As the proportion of external refining and alloying processes in the steelmaking process is getting higher and higher, the importance of refractory materials for ladle working linings is becoming more and more prominent. The role and influence of refractory materials used in ladle working lining on inclusions. Due to the difference in material composition and structure, the physical and chemical properties of refractories for ladle lining and their reactions with molten steel and steel slag are the most concerned directions in the research of ladle lining refractories. Rongsheng refractory manufacturers can provide phosphate-combined high alumina ramming material, phosphate-bonded high alumina refractory plastic, phosphate-combined refractory ramming material, phosphate-bonded high alumina bricks for ladles and steel drums. Combined with several high-alumina refractory materials in the application of ladles, steel drums, etc., conducted a comparative analysis.
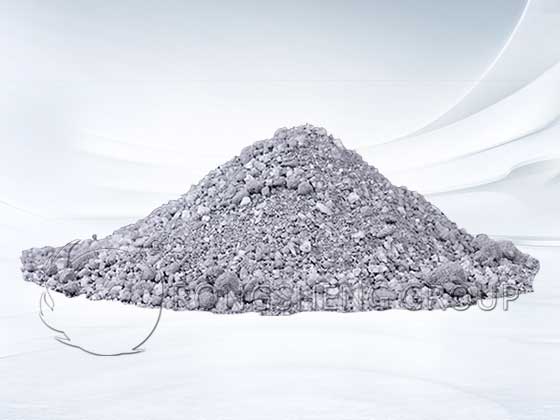
Phosphoric Acid Combined High Alumina Ramming Material for Steel Drum
A steel mill has produced phosphoric acid combined with high alumina ramming material for steel drums. The proportion (w) is: 60%~65% of the Ⅱ contour bauxite clinker of ≤8mm, and 35%~40% of the I contour bauxite fine powder of <1.25mm. The mass concentration is 40%~50% and the industrial phosphoric acid is 7%~10%. The measured moisture is 6%~7.5% in summer and 5%~6.5% in winter. The trapped material time is greater than 16h. When the material is dry, it can be used after wetting with dilute phosphoric acid with a mass concentration of 25%~35%. For tamping and molding, the wind pressure of the tamping machine is 0.5MPa. The performance of this high alumina ramming material is as follows: the compressive strength at 1100°C is 59.9MPa. At 1450°C, the apparent porosity is 24.9%, the bulk density is 2.32g cm-3, and the compressive strength is 54.7~57.7MPa.
Phosphoric Acid-Bonded Ramming Material for Ladle Linings for Converters
A steel mill used super-grade bauxite clinker to produce phosphoric acid-bonded ramming material for ladles used in converters. The ratio is: 8~3mm, 40%~50%; ≤3mm, 30%; <0.088mm, 20%~30%. The concentration of industrial waste phosphoric acid added is 45%~51%, and the amount added is 10%~12%. Mixing is carried out in a J4-1500 liter forced mixer, each feed is 1.5~2t, and dry mixing is 2~3 min. After the granules and powder are evenly mixed, slowly add phosphoric acid and wet mix for 4-6 minutes. In order to prevent agglomeration, the phosphoric acid should flow slowly without stopping. The dry humidity of the material should not be agglomerated after being loosened by hand.
Tamping uses 2~3 D10-11720 tamping machines. Use a 1.5-inch high-pressure rubber hose to connect the compressed air nozzle and the air hammer handle, and the air pressure is 0.4~0.5MPa. Set the mold core (wooden mold or steel mold) in the ladle. The ladle is 1800mm high, and the mold core is composed of three sections, each section is 560mm high. Put the first section first, and make the distance between the mold wall and the bag wall equal to 160mm. Then the cloth is evenly distributed in a circle with a thickness of about 100mm, and two people manipulate the wind hammer to pound along the circle. When the reduction is 50mm, carry out the second cloth tamping. When the first section of the mold core is flattened, put down the second section of the mold core and the third section of the mold core, distribute the material in turn, and pound until the mouth of the bag. It is not advisable to stop in the middle of knotting and take off the mold core after knotting. The bulk density of the knotted layer is 2.09~2.13g.cm-3. Bake with gas baking equipment, first bake on low fire (200°C) for 4 hours, medium fire (300~400°C) for 4 hours, and high fire (600°C) for 8 hours, and use it in time after baking.
