Medium frequency centerless induction copper melting furnace – 30 tons copper melting furnace. Due to the substantial increase in the size of the furnace, new requirements have been put forward for the technology and performance of the furnace lining refractory materials. Rongsheng Refractory Material Manufacturer, 30 tons medium frequency centerless induction copper melting furnace refractory materials, suitable for lining materials used in large tonnage copper smelting furnaces. Contact Rongsheng for free samples and quotes.
Damage Mechanism of Refractory Materials in Copper Smelting Furnace Lining
The damage of refractory materials in copper smelting furnace lining is mainly caused by the penetration of molten metal, metal oxides, slag and the effect of temperature stress. The lining of the centerless induction furnace is thin, so there is a large temperature gradient in the lining, which can easily lead to cracking and peeling of the lining. When molten metal, oxides or slag penetrate into the depth along the cracks or pores of the lining, the following three situations occur:
- 1) The molten metal is oxidized, reduced, or generates low-melting-point substances, causing the lining to be eroded or cracked or peeled off.
- 2) The molten metal and refractory materials undergo an oxidation reaction, accompanied by volume expansion, causing the lining to expand and collapse.
- 3) The molten metal or slag with strong alkalinity has good fluidity and erodes the lining more seriously.
Red copper is one of the most permeable copper alloys, and its melting point is 1083℃. During smelting, molten copper penetrates into the lining, oxidizes and expands in volume. When copper is oxidized to Cu2O, the volume increases by 0.64 times, and when it is oxidized to CuO, the volume increases by 0.75 times. Due to the oxidation of copper, the volume of the furnace lining material changes, causing the organizational structure of the lining material to crack and even peel off.
In addition, under certain temperature conditions, copper oxide can react with certain oxides in the refractory lining to form a liquid phase. For example, the liquidus point of copper oxide with SiO2 is 1060℃, the liquidus point with MgO is 1135℃, and the liquidus point with Al2O3 is 840℃. Due to the generation of low-melting-point substances, the organizational structure of the lining material is destroyed, and corrosion occurs, which reduces the service life of the material. Since the temperature of the metal copper liquid in the furnace is as high as 1250℃ or above, the viscosity is similar to that of water. Therefore, its fluidity and permeability are very strong, and it is very easy to penetrate into the lining. After repeated changes in volume due to cold and hot temperatures, the lining will crack, especially when the temperature suddenly changes, which can easily cause the lining to collapse.
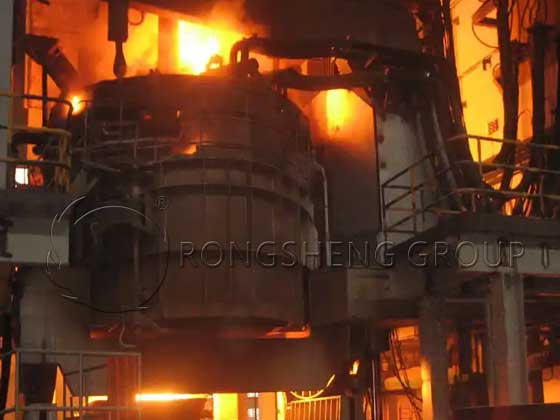
Characteristics of Refractory Materials for Medium Frequency Centerless Induction Copper Melting Furnace
Refractory materials for medium frequency or power frequency centerless induction copper melting furnaces should have the following characteristics:
- 1) It should have excellent physical and chemical stability and not easily react chemically with molten metal.
- 2) It does not stick to slag (or less stick to slag), which is easy to clean and keeps the integrity of the furnace lining.
- 3) It has very high strength. Because the centerless furnace generates a strong stirring force when smelting metal, the molten liquid has a strong scouring effect on the furnace lining. Therefore, only dense and high-strength materials can withstand scouring and operate safely for a long time.
- 4) It has good thermal shock stability to meet the cold and hot changes caused by the continuous pouring of molten liquid from the furnace body.
At present, large-tonnage centerless furnaces generally use neutral oxides as furnace linings. Although quartz sand is cheap and abundant in resources, it is easy to stick to copper slag, has poor thermal stability, and has poor safety and reliability. Rongsheng copper smelting furnace refractory manufacturer, cheap price, reliable quality.
Copper Melting Furnace Lining Refractory Materials
The main material of the refractory lining material for copper smelting furnaces is the main body of the refractory lining material products and the characteristic basis of the formula material. At present, large-tonnage centerless induction furnaces generally use neutral oxides as linings. In China, the refractory materials used in copper smelting furnaces are divided into two categories: one is acidic quartz sand materials, and the other is neutral materials with alumina as the main component. Refractory manufacturers have found through experiments that lining materials with neutral oxides as the main component are the most suitable materials for large-tonnage copper melting furnaces.
