Phosphate refractory castable is a castable combined with phosphoric acid, which belongs to an acidic matrix and has a service temperature of 1400-1600°C. For phosphate castables, the concentration of phosphate binder is 40%-60%, and the dosage is 10%-14%. Phosphate cement is commonly used as a setting accelerator, with a dosage of 0.5%-3.0%. A certain proportion of magnesium oxide fine powder is also added.
Raw Material Configuration of Phosphate Refractory Castables
Phosphate refractory castables use clay clinker or alumina aggregate clinker as refractory aggregate and powder, and their dosages are 65%-74% and 24%-35% respectively. The commonly used ratio is that the refractory aggregate is aggregate with a particle size less than 15mm, and the particle gradation is 15-50mm50%, 5-2.5mm, and less than 2.5mm26%. The refractory powder fineness is greater than 80% when it is 0.09mm. The setting accelerator is CA-50 high alumina cement, and its dosage depends on the construction conditions and normal temperature strength requirements. The general dosage is about 2%. When the ambient temperature is low, the dosage should be appropriately increased. When normal temperature strength is not required, less CA-50 cement can be added without adding fire.
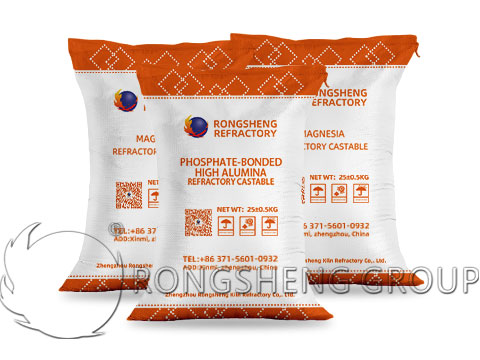
Phosphate refractory castables do not react with aluminum silicate materials except iron at normal temperatures. During construction, heating is required to dehydrate and condense the bonding agent and adhere and cement the bone powder materials together to obtain room temperature strength. When magnesium oxide fine powder is added, it reacts with phosphate, causing the refractory castable to solidify and harden. When aluminate cement is added, water-containing monocalcium phosphate or dicalcium phosphate is formed. The physical and chemical changes of phosphoric acid and phosphate refractory castables during the heating process are very complex. It reacts with refractory powder or additives to generate phosphate, which is further dehydrated and converted into metaphosphoric acid or phosphate. As the temperature continues to increase, polymerization, polycondensation polymerization, first-level cementation and adhesion will occur. At the same time, a ceramic bond is formed, allowing the refractory castable to obtain better high-temperature properties.
Application of Phosphate Refractory Castables
As a high-temperature refractory material, phosphate refractory castable is usually used in industrial fields such as high-temperature reactors and smelting equipment. Phosphate castables are also used in heating furnaces and soaking furnaces for heating metal, and can also be used in coke ovens, etc. Is phosphate refractory castable easy to use?
Advantages and Disadvantages of Phosphate Refractory Castables
Phosphate refractory castables have many advantages.
- First of all, phosphate refractory castables have high refractoriness and good thermal insulation properties. This material can maintain stable physical and chemical properties at high temperatures, and can effectively protect the quality and performance of steel and other metal materials in high-temperature environments. At the same time, due to its good thermal insulation performance, it can effectively reduce energy consumption and reduce energy waste.
- Secondly, phosphate refractory castables also have good wear resistance and corrosion resistance. In high-temperature environments, this material can resist corrosion and wear from various chemicals, thereby extending the service life of the equipment. In addition, due to its good wear resistance, the frequency of equipment maintenance and replacement can be reduced, thereby reducing operating costs.
- In addition, the construction of phosphate refractory castables is simple and easy. Compared with traditional refractory bricks, this material does not require complex construction and installation processes and can be easily poured into equipment, thus greatly shortening the construction period and reducing construction costs.
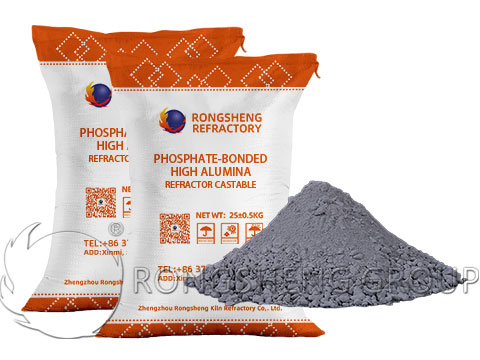
Although phosphate refractory castables have many advantages, there are also some problems.
