In order to solve the problem of slow hardening time of low-cement self-flowing castables in low-temperature environments such as winter, the effects of different types of accelerators on the setting time of low-cement self-flowing castables were studied.
With the development of amorphous refractory castables, the proportion of castables used in heating furnace linings is increasing, among which low-cement self-flowing castables are being used more and more widely and their proportion is also increasing. Low-cement self-flowing castables are developed for heating furnaces by reasonably selecting raw materials and particle size grading, and introducing ultrafine powder and high-efficiency dispersants. The self-flowing castable has the characteristics of convenient construction, self-flowing and densification, good volume stability, and good thermal shock stability. It is suitable for use in parts with complex shapes and narrow spaces.
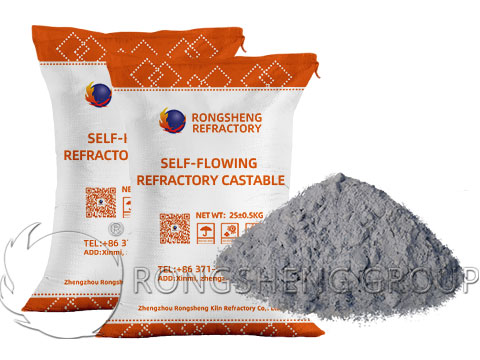
Effect of Coagulant on the Setting Time of Low-Cement Self-Flowing Castable
In the field application of low-cement self-flowing castable, the rheological properties, especially the hardening time, need to be controlled. When the temperature in winter is lower than 5℃, the hydration reaction is slower than that at normal temperature, and the hardening time of the castable is slow, which will greatly extend the demoulding time and affect the subsequent performance of the castable and the construction progress. In order to solve the problem of slow hardening time of low-cement self-flowing castable in low temperature environment such as winter. Effect of coagulant type on the setting time of low-cement self-flowing castable:
- (1) The addition of coagulant has little effect on the room temperature performance of low-cement self-flowing castable, among which the cold strength will be slightly improved.
- (2) The addition of coagulant will significantly reduce the setting time of low-cement self-flowing castable. Among them, the setting time of adding Li OH is the shortest, the addition of NaOH is moderate, and the second is sodium aluminate.
- (3) Although the addition of coagulant will slightly reduce the load softening temperature of the sample, it is within the use range of the heating furnace and does not affect normal use.
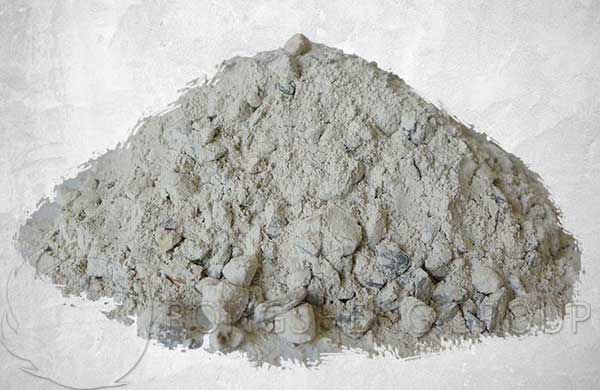
Application of Self-Flowing Castables for Blast Furnace Main Trench
In order to solve the problems of non-compactness and segregation of materials caused by vibration and other construction reasons during the daily pouring construction of the blast furnace main trench. Low-carbon fused brown corundum, dense corundum and silicon carbide are used as aggregates, and silicon carbide, white corundum, activated alumina powder and SiO2 powder are used as fine powders. A self-flowing castable for the blast furnace main trench was developed by replacing the addition amount of Castabio T85 (0.08% (w) of the water reducer in the sample with 1% (w) of polycarboxylic acid water reducer and adding 6%, 8% and 10% of activated alumina powder (w).
Damage factors of refractory lining of blast furnace main ditch
The main ditch is the channel for blast furnace iron tapping, which plays a very important role in the smooth progress of blast furnace ironmaking. In recent years, the volume of domestic blast furnaces has continued to increase, the wind temperature and wind pressure have continued to increase, and the iron tapping cycle has become shorter and shorter, which has increased the load of the iron tapping ditch system and increased the degree of erosion and damage of the iron tapping castable.
The causes of damage to the main iron ditch can generally be divided into melting loss, wear, cracking and peeling. For the main iron ditch, there are many factors that affect the life, among which the most important factor is the construction quality. The construction quality of the main iron ditch is affected by the amount of water added on site, stirring time, vibration time, demoulding time, maintenance, baking, etc. With the increase of water volume, there are more pores in the castable after drying, the corrosion resistance is poor, and the service life is reduced.
Blast furnace iron tapping ditch usually uses vibrating castables, the construction environment is poor, the labor intensity is high, and the life of the castable is also affected by human construction factors. In order to improve the on-site construction technology and enhance the construction quality, a main ditch self-flowing castable was developed based on the existing formula.
Self-flowing castable for main ditch of blast furnace
The main aggregates are low-carbon brown corundum (8-5, 5-3 and 3-1 mm), dense corundum (≤1 mm), silicon carbide (≤1 mm). The fine powders are silicon carbide powder (≤0.074 mm), white corundum (≤0.074 mm), activated alumina powder (d50 = 1.5 μm) and SiO2 powder (d50 =0.5 μm). Pure calcium aluminate cement is used as a binder, and a composite antioxidant (Si powder and metal Al powder) is added. The water reducer is Castabio T85 and a similar domestic polycarboxylic acid water reducer.
After the main ditch self-flowing castable is mixed according to the formula, it is placed in a stirring pot and stirred for 3 minutes. First, the self-flow value of the freshly mixed material and the material after being placed for 30 min was measured by the jumping table method. Then, the samples were vibrated and formed into 40 mm × 40 mm × 160 mm specimens. The specimens were naturally cured for 24 h before demoulding and baked at 110 °C for 24 h. Then, they were heat treated at 1450 °C for 3 h. Finally, the room temperature compressive strength, room temperature flexural strength, linear change rate after burning, thermal shock resistance (1100 °C, water cooling) and high temperature flexural strength at 1400 °C for 1 h were tested according to relevant national standards.
Performance of main trench self-flowing castable
- 1) Compared with the material with domestic polycarboxylate water reducer, the material with Castabio T85 added has 0.6 percentage points less water (w) under the premise of ensuring the fluidity of the material, and the self-flow value is relatively higher, and the fluidity decay at 30 min is slower.
- 2) As the amount of activated alumina powder added (w) increases from 6% to 10%, the fluidity of the sample becomes better. This is because the appropriate amount of powder can fill the accumulation gap of particles and fine powder.
- 3) From the initial self-flow value and the 30 min self-flow value, the materials of 2#, 3#, and 6# samples can meet the requirements of self-flow.
It can be seen that with the increase in the amount of activated alumina powder added, the room temperature compressive strength, room temperature flexural strength, line change rate after burning, and high temperature flexural strength of the heat-treated samples gradually increase.
After 30 times of water-cooling thermal shock at 1100 °C, no peeling or falling off occurred on any of the samples.
Practical application of self-flowing castables in the main trench of blast furnace
Industrial tests were conducted in the main trench of blast furnace in a certain iron plant. The main trench material was used for self-leveling construction, and no vibration was performed during the entire construction process. In this industrial test, the iron flow rate reached 150,000 tons at a time, without any repairs in the middle, and the use effect was good. It can not only meet the requirements of iron flow rate, but also reduce the labor intensity of workers and ensure stable construction quality. It indirectly reduces the number of repairs of the main trench and increases the life of the main trench. It is suitable for the construction of the main trench of large and medium-sized blast furnaces.