The waste heat boiler is a boiler equipment that uses waste heat from the production process to generate heat energy from waste gas, waste materials, or waste liquids in various industrial processes. Waste heat boilers need to use various shaped and unshaped refractory materials as high-temperature furnace linings to operate. So, what refractory castables can be used in waste heat boilers? Since boilers are made by different manufacturers and models, the required castable specifications are also different. Rongsheng Refractory Material Manufacturer has rich production and sales experience in refractory furnace lining materials. Our refractory products are of reliable quality. Customer service is guaranteed.
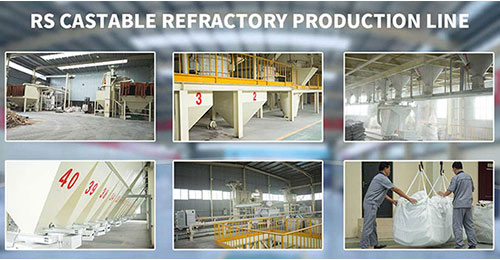
Rongsheng refractory castable factory is located in Xinmi, Henan. The castables produced by Rongsheng include steel fiber castables, lightweight castables, iron trench castables, high aluminum castables, lightweight insulation castables, wear-resistant castables, refractory ramming materials, refractory plastics, and Refractory Precast Shapes et al.
Configuration of Refractory Castables for CFB Boiler Lining
Circulating fluidized bed boilers are widely used and relatively one of the most environmentally friendly waste heat boilers. Circulating fluidized bed boilers are mainly used in the power industry, petrochemical industry, waste incineration industry, etc.
Although the application industries are different, the structure of circulating fluidized bed boilers is roughly the same. During boiler operation, high-temperature gas and solid particles in the gas cause serious wear and tear to the refractory linings in various parts of the furnace and circulation system. Therefore, the anti-wear and thermal insulation requirements of the linings used in various parts are the key to boiler operation. Taking a power plant boiler as an example, the operating environment of each part of the boiler and the requirements for the refractory castable lining are as follows.
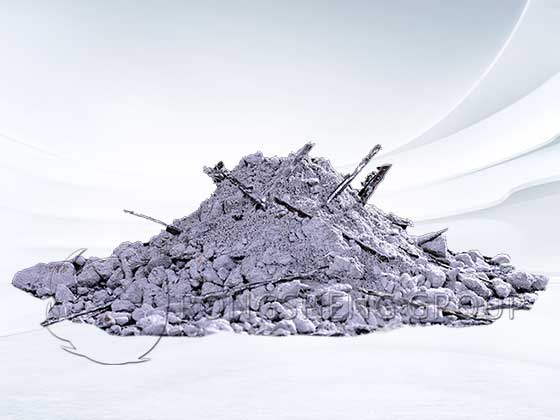
- The lower part of the furnace.
The dense phase area in the lower part of the furnace is the most severely worn part of the circulating fluidized bed boiler. The bed material is coarse, the concentration is high, the fluidization speed is fast, and the combustion atmosphere is corrosive to a certain extent. The wear-resistant and refractory castable used in this part requires anti-wear, good thermal conductivity, and good resistance to thermal burst and thermal shock. It is recommended to use steel fiber wear-resistant and refractory castables.
- Separator inlet flue.
The direction of the air flow changes in the separator inlet flue, and the ash particles in the air flow are fine and high in concentration. The air flow speed is generally 4.5~6.0m/s, and the temperature is 850~950℃. The combustion atmosphere is an oxidizing atmosphere, and wear and erosion are serious. The castable is required to have good wear resistance, heat burst resistance and thermal shock resistance. It is recommended to use steel fiber wear-resistant and refractory castables.
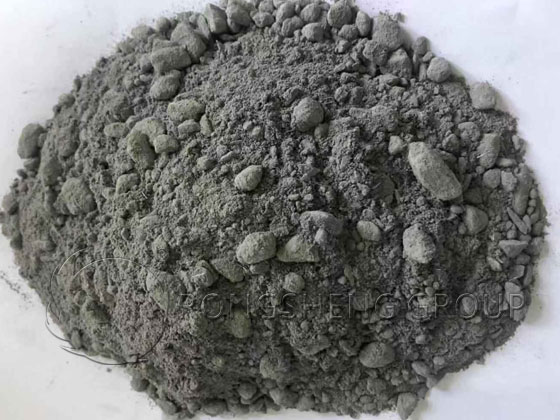
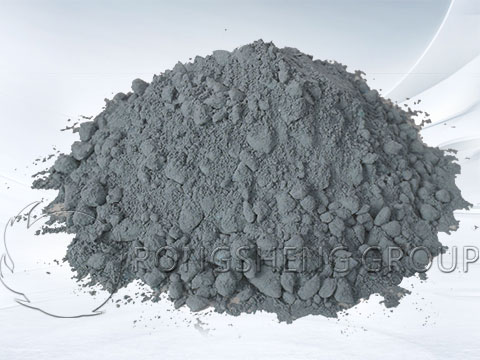
- Cyclone separator.
