The aluminum smelting process mainly produces alumina, then electrolyzes the alumina into metallic aluminum and performs smelting, dehydrogenation and purification, and finally casts it into aluminum ingots. There are many types of kilns used for aluminum smelting, and the furnaces have lower operating temperatures and better use conditions. Generally, clay bricks and high-alumina bricks are used as linings to meet production requirements and have a longer service life.
Refractory Materials for the Production of Alumina
Use bauxite as raw material to produce aluminum hydroxide. Then calcine it at a temperature of 950-1200℃ to obtain aluminum oxide. The thermal equipment for calcining aluminum hydroxide generally uses rotary kilns and flash roasters.
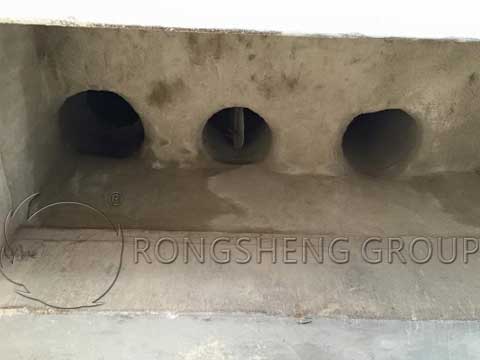
(1) Refractory materials for rotary kilns. The rotary kiln is divided into a preheating zone, a firing zone and a cooling zone. The working temperature of the firing zone is not higher than 1200℃. The insulation layer structure of the kiln is to first lay a layer of refractory fiber felt against the furnace shell. Then use diatomaceous earth bricks, clay insulation bricks or floating bead bricks for masonry, or use lightweight refractory castables with a volume density of 0.8g/cm³ for integral pouring. The working layer of the preheating zone is built with turned earth bricks. The working layer of the firing zone is built with high-alumina bricks, low-calcium aluminate cement combined with high-alumina unfired bricks or phosphoric acid combined with high-alumina unfired bricks. The working layer of the cooling zone is greatly worn by the burning materials. In addition to dense clay bricks, it is advisable to use unburned bricks with high aluminum phosphate. Rotary kiln refractory materials for alumina production, Rongsheng Refractory Manufacturer.
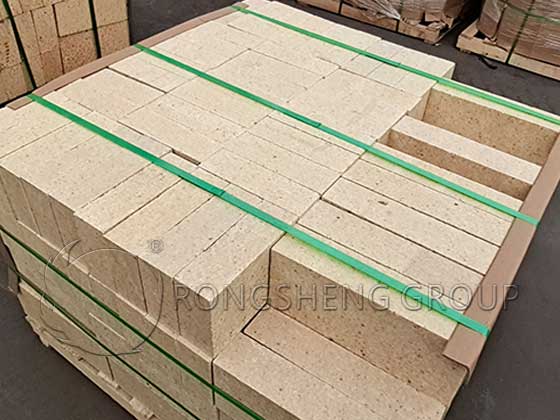
(2) Refractory materials for flash roasting furnace. The furnace group consists of a flash furnace, a preheating furnace, a retention tank, a fluidized bed dryer and a cooler. The maximum operating temperature is about 1100℃, and the maximum flow rate of the material in the furnace section is about 30m/s. The entire roasting process of the material in the furnace is carried out under high temperature, high speed and constantly changing flow direction, which causes wear on the furnace lining. The furnace lining is generally poured with high-strength aluminum silicate refractory castables. That is, first weld heat-resistant steel anchor nails or install ceramic anchors on the furnace shell, and then lay a layer of 20mm thick refractory fiber felt. Finally, pour 200-300mm thick refractory castables, which can be used after the furnace is baked.
(3) Refractory materials for alumina electrolytic cells
The electrolyte is composed of alumina and cryolite (Na₃A1F₆) flux, and the electrolyte solution is placed in the electrolytic cell and energized. At a temperature of 950-970°C, the alumina in it is decomposed into metallic aluminum and oxygen.
The thickness of the non-working layer of the aluminum electrolytic cell is generally 240-400mm. First, a layer of insulation board or refractory fiber felt is laid against the tank shell, and then clay insulation bricks or floating bead bricks are laid, or lightweight refractory castables with a volume density of 1.0g/cm³ can be poured. Finally, ordinary clay bricks are laid. The working layer is built with carbon or silicon nitride combined with silicon carbide refractory materials, which can resist the penetration of aluminum liquid, fluoride and electrolyte and molten sodium salt erosion, and extend the service life.
The working layer of the tank wall is generally built with carbon blocks. If silicon carbide bricks are used, the working layer can be thinned, which is conducive to expanding the tank capacity, improving its thermal conductivity, corrosion resistance and mechanical strength, and is particularly suitable for high-power or fast-cooling aluminum electrolytic cells. For example, when carbon bricks were used originally, the thickness of the side wall was about 200-400mm. After using silicon carbide bricks combined with silicon nitride, the thickness of the side wall is only 75mm. Silicon carbide bricks combined with silicon nitride. At the same time, a eutectic of alumina and cryolite can be formed on the surface of the silicon carbide brick layer to protect the working layer of the tank wall and extend the service life. The working layer of the tank bottom is built with carbon blocks, with a thickness of 400-500mm. A metal conductor is buried in it, and the surrounding area is compacted with carbon refractory ramming materials to form the cathode lining. In the early stage of electrolytic cell production, due to the thermal stress and the chemical reaction between carbon bricks and aluminum liquid, the volume of the masonry expands, causing the carbon bricks to arch or crack. As a result, the electrolyte and aluminum liquid penetrate into the cathode lining, affecting its service life. Therefore, the requirements for carbon block masonry joints are small to prevent leakage. The working layer of a small electrolytic cell can be rammed into an integral lining with carbon refractory ramming materials. The average service life of the aluminum electrolytic cell lining is 3-4 years. When silicon carbide bricks are used as the tank wall and high-efficiency adhesives are used to build the carbon blocks at the bottom of the tank, its service life can be increased to 4 to 7 years.
