Carbon ramming materials are bulk materials made of silicon carbide, graphite, and electric calcined anthracite as raw materials, mixed with a variety of ultrafine powder additives, and electrofused cement or composite resin as binding agents. It is used to fill the gap between the furnace cooling equipment and the masonry or the filling material for the masonry leveling layer. Ramming materials have good chemical stability, are resistant to erosion, abrasion, spalling, and thermal shock. They are widely used in metallurgy, building materials, non-ferrous metal smelting, chemical industry, machinery and other manufacturing industries! Acidic, neutral and alkaline ramming materials are widely used in coreless intermediate frequency furnaces and cored induction furnaces. As intermediate frequency furnace ramming materials, they are used to melt gray cast iron, ductile iron, forgeable cast iron, vermicular graphite cast iron and cast iron alloys. , melt carbon steel, alloy steel, high manganese steel, tool steel, heat-resistant steel, stainless steel, melt aluminum and its alloys, melt copper alloys such as copper, brass, white copper and bronze, etc.
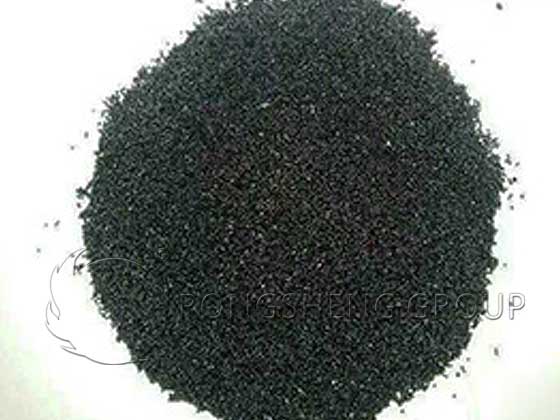
Application of Carbon Ramming Materials in Blast Furnaces
Carbon ramming materials are widely used in blast furnaces. Rongsheng Refractory Materials Manufacturer is a powerful manufacturer and seller of refractory materials, providing high-quality and long-life refractory lining materials for high-temperature industrial furnaces. Carbon ramming material is used in the gap between the carbon bricks in the blast furnace bottom and the furnace bottom sealing plate and in the leveling layer above the center line of the furnace bottom water-cooling tube. It is required that the carbon ramming material after arrival has a certain strength and density, filling every corner and small gaps, so as to achieve the requirement of no leakage of molten iron. Moreover, the thermal conductivity of the carbon ramming material must be consistent with the performance of the high thermal conductivity carbon bricks, so as not to affect the life of the blast furnace and ensure the normal production needs of the blast furnace.
Application Characteristics of Carbon Ramming Materials
Carbon ramming mass material plays an important role in transferring heat. Blast furnace cooling requires the heat of the carbon bricks to be transferred out of the blast furnace carbon ramming material and taken away by the cooling water to slow down the erosion rate. If the thermal conductivity of the carbon ramming mass material is too low and inconsistent with the performance of the furnace bottom carbon bricks, it will affect the smooth transfer of heat. This causes the temperature of the carbon brick to rise and accelerates the erosion rate of the carbon brick.
In addition, carbon ramming mass material also plays the role of refractory brick lining. Carbon ramming material is made of the same material as carbon bricks. In the later stages of the blast furnace, if the carbon bricks burn through or leak molten iron and slag, the carbon ramming mass material can act as a refractory brick lining to protect the furnace bottom and maintain normal production.
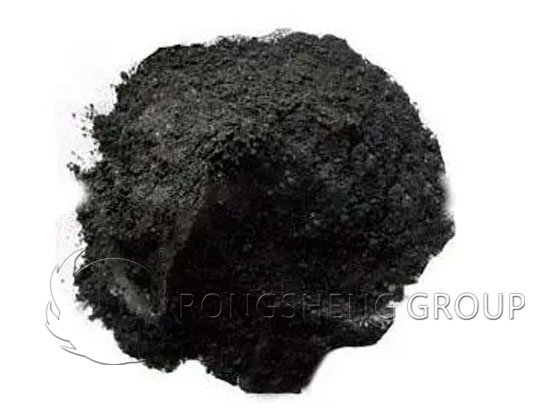
Application of Carbon Ramming Mass Materials in Blast Furnace Bottom
The blast furnace bottom is subjected to high temperature, high pressure, slag, and iron erosion and penetration, and the working conditions are very harsh. Therefore, carbonaceous materials with excellent performance must be used. Graphite materials have extremely high thermal conductivity, high-temperature resistance, lubricity, plasticity, slag resistance and chemical and thermal stability. Therefore, carbon ramming mass material is used in the leveling layer between the blast furnace bottom carbon bricks and the furnace bottom sealing plate and above the center line of the furnace bottom water-cooling pipe.
Construction of Carbon Ramming Mass Material
The construction of carbon ramming mass materials is mainly based on ramming method, but the construction methods will be different in different use parts and construction body structures. The construction of carbon ramming mass material at the bottom of the blast furnace must wait until the control flat steel is installed and inspected before the ramming construction can begin. In order to prevent damage to the leveling flat steel strips, the ramming material must be evenly spread in the leveling flat steel strips during construction, use a flat vibrating tamper, and continuously ram back and forth along the space between the steel strips until it is dense. The pounded surface must be shaved first, and then a layer of material is added to continue pounding. The thickness of each layer is 100mm. After 2-3 times of feeding, adjust the size according to the design drawing, and continue to pound it tightly. The carbon ramming mass material after final ramming must be higher than the top surface of the flat steel, and finally leveled one by one with a scraper along the top surface of the steel strip. Use a spirit level to check whether it is on a horizontal plane. Only after the test reaches the standard can the next step of carbon brick laying be carried out.
Precautions for Construction of Blast Furnace Carbon Ramming Mass Materials
- Construction should be carried out strictly in accordance with the construction instructions of the carbon ramming mass material.
- During construction, the edges such as the four corners should be pounded tightly to avoid deterioration in thermal conductivity and erosion.