Refractory concrete is made up of refractory aggregates, powders, and cement, added with water or other liquids and is an unshaped refractory material used directly without calcination. Refractory concrete and refractory castables belong to the category of unshaped refractory materials. There are hundreds of refractory castables and they are widely used. So, what are the application areas of refractory concrete? Castable refractory concrete manufacturers will introduce the application range of refractory concrete from some aspects such as the particle grading requirements and bonding methods of refractory concrete. Free Quote from Rongsheng Now!
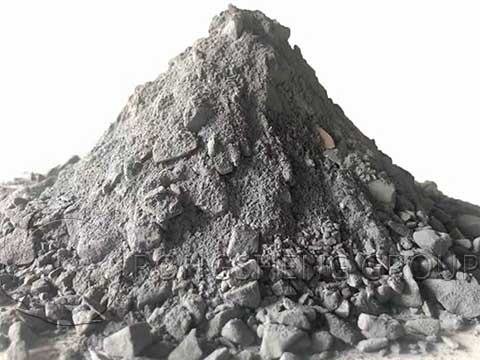
Particle Grading Requirements of Refractory Concrete
The same material should be used for aggregate and powder in refractory concrete. Aggregate and powder must be calcined clinker. The particle size of aggregate particles can generally be divided into two levels, with large particles ranging from 5 to 15 mm and small particles below 5 mm. When the thickness of the concrete layer is less than 60mm, the aggregate can adopt the following gradation: 6~8mm accounted for 20%; 3~6mm accounted for 20%; 1~3mm accounted for 35%; less than 1mm accounted for 25%.
What are the Application Areas of Refractory Concrete?
Refractory concrete is suitable for use in the furnace bottom, blast furnace hearth, the foundation of thermal equipment, soaking furnace, heating furnace, chimney, and other areas. application areas of refractory concrete. Refractory concrete has three bonding methods: cement bonding, water glass, and phosphoric acid bonding.
The cement-bonded refractory concrete has high strength and good thermal shock stability. It can be used at a temperature of 1200°C, and those with high aluminum content and high bulk density can be used at 1400°C.
Water glass concrete is air-hardening refractory concrete, which can be dried directly after demoulding. Used at 900~1000℃. Because of its high mechanical strength, thermal stability, and wear resistance. It is suitable for engineering use under the action of acid (except hydrofluoric acid) at high temperatures. Especially in the application part of water vapor and water.
Phosphoric acid-bonded refractory concrete is a fire-hardening refractory material, and it can be dried directly after construction and shaping. The characteristic is that it can be used at a high temperature of 1450~1650℃. Good thermal stability, wear resistance, and impact resistance. However, the price of concrete combined with cement and water glass is higher. It is suitable for soaking furnace, high-temperature area of heating furnace, and high-temperature area of the oil-burning combustion chamber.
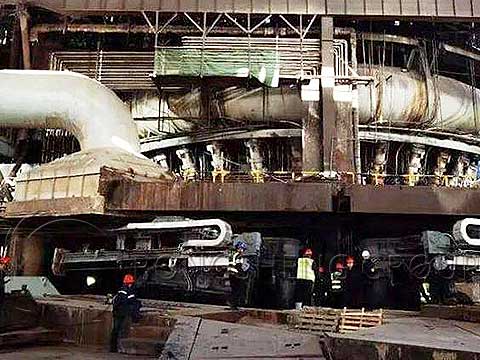
The Difference between Refractory Concrete and Heat-Resistant Concrete
The biggest difference between refractory concrete and heat-resistant concrete is the operating temperature. The use temperature of heat-resistant concrete is between 500-900℃. Refractory concrete is used in high-temperature areas, and the service temperature is above 1250°C.
Refractory concrete is produced by combining high-aluminum clinker particles and powder, as well as different proportions of binder and cement. The matrix of heat-resistant concrete is the same as that of fire-resistant concrete, but the grade is lower. However, it is not the same field as the general concrete used at around 250°C.
Ordinary concrete is often used for pavement repair. Refractory concrete and heat-resistant concrete are unshaped castables in the field of refractory materials. Refractory concrete is divided into neutral, acidic, and alkaline.
What are the Advantages of Refractory Concrete Compared with Refractory Bricks?
Refractory concrete and refractory bricks are both high-temperature-resistant materials and are commonly used refractory materials in industrial kilns. One of them belongs to unshaped refractories, and the other belongs to shaped refractories. So what are the advantages of refractory concrete compared with refractory bricks?
Refractory castable concrete is a mixture of different granular granular materials and cementitious materials. The shaped material obtained by adding a certain proportion of water to mixing, forming, and hardening during use is a sinter-free product. Refractory bricks are formed by forming, drying, and sintering mud materials of different materials, which are sintered products. Compared with refractory bricks, refractory concrete simplifies the manufacturing process, reduces production costs, and enables the furnace equipment to have good integrity and performance. And also, refractory castable concrete has the following advantages in terms of performance.
- ①The refractoriness is close to or slightly lower than the refractory bricks of the same material.
- ②The softening temperature under load is much lower than that of refractory bricks of the same material.
- ③The linear expansion coefficient is small. Because the cementitious material has the effect of sintering shrinkage during the thermal processing, which offsets the thermal expansion of the aggregate.
- ④ High strength at room temperature.
- ⑤The chipping resistance (thermal shock resistance) is better, which is better than the refractory bricks of the same material.
- ⑥The apparent porosity is slightly lower than that of refractory bricks. But there are many closed pores, so the density is not as good as refractory bricks.
- ⑦The shrinkage of the re-burning line is generally larger than that of refractory bricks.
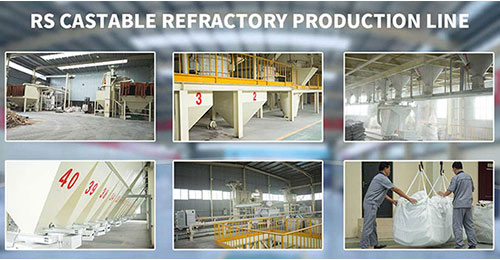
Rongsheng Castable Refractory Concrete Manufacturer
Rongsheng refractory material manufacturer is a refractory material manufacturer with rich experience in production and sales. Rongsheng’s environmentally friendly, advanced, and fully automatic monolithic refractory production line has an annual output of 80,000 tons of monolithic refractories. Rongsheng has its own characteristics in the production and research and development of castable refractory concrete. We can customize the refractory material formula for the customer’s refractory lining according to the actual working conditions of the customer’s refractory lining. Among our customers in more than 60 countries, most of them continue to customize refractory lining products from Rongsheng manufacturers. If you need to buy high-quality high alumina refractory concrete products, please contact us.