The main structural strength of corundum-silicon carbide castables depends on the bonding strength of the matrix. Because the castable with corundum-silicon carbide as the aggregate is difficult to sinter and combine the aggregate particles, therefore, it must be combined by the aggregate phase formed by the matrix. According to the above experimental results, as the ratio of synthetic mullite powder (SM) to mixed powder (MP) in the matrix decreases, that is, as the ratio of mixed powder increases, the physical properties are significantly improved. The mixed powder here is a powder composed of alumina micro-powder and silica micro-powder according to the Al2O3/SiO2 ratio of 2.33. This kind of powder can generate mullite “in place” when it is heated in the castable, which can be called secondary here. Raw (secondary) mullite. Secondary mullite contributes more to castable strength than primary (synthetic) mullite. This is because the secondary mullite is easier to form a network structure in the matrix than the primary mullite, which is more conducive to improving the structural strength, especially the high-temperature thermal strength.
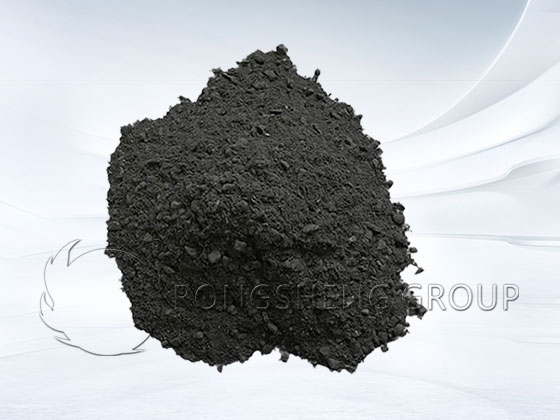
Microstructure Characteristics of Corundum-Silicon Carbide Ramming Mass
The columnar mullite in the castable matrix is connected into a network structure one by one, and the inner crystals of the mullite are filled by the glass phase. The corundum aggregate particles react with SiO2 in the matrix to form a new secondary mullite reaction zone around the corundum particles. The edges of silicon carbide particles are clear and tidy, but there is a Si-rich shell layer around the particles, and the uneven Si-rich layer reacts with the glass in the matrix to form a whole.
Secondary mullitization is a reaction between SiO2 in the glass phase and corundum during sintering. There are mainly two forms. One is present around corundum particles. This secondary mullite exists at the junction of the particles and the matrix, forming a secondary mullite reaction zone around the particles, combining the corundum particles with the matrix. The second is the reaction between corundum micro-powder in the matrix and SiO2 in the glass phase to generate secondary mullite to form a network structure in the matrix. Improves the high-temperature performance of the matrix, thereby enhancing the overall performance of the castable. Therefore, as the speed of corundum micro-powder and SiO2 micro-powder in the castable matrix increases, the secondary mullite generated in the system increases, and various properties are improved.
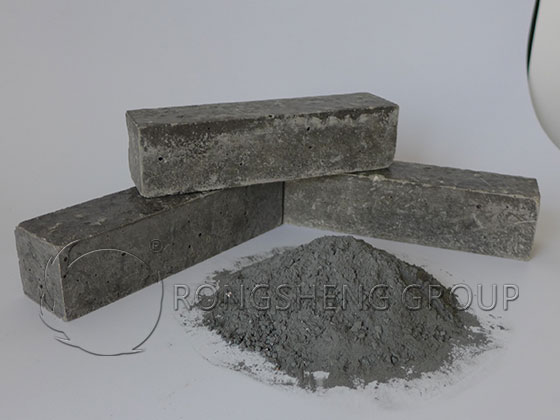
Properties of Corundum-Silicon Carbide Ramming Mass
A corundum-silicon carbide castable matrix composed of pre-synthesized mullite powder and a mixed powder with a ratio of (Al2O3/SiO2) of 2.33. Its physical properties and high-temperature mechanical properties are improved with the increase in the amount of secondary mullite in the matrix. It shows that the contribution of secondary mullite to the improvement of the performance of corundum-silicon carbide castable is greater than that of primary mullite.
Application of Silicon Carbide-Corundum Composite Refractory Ramming Material in Pulverized Coal Gasifier
Silicon carbide-corundum composite refractory ramming material is mainly used in the water wall area. Using the high thermal conductivity of silicon carbide-corundum composite refractory ramming material, the heat of the slag on its surface is quickly taken away. This lowers the temperature of the slag and solidifies it. Gradually form a stable solid slag layer, realizing “resisting slag with slag”. Effectively protect the refractory material from the erosion of high-temperature liquid slag.
Silicon carbide-corundum composite refractory ramming material is a SiC-Al2O3 system. The raw materials are silicon carbide, corundum, activated alumina micro-powder, additives, binders, etc. The composition ratio of conventional silicon carbide-corundum composite refractory ramming materials is 65%-75% of silicon carbide, 20%-30% of alumina, and the binder is added in the form of liquid. It is applied to the surface of the water-cooled coil by ramming.
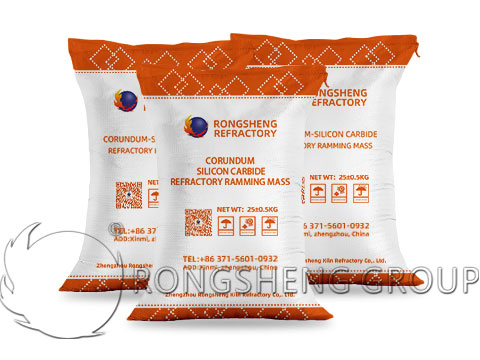
Silicon Carbide Ramming Material for Mineral Wool Electric Furnace
The primary problem of the electric furnace smelting mineral wool method is the excessive consumption of refractory materials in the lining of the electric furnace. The furnace lining refractory material is subject to cyclical erosion and damage of the slag in the high-temperature liquid state, and its service life is short. The process of electric furnace slag smelting is actually the reaction process of mineral wool acid adjustment. The main components of slag are not only acidic medium and alkaline medium but also some low-melting substances. Therefore, the damage and erosion of conventional refractory materials are very fast. In the selection of refractory lining materials, dense refractory materials that are resistant to erosion and penetration should be selected, and the materials have low porosity and high density. However, the price of this refractory material is very high. For example, chrome-zirconium corundum bricks and zirconium corundum bricks can be applied to this type of furnace. Since the market price is between 20,000 and 30,000 yuan/ton, it will increase the cost for users. The commonly used high alumina brick and silicon carbide ramming material lining, although the service life is not very ideal, the price is several times cheaper than corundum refractory materials. Therefore, at present, there are more units of furnace linings made of high alumina bricks and silicon carbide ramming materials.
Rongsheng Silicon Carbide Ramming Material Manufacturer
The silicon carbide ramming mass produced by Rongsheng refractory manufacturer is carefully formulated with silicon carbide (SiC content ≥ 98.5%), aluminum dihydrogen phosphate as a binder, and other materials. Its main features are: high strength, strong resistance to liquid slag erosion, and can protect the inner lining. The material has good thermal conductivity, a small thermal expansion coefficient, strong oxidation resistance, and thermal shock stability. It is mainly used in submerged arc furnaces, industrial kilns, inner walls of cyclones, and waste incinerators. Rongsheng refractory manufacturers can adjust the ratio of refractory materials according to the design indicators specified by customers and the actual working conditions of the road, so as to meet the performance indicators. Contact us for free samples and quotes.