The Refractory Precast Shapes is to shape the unshaped refractory material. The preparation process is between the shaped refractory material and the unshaped refractory material. Refractory Precast Shapes are an advancement in the application and application of monolithic refractory materials. From the application of Refractory Precast Shapes in a cement kiln, you can learn more about the advantages of Refractory Precast Shapes. The new factory of Rongsheng refractory material manufacturer mainly builds the brand of uncertain Refractory Precast Shapes. To better serve the lining of high-temperature industrial furnaces.
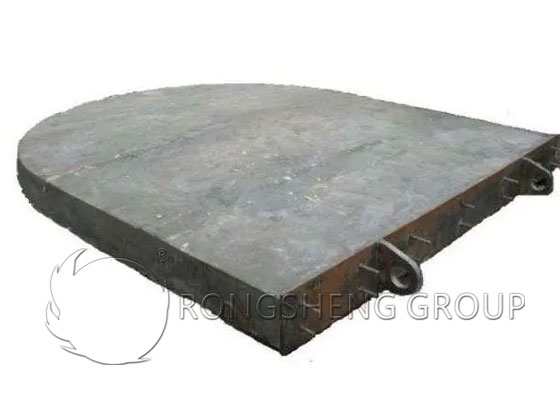
Application of Refractory Precast Shapes in Cement Kiln
Monolithic refractory materials have the advantages of excellent performance, convenient construction, and energy saving. It has been widely used in the cement industry.
The raw materials and ratio of Refractory Precast Shapes for cement kiln can refer to the castable of the used part. The shape adopts a personalized design according to the on-site use conditions and adopts factory and large-scale production in terms of molding and baking. Need to pay more attention to performance indicators after baking. Compared with castables, Refractory Precast Shapes have lower requirements on shelf life and environmental conditions, and have better overall stability and adaptability. It can significantly shorten the construction time of cement kiln, improve maintenance efficiency, and effectively prolong the service life of refractory materials. Good results have been achieved in the grate cooler, tertiary air duct, kiln tail smoke chamber, and other parts. It is expected that the use of Refractory Precast Shapes in cement kilns will be further expanded in the future.
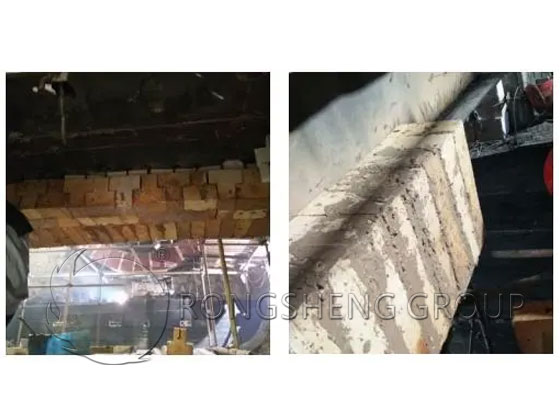
Application Advantages of Refractory Precast Shapes in Cement Kiln
Refractory prefabrication is to divide the pre-construction part into small pieces in advance, design a suitable shape, and then make a mold according to the shape. After pouring, curing, and baking in the factory, it is transported to the site for construction and installation. The application of Refractory Precast Shapes has changed the construction method of traditional pouring materials on-site, making the construction simple and easy. It can save on-site mixing, pouring, or ramming and the corresponding equipment required, which greatly saves construction time. And the on-site construction conditions are not affected by the construction environment and seasons, which is more conducive to ensuring the construction quality. In order to facilitate production, transportation, and installation, the shape of the prefabricated parts should not be designed to be too large or too complicated, and the size should be as uniform as possible. In addition, it is necessary to consider the combination of blocks and blocks, so as to enhance the integration effect after construction. The construction site needs to be cleaned up, otherwise, it will affect the installation accuracy and effect of the Refractory Precast Shapes.
Most of the parts used for refractory Precast Shapes are in special parts under harsh environments such as high temperature, cement clinker erosion, wear, rapid cooling, and rapid heating, and are prone to mechanical deformation. It needs to have good corrosion resistance, good wear resistance high-temperature gas erosion resistance, and excellent thermal shock resistance. To meet the performance requirements, the ratio of raw materials is the basis, which is similar to the requirements of castables. However, castables need to pay attention to the performance in the entire temperature range from construction to service conditions. The Refractory Precast Shapes is a shaped product prepared by using castables, and it is only necessary to pay attention to the performance after baking. Many manufacturers have listed the performance indicators of prefabricated parts under different temperature conditions, which is actually of little reference value to cement manufacturers. In view of this situation, the raw materials and proportions used for Refractory Precast Shapes can be adjusted on the basis of castables, and more attention needs to be paid to the performance after baking.
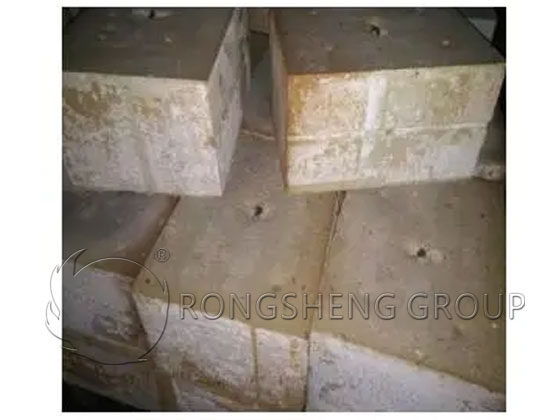
Refractory materials in key parts of cement kilns require high construction quality during construction. During the inspection and maintenance of cement kilns, the general construction period is short, and the construction quality of on-site pouring is difficult to guarantee. The quality of construction has a great impact on the service life of refractory materials. The increase in the amount of water added will increase the porosity of the castable, reduce its strength, and seriously affect the wear resistance of the castable. After the construction of the castable, there must be a certain curing time. After the curing is completed, it must be baked, otherwise, it is easy to burst.
Since the production process of Refractory Precast Shapes is carried out in the production enterprise, it can overcome the adverse effects of factors such as tight construction time on site, environmental seasonal temperature changes, and on-site construction management. After sufficient maintenance and strict baking, the construction quality can be guaranteed, the quality problems caused by irregular construction can be greatly reduced, and the performance of refractory materials can be fully exerted. It can be ignited and used directly after installation, which shortens the maintenance time and can create good economic benefits.
Rongsheng Monolithic Refractory Material Manufacturer
Rongsheng refractory manufacturer has an environmentally friendly and advanced monolithic refractory production line. At the same time, we have established a Refractory Precast Shapes factory to provide high-quality refractory lining materials for various high-temperature industrial furnaces. To purchase high-quality indeterminate refractories or Refractory Precast Shapes, please contact us. We will provide you with free refractory design, and we can also customize Refractory Precast Shapes for you according to your specific working conditions.