- First of all, the preparation of phosphate refractory castables needs to take into account various factors such as the selection, proportion, and process conditions of raw materials, and requires a high technical level.
- Secondly, during use, phosphate refractory castables will also be affected by high temperature, wear, and other factors, and their service life requires regular testing and maintenance.
Preparation Method of Phosphate Refractory Castable
The preparation method of phosphate refractory castables is generally dry or wet. In the dry preparation, raw materials such as kaolin, phosphate, and swelling agent are mixed evenly, then mixed and stirred by adding an appropriate amount of water and binder, and then dried, screened, ground, and other processes to obtain refractory castables. In wet preparation, the raw materials are mixed first, and then an appropriate amount of water is added for stirring and shaping. This preparation method can significantly reduce production costs and save energy.
Storage and Use of Phosphate Refractory Castables
There is a big difference between indoor storage and open-air storage of phosphate refractory castables. If such castables are stored in a warehouse, the normal temperature compressive strength will increase as the storage time increases. The strength of castables stored in the open air will slowly decrease after construction and maintenance. Moreover, the strength of phosphoric acid refractory castables stored indoors will be more than ten MPa higher than that stored in the open air. The compressive strength after burning is also more than 10Mpa better than the strength in the open air. Therefore, it must be stored indoors. Especially in winter, avoid storing it in the open air as the temperature fluctuates and forms a dry-wet cycle, which reduces the performance of phosphate refractory castables.
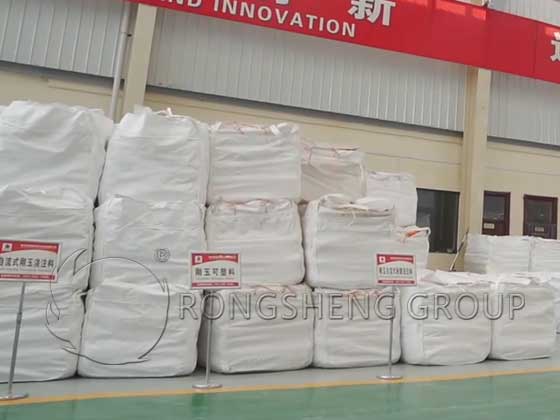

Phosphate refractory castables must be trapped before use, so that the use effect can be better and the cycle can be longer. Under normal circumstances, a certain proportion of binder is added to the aggregate and matrix. After stirring for a few minutes, the material is trapped for more than 16 hours. Especially during formal construction, the binder is added to the trapped castable and continued stirring. Construction can begin in about 3 minutes. The fluctuation of the trapped material time can also be adjusted and determined based on the chemical reaction speed between the cement and the refractory aggregate and powder, and the difference in the temperature of the construction environment.
When trapping materials, pay attention to mixing 3/5 of the refractory aggregate and powder and cementing agent evenly. Cover the trapped material site with plastic sheeting to prevent the cement from evaporating. The trapped material should not be in contact with water. The temperature of the trapped material should be above 15°C and left to stand for 12-16 hours. The binding agent fully reacts with the metal in the refractory aggregate and powder to release hydrogen.
Sometimes, the amount of phosphoric acid solvent can be appropriately reduced and an appropriate proportion of inhibitors can be added to increase the molding pressure. Although the storage environment of such castables has an impact on the normal temperature performance of phosphoric acid refractory castables, it has little impact on the high-temperature performance and does not affect its use. Therefore, after the setting accelerator is added and the castable hardens, the requirements for the storage location are not too strict. Refractory castables without accelerator must be heat treated before they can be stored. Without heat treatment, deliquescence will occur, which is not conducive to use.
When the temperature of the place where the phosphoric acid refractory castable is stored is too low, white crystals will precipitate on the surface of the castable. If white hair appears, it is the precipitation of aluminum salts and calcium salts.
If it is heated at high temperature or for a long time, the aluminum salt and calcium salt will transform into insoluble salts, and the “white hair” will disappear. In this case, the performance of phosphoric acid refractory castables is not affected. However, if there is too much precipitation, the internal structure of the castable will become loose and the strength will be reduced. Therefore, you must pay attention to storing it indoors, and pay attention to the temperature during storage, which cannot be too low.
Buy Phosphate Refractory Castables
Refractory furnace lining solutions. Purchase high-quality refractory lining materials. Please choose Rongsheng refractory material manufacturer for high-quality refractory products and perfect customer service. Contact us for a free quote and sample of phosphate refractory castables.