for spraying. The latter three methods are suitable for spraying furnace construction or gunning furnace lining.
Dry spraying means that the mixed refractory gunning mix is sprayed directly onto the sprayed surface through the nozzle, and is mainly used for repairing the furnace.
Flame spraying is to uses oxygen to transport the mixed refractory gunning mix to the nozzle where it meets the combustible gas and sprays it together. The combustible gas is burned, and the material travels in the flame and melts into a plastic state, and shoots onto the sprayed surface. This method is mainly used for thermal gunning furnace lining, with less damage to the original lining, easy sintering of the spray coating, long service life, but high cost. In other methods, a plasma gun is used to melt or semi-melt the refractory mixture and spray it onto the sprayed surface, and spray the molten slag in the furnace with an appropriately adjusted composition onto the lining body. The slag splashing method also belongs to this type of method.
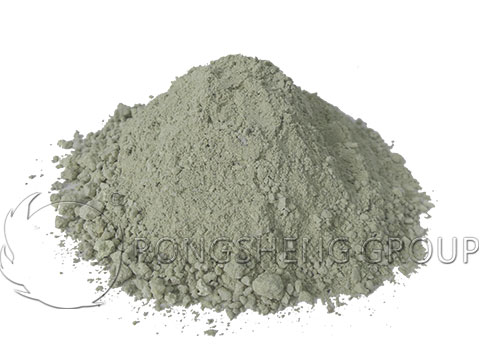
Get Free Quote
How to Apply the Gunning Mix Coating
There are many spraying methods, but spray guns are usually used for spraying. In the spraying process, external factors are mainly affected by the construction, the operating proficiency of the construction personnel, and the spraying equipment. The internal factors are mainly affected by the rebound rate and adhesion rate of the spray paint. Therefore, the construction of refractory gunning mix coatings is a technical job.
The particles of the refractory gunning mix cannot be larger than 5mm. Because when it is larger than 5mm, the spray gun will be blocked and normal construction will not work. During construction, the refractory gunning mix is sprayed 40-50mm in the pipeline, and the spray coating can be formed quickly. Under normal circumstances, the rebound rate of the refractory gunning mix manufacturer is 10%.
In the refractory gunning mix, the fine particles in the process can greatly improve the adhesion rate, but it will increase the peeling during drying. Coarse particles can make the coating layer more stable, but too many coarse particles will result in a high rebound rate and increase the amount of material used. Therefore, the particle gradation must be reasonable and cannot exceed 5mm. Because it exceeds 5mm, the spray gun cannot spray. Reasonable gradation can best improve the construction and use performance of gunning mix.
In the spraying construction process, the gunning mix should be determined according to the type of gunning mix and the outlet pressure. The nozzle of the spray gun and the spray surface are kept in a vertical direction, that is, the gunning mix is directed at the spray surface. Due to the large mass of the aggregate of the gunning mix, it is easy to rebound when it moves in the middle of the spray stream. If the rebound rate is too large, not only will the cost increase, but the use effect will also be affected.
When the distance between the nozzle of the spray gun and the sprayed surface is determined, the spray gun should move in a circular trajectory and its diameter should be controlled between 30-40m. The spraying layer is sprayed to the design thickness at a time, and the spraying area should not be too large, generally controlled at 1.0~1.5m2. After spraying, expand to the surroundings.
When the refractory gunning mix is stirred, add 2% to 4% water to prevent the powder from flying during the transportation process. The rest of the water is added to the mouth of the spray gun. The water consumption of dense and light refractory gunning mixes is 10% to 14% and 12% to 20%, respectively.
When the pressure and distance of the gunning mix from the nozzle of the spray gun are fixed, the water consumption should be the best that the gunning mix does not flow, and the water consumption should be stable. On the premise of ensuring the quality of the spray coating, add as little water as possible to obtain a spray coating with good performance.
The spraying sequence is carried out from top to bottom, and the application is divided into pieces. At intervals of 1~2m, there should be expansion joints with a width of 1~3m. If the spraying construction is interrupted, it should be at the expansion joint or made into a stepped stubble.
When the sprayed layer has not initially set, use a knife to cut expansion joints or stepped stubble. When the spray coating has just set, use a knife to trim the surface. In case of looseness, dryness, etc., it should be removed in time and sprayed again.
After the gunning mix is sprayed, wait until the natural curing to the initial setting, before spraying water for wet curing for 3 days.
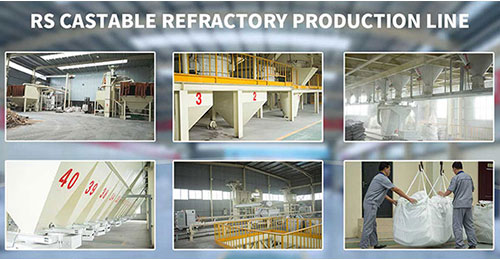
Contact Rongsheng
Rongsheng Refractory Manufacturer
Rongsheng is an experienced refractory material manufacturer and sales company. Rongsheng’s refractory bricks and monolithic refractories products have been sold to more than 60 countries around the world, and have received unanimous praise from customers. Rongsheng Environmental Protection’s advanced and fully automatic unshaped refractory production line has an annual output of tons. Our monolithic refractory production workshop has completed the supply of refractory materials for a turnkey project. And the customer’s project is running stably. This has increased the visibility of our Rongsheng refractory manufacturer. It has strengthened our confidence in making monolithic refractories better. Our unshaped refractory production line not only provides standard unshaped refractory products for various thermal furnace equipment but also can customize refractory products according to the specific production needs of customers. To learn more, please contact us.