The air flow speed in the cyclone separator is high. Due to the centrifugal force, the coarse particles in the air flow hit the wall and are separated. And serious wear occurs on the separator inlet and the inner wall of the cylinder. The operating temperature inside the separator is less than 1000°C, and the refractory and wear-resistant layer is thick. Its atmosphere is an oxidizing atmosphere. The castables are required to be light, dense, wear-resistant, have good thermal insulation properties (for adiabatic separators), and have good thermal burst resistance and thermal shock resistance. It is recommended to use high-strength wear-resistant refractory castables or wear-resistant refractory plastics.
- Return device.
The return feeder sends the ash separated by the separator into the furnace for circulation and combustion. The returner has a fluidized bed on one side of the furnace and a moving bed on the other side. It is a fluidized sealed ash feeding device. The fluidization speed is less than 1m/s, the bed material is fine, the concentration is high, and the working temperature is about 900°C. Compared with other parts, the working environment of the return feeder is not too bad, but the construction of this part is difficult. No combustion occurs in the return device, which requires the castable to have good thermal insulation properties, thermal burst resistance and thermal shock resistance. It is recommended to use high-strength, wear-resistant and refractory castables.
- Screen type heating surface.
The power plant boiler furnace is equipped with a screen heating surface (water cooling screen, superheating screen). The lower elbow part of the screen is worn away by dust particles. The castable is required to have good wear resistance and thermal conductivity. It is recommended to use high-strength, wear-resistant and refractory castables.
Familiar with the working environment of the refractory lining of each part, the rational allocation of refractory castables and refractory plastics is the key to the long-term safe operation of the boiler. The wear resistance of refractory materials used in CFB boilers is the most important. The above recommendations for refractory castable materials are widely used and have achieved good results in CFB boilers of thermal power plants.
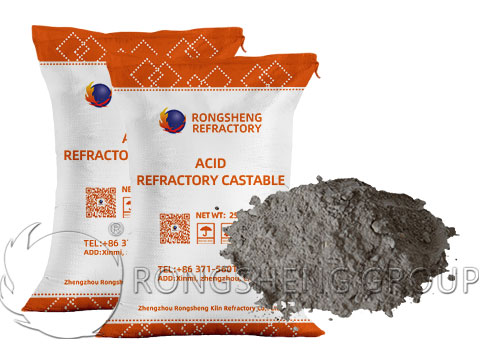
Acid-resistant castables for waste heat boilers
Acid-resistant castable is a refractory material specially used in waste heat boilers. It has excellent acid resistance and high-temperature performance, which can protect the high temperature parts of the waste heat boiler and extend the service life of the equipment. The high-temperature parts of the waste heat boiler will be affected by high-temperature corrosion and acid attack, so acid-resistant castables need to be used to protect these parts.
Acid-resistant castable is a refractory material composed of refractory aggregate, refractory powder, binder and admixture. It has excellent acid resistance and high temperature performance, can resist erosion by acidic substances and high-temperature oxidation, while maintaining high strength and stability. In waste heat boilers, acid-resistant castables can be applied to high-temperature parts to form a protective layer to protect equipment from corrosion and damage.
Acid-resistant castables are widely used in waste heat boilers. They can be used to protect the furnace, flue, economizer, air preheater and other parts of the boiler. Due to the high operating temperature and pressure of waste heat boilers, acid-resistant castables are required to have high high temperature resistance and compressive strength, as well as good adhesion and fluidity, and can be easily constructed and repaired.
In order to ensure the safe operation and service life of waste heat boilers, it is very important to choose suitable acid-resistant castables. When selecting acid-resistant castables, factors such as the operating conditions of the equipment, the performance of the refractory materials, and construction requirements need to be considered. At the same time, refractory materials need to be inspected and maintained regularly during use, and problems can be discovered and dealt with in a timely manner to ensure the safe and stable operation of the equipment.
To purchase high-quality refractory castables for waste heat boilers, please choose Rongsheng Refractory Materials Manufacturer. The quality of our refractory products is guaranteed, and the refractory castable formula can be customized according to actual working conditions. High-quality, long-life refractory castable furnace lining material. Contact us to get free samples and quotes.