Carbon-containing refractory ramming materials are widely used in the tapping trenches and slag-tapping trenches of blast furnaces. Its lifespan is that the one-time iron flux without repair is more than 50,000 tons, and after 3 to 5 repairs, the iron flux can reach several 100,000 tons. The main application of ramming material for blast furnace iron and slag trenches can be used for large and medium blast furnace tap trenches. It includes slag lines and molten iron lines, etc. It is also suitable for tapping trenches and slag-tapping trenches of medium and small blast furnaces.
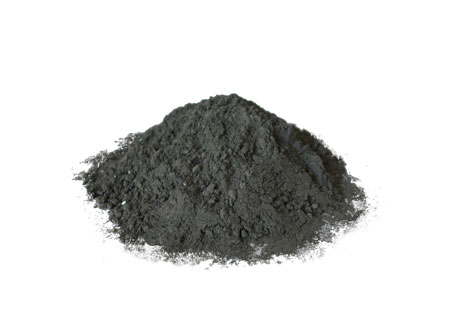
The Main Application of Carbon-Containing Refractory Ramming Material
In large and medium-sized blast furnace bottom cushions and carbon brick gaps and other parts, use carbon ramming material to ram. Cushion ramming material is crushed with graphite blocks and used as aggregate. The carbon content of the material is greater than 90%, the drying bulk density is greater than 1.5g/cm3, and the thermal conductivity is about 14W/(m·K). The caulking refractory ramming material is an advanced material containing silicon nitride, and its Si3N4 content is about 20% and SiC is about 16%. The drying bulk density is generally 1.70~1.76g/cm3, the drying flexural strength is 4~7MPa, the high-temperature flexural strength at 1400℃ and the linear shrinkage after burning are about 2.4~2.9MPa and 0.3% respectively. There is also carbon ramming material used in the hearth. The carbon content is more than 15%, Al2O3 is about 15%, and SiO2 is about 60%. The drying bulk density of the material is about 1.8g/cm3, and the thermal conductivity is generally 1.3W/(m·K). In addition, carbon refractory ramming materials are used for cold ramming linings in thermal equipment such as hearths, furnace bottoms, and aluminum electrolytic cells of medium and small blast furnaces, which are widely used.
Compared with the traditional hot carbon ramming material, the working conditions are improved and the performance of the lining body is improved. This material is also called cold-rammed carbon material, and its maximum particle size is 10mm. The properties after sintering at 1350 ℃, the bulk density is 1.45g/cm3, the volume shrinkage rate is 1.3%, the apparent porosity is 21%, the compressive strength is 27MPa and the thermal conductivity is 2.55W/(m·K). This type of refractory ramming material generally uses organic compounds such as phenolic resin and asphalt as binders, and the dosage is 5% to 13%. At the same time, admixtures such as preservatives and curing agents are added.
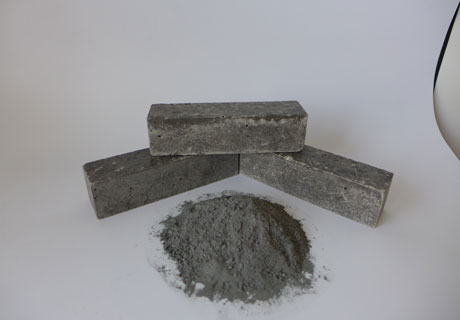
In thermal equipment such as large hot weathering iron furnaces, carbon-containing refractory ramming materials are also used in some parts. The material generally uses dense white corundum and brown corundum and is compounded with super or first-grade bauxite clinker as refractory aggregate and powder. Some add a small amount of zircon fine particles to improve performance. Carbon materials generally use SiC, flake graphite, earthy graphite, pitch coke, etc., and the total amount is 10% to 25%. Commonly used binders are generally phosphoric acid, aluminum phosphate and binding clay, etc., used alone or in combination, and the dosage is 8% to 11%. At the same time, admixtures such as acid inhibitors, surfactants, and preservatives should be added.
In the aluminum zirconium carbon refractory ramming material, the experiment of adding metal silicon powder was carried out. The results show that the refractory ramming material added with silicon metal powder has a high-temperature pressure resistance and flexural strength of 24MPa and 5MPa respectively at 1500℃. The strength of the refractory ramming material without the addition of metal silicon powder is about 164% and 113% higher, respectively. Therefore, in the carbon-containing refractory ramming material, adding metal silicon powder can improve the strength, and also improve the slag resistance and oxidation resistance.
In the carbon-containing refractory ramming material, adding SiO2 ultrafine powder, a comparative test was also carried out. The dosage of SiO2 ultrafine powder is 2%. After Al2O3 – SiC – C refractory ramming material is mixed with SiO2 ultrafine powder, the bulk density and drying strength are basically the same as those without addition. This shows that the addition of SiO2 ultrafine powder in this type of refractory ramming material has no obvious effect.
Carbon-containing refractory ramming materials are generally prepared in refractory factories. That is, various raw materials are weighed according to the mixing ratio, and then wet-mixed evenly in a wheel mill or a forced mixer, without the need to squeeze the mud. The shelf life of the material is generally 3 months. That is, within 3 months of the storage period, the ramming material should still have good plasticity to facilitate ramming construction.
It can be seen from the performance curve of the aluminum zirconium carbon ramming material during the storage period that with the prolongation of the storage time, the water escapes, resulting in a decrease in the compactness of the ramming body. Therefore, the strength also decreases. Within 3 months of the storage period of the ramming material, there is still good viscoplasticity, which can be rammed for construction, and generally does not affect the use.
In addition, carbon-containing refractory ramming materials are also used in thermal equipment such as steelmaking electric furnaces. For example, magnesia is used as refractory aggregate and powder, mixed with 10% metallurgical coke powder and other carbon materials, and coal tar, dehydrated coal tar or brine, and other materials are used as binders. The working layer of the furnace bottom and embankment slope of the smelting pool is rammed on-site to meet the technical requirements of the production process.
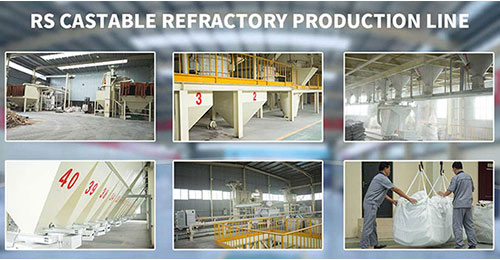
Rongsheng Refractory Materials Manufacturer
Rongsheng Refractory Manufacturer is a refractory manufacturer with rich experience in production and sales. Not only has an advanced production line that is environmentally friendly in the production of unshaped refractory materials, but also has a production line of high-quality refractory bricks. To buy carbon-containing refractory ramming materials, and high-quality refractory brick products, please contact us. We will provide you with high-quality refractory lining materials according to your production needs.