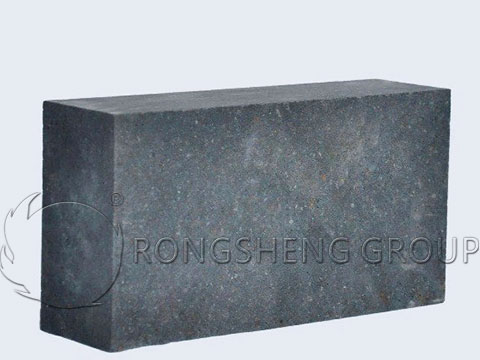
Refractory Materials for Aluminum Smelting
Aluminum smelting furnaces mainly include reverberatory furnaces, rotary drum furnaces and induction furnaces, and the operating temperature is generally 700-1000℃. The damage to the lining of this type of furnace is mainly caused by the penetration and erosion of aluminum liquid. The lining is generally built with clay bricks, high-alumina bricks and corundum mullite bricks, and can also be made of high-alumina refractory castables and refractory plastics. Due to good use conditions, the furnace has a long life.
(1) Refractory materials for reverberatory furnaces. The furnace is divided into fixed and tilting types, and generally uses gas or heavy oil as fuel.
Fixed reverberatory furnaces are usually used for aluminum smelting. The non-working layer of the reverberatory furnace is built with refractory fiber felt and clay insulation bricks, and the working layer above the molten pool is generally built with clay bricks, or it can be made of prefabricated blocks of high-alumina refractory castables hoisted or poured on site or rammed with high-alumina refractory plastics. The material of the molten pool working layer varies according to different usage requirements. In general, high-alumina bricks with an Al2O2 content of more than 75% are used for masonry, and high-alumina refractory castables with an Al2O2 content of 80% can also be used to cast the entire working layer. When smelting high-purity aluminum metal, the molten pool working layer should be built with high-purity mullite bricks, zircon bricks or corundum bricks. In order to resist the penetration and erosion of aluminum liquid, large silicon carbide bricks are generally used for the aluminum outlet, aluminum flow trough and its lining. The refractory materials used in the insulation furnace and its flux and alloy material treatment room are basically the same as those of the reverberatory furnace. When electrolytic aluminum liquid is used as raw material, the aluminum liquid is first sucked out from the bottom of the aluminum electrolytic cell with a siphon or vacuum bag. Then it is transported to the reverberatory furnace and poured into the charging port. After loading, oxygen is blown into the molten pool while heating for dehydrogenation treatment. The siphon lining is generally made of refractory fiber reinforced lightweight refractory castable as an insulation layer, and can also be built with 0.8g/cm³ clay insulation bricks. The working layer is generally built with dense clay bricks or corundum bricks. The insulation layer of the vacuum bag lining is the same as that of the siphon, and its working layer is built with high-quality clay bricks or high-alumina bricks. Under normal operation, the service life of the reverberatory furnace and the insulation furnace is generally 2 to 5 years.
(2) Refractory materials for rotary drum furnace. The non-working layer of the furnace is built with clay insulation bricks or floating bead bricks, and can also be cast with lightweight refractory castables with a bulk density of 1.0g/cm³ or made into prefabricated blocks. The working layer is built with dense clay bricks or high-alumina bricks with an Al2O2 content greater than 55%. The service life of a rotary drum furnace is generally 300 to 500 times. When salt flux is added to melt aluminum blocks, the service life is reduced due to increased chemical erosion.
(3) Refractory materials for induction furnace. The lining of the furnace is generally built with clay bricks or third-grade high-alumina bricks. The bottom of the furnace is sometimes first cast with a high-alumina refractory castable, and then high-alumina bricks are laid. When the capacity of the induction furnace is less than 10t, its lining can be made of high-alumina refractory castables or refractory ramming materials with an Al2O2 content of about 75%, or corundum refractory castables or dry vibrating materials. The lining around the coil of the furnace inductor is generally cast as a whole with corundum refractory castables or vibrated compacted with dry vibrating materials. Due to the different types of raw materials and operating conditions, the service life of the furnace also varies, and the general furnace life is 0.5 to 4 years. During use, the lining around the coil and other vulnerable parts should be repaired 1 to 5 times.
(4) Refractory materials for insulation furnaces and aluminum water tanks. Aluminum insulation furnaces are divided into trough induction furnaces, resistance heating pool furnaces, and gas chamber furnaces. Because of the low operating temperature of this type of equipment, clay bricks and other materials are generally used as linings, which also achieve a longer service life.