Porosity and bulk density in refractory bricks. The percentage of the volume of pores in refractory products to the total volume of refractory products is called porosity. The level of porosity also indicates the density of refractory products.
Porosity of Refractory Bricks
The pores in refractory materials can be divided into three types according to their different forms of existence. The pores in refractory products that are connected to the atmosphere are called open pores, and the pores that penetrate them are called connected pores; the pores that are not connected to the atmosphere are called closed pores.
- Closed pores: pores enclosed in refractory bricks and not connected to the atmosphere;
- Open pores: One end is closed in the refractory brick, and the other end is connected to the atmosphere and can be filled with fluid;
- Through pores: pores that are not only connected to the atmosphere but also penetrate both sides of the refractory brick and can allow fluid to pass through.
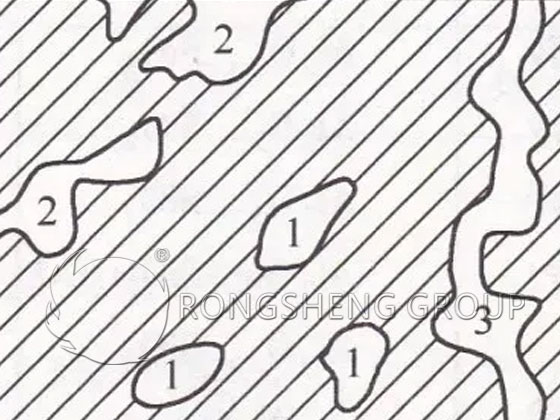
For simplicity, the three types of stomata are usually combined into two categories, namely closed stomata and open stomata, with the latter including through stomata. Since open pores can directly come into contact with external media such as liquid (slag), gas, and other substances during the use of refractory products, their impact on the product is more serious than closed pores.
The volume of closed pores cannot be directly measured, so the porosity index of the product is often expressed as open porosity or apparent porosity. Apparent porosity is the ratio of the volume of all open pores in refractory bricks to its total volume. The percentage of the volume of all pores in a refractory product to the total volume of the refractory product is called true porosity, also known as total porosity. The percentage of the volume of open pores and through pores in the total volume of refractory products is called apparent porosity, or false porosity. The requirements for the apparent porosity of various refractory materials are specified in national standards or industry standards.
The Relationship Between Porosity and Bulk Density in Refractory Bricks
Porosity is the percentage of the pore volume contained in refractory bricks to the total volume of the product. That is to say, the higher the bulk density, the smaller the porosity. The apparent porosity of heavy refractory bricks is generally between 10% and 28%. Standardly, only products with less than 16% can be called low porosity products. However, as raw material resources become less and less, and aluminum ore is harvested, the ingredients are not artificially added and fired. Therefore, in the actual production process, heavy refractory bricks with less than 20% are called low-porosity bricks.
Porosity is the basic technical indicator of refractory bricks. Its size affects the performance of refractory bricks, especially strength, thermal conductivity, slag resistance, and thermal shock resistance. As the porosity increases, the strength decreases. Low porosity is beneficial to the load-softening temperature and creep properties of refractory bricks. However, the effect of porosity on thermal shock resistance is more complicated, and the thermal shock resistance is better when the porosity is within a certain range. However, too low porosity is not good for thermal shock. Not all indicators are high or low.
To produce dense refractory bricks with low porosity, raw materials with low porosity must be selected. Formulate a reasonable particle gradation, rationally use binders, and mix thoroughly and evenly. High-pressure molding and increasing the firing temperature, and then extending the holding time to reduce porosity. In the amorphous castable, adding ultra-fine powder and dispersant can form a closer packing and obtain products with low porosity.
The relationship between volume density and porosity in refractory bricks is that the higher the volume density, the smaller the porosity will be.
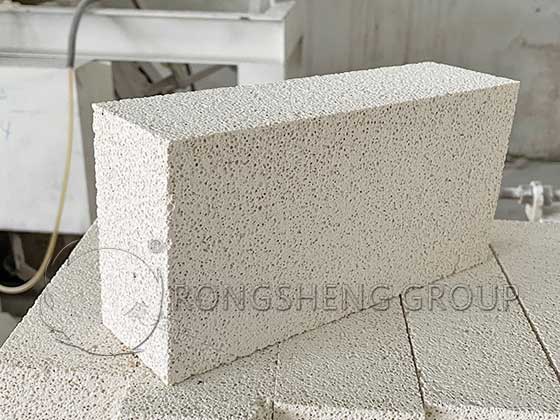
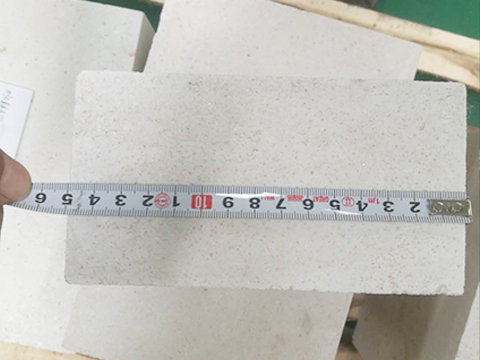
What is the Significance of Measuring Porosity?
Porosity is the basic technical indicator of most refractory materials. Its size affects almost all properties, especially strength, thermal conductivity, slag resistance, and thermal shock resistance. As the porosity increases, the strength decreases, not only because the solid cross-sectional area decreases, but the actual stress increases. More importantly, pores are defects in the material, which can cause stress concentration and reduce strength. The impact of large pores is more significant. Increased porosity can significantly reduce thermal conductivity, and large porosity increases the penetration of slag into products.
The Porosity of Heavy Refractory Bricks and Its Influencing Factors
The porosity of heavy refractory bricks refers to the volume proportion of pores in the brick body, which affects its fire resistance and thermal insulation properties.
The significance of porosity of heavy refractory bricks. As an important material in high-temperature industrial kilns, heavy refractory bricks’ main functions are to withstand high temperatures and chemical corrosion and to insulate and maintain heat. The porosity is one of the key factors affecting its fire resistance and thermal insulation performance. If the porosity is too high, the brick density will decrease. Thermal stress and thermal shock cracks are prone to occur when temperature changes, thereby reducing its compressive strength and service life. If the porosity is too low, it will be difficult for the bricks to maintain sufficient thermal insulation performance in high-temperature environments, affecting the production efficiency and quality of the kiln.
Therefore, the porosity of heavy refractory bricks needs to be strictly controlled and rationally designed. The factors that affect the porosity of heavy refractory bricks include the following aspects.
- Selection of raw materials. The raw materials of heavy refractory bricks include clay, high-aluminum materials, etc. Different raw materials have different effects on the porosity of bricks. For example, high-alumina bauxite is easy to sinter at high temperatures and can reduce porosity. Organic substances such as graphite will produce gas and increase porosity.
- Control during the firing process. Factors such as firing temperature and time also have an important impact on the porosity of heavy refractory bricks. Excessively high firing temperature will cause the brick body to be over-sintered and reduce the porosity. However, too low a firing temperature will lead to incomplete sintering of the bricks and an increase in porosity. Firing times that are too long or too short can also affect porosity.
- Use of additives. Additives such as graphite and polyethylene can produce gas during the firing process and increase the porosity of the bricks.
In summary, the porosity of heavy refractory bricks is an important factor affecting their performance. Optimum results need to be achieved through reasonable material selection and firing process control.