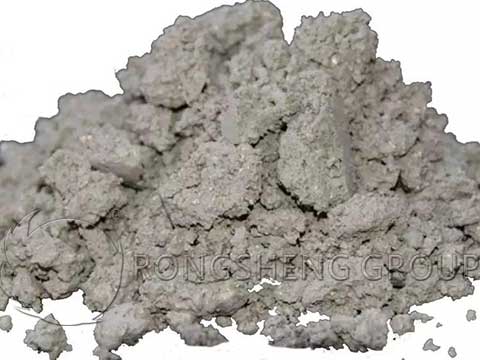
High Alumina Plastic Refractory Material for Electric Furnace Top
The high-alumina plastic refractory material is used for the electric furnace top, and its raw materials are super-grade high-alumina bauxite clinker <5mm, fused corundum fine powder, and Suzhou porcelain clay. Phosphoric acid is used as a binding agent and oxalic acid is used as a preservative. The storage period of the plastic refractory material is 3 months, and the flexural and compressive strengths are improved after 15 days of storage. At 30d decreased slightly and then remained basically unchanged until 90d when there was a significant decline.
Influence of High Alumina Refractory Materials Used for Working Lining of Ladle on Molten Steel
With the gradual improvement of modern industry’s requirements for steel quality, the refining methods of molten steel tend to be diversified. In order to meet the refining needs in different periods, the development of refractory materials for ladle working lining has also undergone several important changes. From high alumina brick system, carbon composite system, corundum-spinel castable system, and calcium oxide system, the respective characteristics of these four typical refractory materials.
High alumina bricks are refractory materials. From the early 1960s to the late 1970s, clay bricks (mainly composed of aluminosilicate) have been the main choice of refractory materials for ladle lining in my country. But its service life is low, consumption is big. During the same period, foreign ladles have begun to use high-alumina bricks as the main lining bricks. From the late 1970s to the early 1990s, with the improvement of my country’s steelmaking process and the development of smelting technology to a certain extent, high alumina bricks were gradually adopted by steel mills. The acquisition of high alumina bricks is mainly based on natural bauxite. At that time, when the conditions of use were not too harsh, there was no refining or the refining treatment time was very short, and the life of the high-alumina brick lining was only about 20 to 30 times.
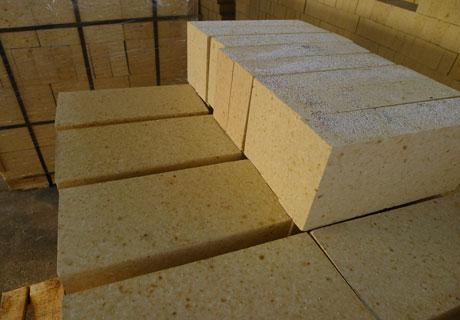
In order to improve the service life of the ordinary high alumina brick working lining, people use methods such as increasing the content of Al2O3 or adding zircon and andalusite powder. The principle is to improve the slag resistance of the material by increasing the refractoriness and load-softening temperature of the high alumina brick. Using this high-alumina brick as a refractory material for ladle lining has a longer service life than ordinary high-alumina bricks. After the improved high alumina brick is in contact with molten steel, a high melting point reaction layer with corundum and mullite as the main minerals will be formed. However, it also contains a higher amount of liquid phase at high temperatures. These shortcomings lead to high alumina bricks being easily infiltrated by molten steel and slag during service in the face of thermal shock, forming a thicker permeable layer. It is easy to hang slag and peel off, resulting in uneven damage to the lining. Subsequently, researchers successively introduced chemically bonded high-alumina bricks, phosphoric acid or phosphate-bonded high-alumina ramming materials, and high-alumina castables to improve the anti-stripping performance of materials. Thereby further improving the service life of the high aluminum ladle lining. However, these treatment methods often have adverse effects on the quality of molten steel, such as phosphoric acid or phosphate will be introduced into the steel.
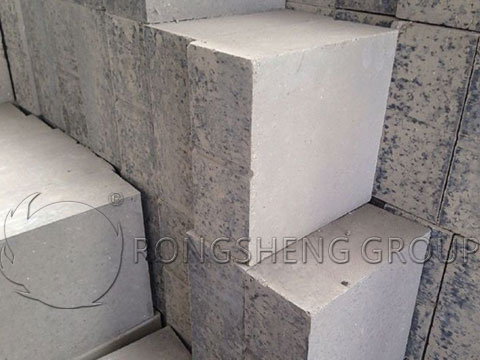
With the increase of refining temperature and the extension of refining time, the problem of the low life of high alumina bricks gradually becomes insurmountable. In addition, SiO2 in high-alumina brick-based refractory materials will inevitably lead to a “Si” increase in molten steel during service. Due to the limitation of short service life and pollution of molten steel, high alumina brick refractory materials are gradually replaced by other refractory materials in the field of ladle lining.
Rongsheng Refractory Material Manufacturer
Rongsheng refractory material manufacturer is a refractory material manufacturer with rich production and sales experience. We have an independent refractory brick factory and an environmentally friendly monolithic refractory factory. Our third factory is also under construction preparations to better serve our customers. Our high alumina refractory products include not only various series of high alumina brick products but also various types of high alumina monolithic refractory castable products, etc. Our phosphate-bonded high-alumina refractory materials are used by customers with good results. Contact us to get prices and samples for free.