Mullite thermal insulating refractory bricks, This series of products are made of mullite as the main raw material and sintered at high temperature by a special process. It has the advantages of high-temperature resistance, high strength, low thermal conductivity, and direct contact with flames. It is suitable for various industrial kiln linings and heat insulation layers, and the operating temperature is 1300°C. As an excellent refractory material, mullite brick has the advantages of high-temperature resistance, chemical corrosion resistance, good thermal conductivity, low thermal expansion coefficient, and easy forming and installation. These advantages make mullite series refractory bricks widely used in iron and steel smelting, the glass industry, the electric power industry, the chemical industry tunnel kiln, and other fields. With the continuous development of technology, mullite bricks will continue to exert their advantages to meet the needs of high-temperature refractory materials in different fields and provide stable and reliable guarantees for industrial production.
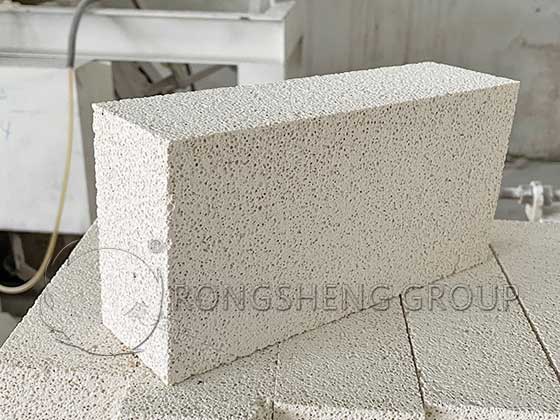
Mullite Series Refractory Brick
In the field of refractory materials, refractory bricks with mullite phases can be called mullite refractory bricks. The following are several common mullite series refractory bricks. Rongsheng refractory material manufacturers can customize the index parameters and sizes of mullite refractory bricks for you according to the working conditions of high-temperature industrial furnaces.
1. Low creep mullite brick. Synthetic mullite clinker and super-high alumina bauxite clinker are used as raw materials. In addition, some high-purity quartz and additives can be added to produce low-creep mullite bricks.
Forming is carried out on a 300t friction brick press. The bulk density of the green body should be controlled above 2.70g/cm3. The green body is dried at 50~110°C for 16 hours. After drying, the residual moisture of the green body should be less than 0.5%. The highest firing temperature of the product is 1600°C, and the heat preservation time is 16h. The physical index of the product is as follows: the apparent porosity is 19~21%, the bulk density is 2.55~2.60g/cm3, and the compressive strength is 69~116MPa. 1450℃, 50h creep rate 0.12%.
2. Low creep sintered mullite brick. Sintered mullite bricks can be made by using andalusite as aggregate, sillimanite as intermediate particles, and common finely ground powder of sillimanite powder, bauxite powder, industrial alumina powder, and clay powder as base material.
The firing temperature is 1490°C and the heat preservation time is 19 hours. The porosity of the product can reach 17.15%. The bulk density is 2.53g/cm3, the compressive strength at room temperature is 136.5MPa, and the softening temperature under load is 1627°C. 1450℃, 50h creep rate can reach 0.87%. If the firing temperature is 1450°C and the holding time is extended to 26 hours, the purpose of sintering can also be achieved. However, the physical performance index is lower than that of the product fired at 1490°C. For example, at 1450°C, the 50h creep rate is 0.98%.
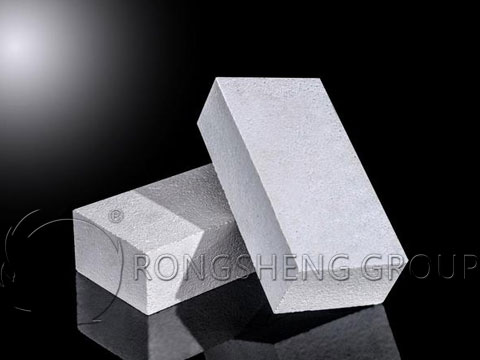
3. Sintered mullite bricks. The sintering temperature of sintered mullite bricks is usually above 1600°C. Such a high sintering temperature makes sintered mullite bricks difficult to mass-produce. Utilizing the activity of active SiO2, adding an appropriate amount of active SiO2 into the ingredients can make the sintered mullite bricks sintered at 1550 °C.