Comparison of the use of quartz sand materials and neutral alumina furnace lining refractory materials
1) Quartz sand furnace lining materials
Quartz sand furnace lining materials. When smelting copper and copper alloys (especially copper alloys containing metals such as Al, Ni, Mn, and Fe), since SiO2 is an acidic oxide, and Cu2O, NiO, and MnO2 are all alkaline oxides, the following reactions will occur during the smelting process:
SiO2 + Cu2O →SiO2 ·Cu2O
NixO2 + SiO2 →NixO2 ·SiO2
MnO2 + SiO2 →MnO2 ·SiO2
The above reactions will make the composition of the copper alloy difficult to control, thereby affecting the quality of the casting. The impact on large-tonnage coreless furnaces with high power is particularly obvious. At the same time, the products generated by the reaction will adhere to the surface of the furnace lining, making the furnace size smaller and smaller, and the melting rate is greatly reduced. Take a factory’s 1.5t copper melting furnace as an example. Quartz sand is used as the furnace lining. After more than ten furnaces are used each time, serious slag sticking will occur, the furnace size will be reduced by 10~20%, and the melting time will be extended by more than 1 hour.
2) Neutral alumina furnace lining material
When using dry-molded neutral alumina furnace lining material, since the main component is neutral oxide and special anti-seepage agent is added, it does not react with Mn, Ni, Al, etc. in the copper liquid. It is also particularly resistant to copper corrosion, so there is no slag sticking.
This material has a good effect on a 16-ton industrial frequency copper melting furnace in a copper material factory, and the furnace lining life exceeds three years (more than 700 furnaces). Moreover, the furnace lining size does not change by more than 5% from beginning to end, thus ensuring the normal use of the furnace with high efficiency from beginning to end.
30-ton Coreless Medium Frequency Copper Melting Furnace Lining Material
Although dry-molded neutral alumina lining materials work well on small and medium-sized copper melting furnaces. However, for 30-ton medium frequency furnaces, due to the large changes in depth and diameter, the static pressure and thermal stress that the lining has to bear during use have greatly increased. This puts higher requirements on the performance of the lining material.
According to the structural characteristics and operating conditions of large-tonnage furnaces, refractory manufacturers focus on the thermal stability, high-temperature mechanical strength and corrosion resistance of new materials.
1) Improvement of thermal stability
The thermal stability of refractory materials is related to the thermal expansion performance, thermal conductivity and particle size composition of the material. Suitable additives can increase the high-temperature mullite phase in the material to more than 85%. So that the material has a lower thermal expansion coefficient. In order to appropriately improve the thermal conductivity, Rongsheng manufacturers increased the content of high thermal conductivity materials.
The particle composition and maximum particle size both affect the thermal stability of the material. Combined with the thickness of the furnace lining, Rongsheng controls the maximum particle size at 8~10mm and the proportion of aggregate at 55~65%.
2) Improve the strength and corrosion resistance of materials
For centerless induction melting furnaces, the higher the strength of the furnace lining material, the better. In the case of being able to resist the erosion of molten metal, more attention should be paid to improving the toughness of the material. For this reason, a composite binder is used. The use of the composite binder greatly improves the properties of the sintered layer, semi-sintered layer and loose layer of the furnace lining. A small amount of high-viscosity glass phase in the sintered layer blocks the infiltration of molten metal. The content of components that are not wetted by copper liquid and do not react with copper liquid is increased in the powder, further improving the corrosion resistance. The content of components that produce bonding strength below 800℃ is reduced in the composite binder, ensuring that the loose layer of the furnace lining exists from beginning to end. This effectively prevents the extension of the furnace lining cracks and the penetration depth of the molten metal.
Industrial operation effect of furnace lining materials
30-ton medium-frequency copper melting furnace. The melting alloy is nickel-aluminum bronze, and the maximum melting temperature is 1350℃. The furnace operation mode is: feeding – melting – casting – furnace stop – waiting for sand mold making. The lining material has been used for two years and the lining is in good condition. During the use of the lining, there is no sticky slag, less cracking, and no reaction with copper alloy.
Economic Benefits of High-Performance Lining Materials
Under the condition of achieving the same service life, the cost ratio of quartz and neutral alumina is: (5.8~7.4): 1. And the total cost of quartz lining refractory materials accounts for more than 30% of the total cost of the furnace. The total cost of neutral alumina lining refractory materials accounts for about 6% of the total cost of the furnace.
Rongsheng refractory manufacturer’s 30-ton medium-frequency coreless induction copper melting furnace lining refractory materials. Dry-molded neutral alumina lining refractory materials have high hot surface strength, corrosion resistance, wear resistance, and excellent resistance to rapid cooling and heating. It provides a reliable lining guarantee for large-tonnage coreless copper melting furnaces. To purchase high-quality refractory bricks, amorphous refractory materials, etc. for copper melting furnaces, please contact Rongsheng manufacturers.