The physical indicators of this sintered mullite brick are as follows: the apparent porosity is 20.88%, and the bulk density is 2.61g/cm³. The compressive strength at room temperature is 84.4MPa. 1550℃, 50h high temperature creep rate 0.796%.
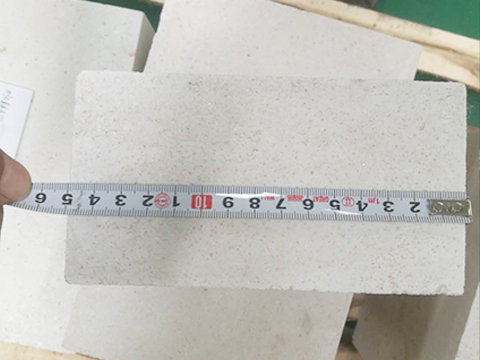
4. Mullite corundum brick. Using mullite and fused white corundum as raw materials and Suzhou soil as a binder, mullite corundum bricks for electric furnace roofs can be manufactured.
The green body is formed by a 300t friction brick press, and the density of the green body is 2.70g/cm3. The body is dried in a tunnel dryer. The inlet temperature is 40~50°C, the maximum drying temperature is 130°C, the drying time is 48h, and the moisture content of the green body is not more than 1.5%. The products are fired in a tunnel kiln at a firing temperature of 1550°C and a holding time of 10 hours.
The physical and chemical indicators of the product are as follows: Al₂O₃ 73.06%, SiO₂ 24.10%, apparent porosity 19.9%. The bulk density is 2.55g/cm3, and the compressive strength at room temperature is 81.7MPa. 1550℃, 3h re-burning line change rate -0.11%. The load softening start temperature is 1710°C.
5. Mullite-sillimanite bricks. Using andalusite as aggregate, sillimanite, high alumina bauxite, bonded clay as fine powder, and sulfurous acid pulp waste liquid as binder, mullite-sillimanite ceramic kiln furniture can be manufactured.
The physical and chemical indicators of the product are as follows: Al₂O₃ 51.9%, SiO₂ 43.9%, apparent porosity 23%. The bulk density is 2.27g/cm³, the compressive strength is 38.2MPa, and the softening temperature under load is 1520°C. Thermal shock stability (1100°C, water cooling)>20 times.
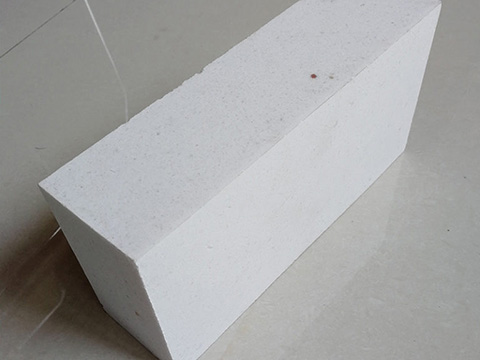
6. Sillimanite bricks. Using mullite, high alumina clinker, and sillimanite clinker as aggregates, sillimanite bricks can be manufactured.
The sillimanite bricks are formed by a friction brick press of more than 300t, and the density of the green body is controlled above 2.53g/cm³. The firing temperature of the sillimanite brick is 1350~1400°C, and the heat preservation is 8~10h.
The main physical and chemical indicators of sillimanite bricks are as follows: Al₂O₃ 61.45%, SiO₂ 35.15%. The apparent porosity is 15.3%, the bulk density is 2.58g/cm³, and the compressive strength at room temperature is 123.4MPa. 1500°C, 2h reburning line change +0.17%, 1450°C, 50h creep rate 0.72%, thermal shock resistance (1100°C~water cooling) greater than 15 times.
Rongsheng Mullite Refractory Brick for Sale
Rongsheng Refractory Material Manufacturer is a powerful refractory manufacturer and seller. Our refractory products have been sold to more than 100 countries and regions all over the world. Moreover, our technical team has been working on the design of refractory materials for the insulation layer of high-temperature industrial furnaces. It aims to save production costs for enterprises, including refractory material costs, refractory material transportation costs, fuel costs, etc. Our insulation material products include various lightweight insulation brick products, as well as mullite insulation bricks, as well as our new ultra-light nano-insulation bricks, nano-insulation modules, etc. Contact us for free refractory solutions and quotes.