Refractory materials for copper and nickel smelting. The main process of copper pyrometallurgy is very similar to that of nickel smelting, with only the following differences: the product of the copper smelting converter is crude copper, while the product of the nickel smelting converter is high-grade nickel matte (nickel matte with high nickel content); copper electrolytic refining uses copper anode plates, while nickel electrolytic refining uses Ni₃S₂ anode plates.
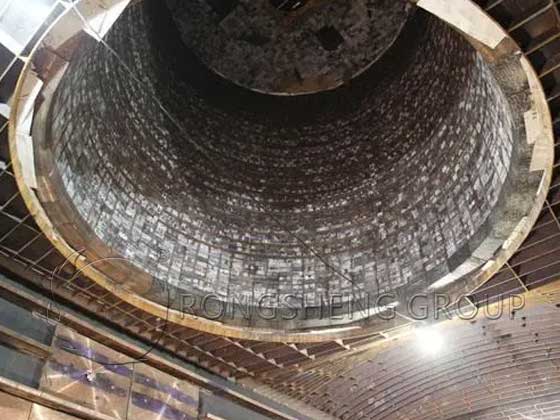
Refractory Materials for Copper and Nickel Smelting
Flash smelting furnace
Finland Outokumpu flash furnace and refractory lining. A Chinese smelter has built a copper smelting flash furnace, and a non-ferrous metal company has built a nickel smelting flash furnace. The flash furnace is mainly composed of a reaction tower, a sedimentation tank, and an ascending flue. Its advantages are that ore roasting and smelting are combined, the reaction is rapid, the energy consumption is low, and the pollution to the environment by the non-ferrous metal smelting process is greatly reduced.
The oxygen pressure in the upper part of the reaction tower is high, the temperature is low, and the tower wall forms a Fe₃O₄ protective layer, which is built with direct bonded magnesia-chrome bricks. The lower end wall and side wall of the tower and the side wall of the slag line of the sedimentation tank are in a harsh environment due to the high temperature and the erosion of high-temperature melt, the penetration and erosion of slag and matte. Therefore, these parts are built with cast magnesia-chrome bricks and installed with water-cooled copper sleeves. Cast magnesia-chrome bricks are difficult to produce, have low productivity and high cost, and have been replaced by molten grain-bonded magnesia-chrome bricks in recent years. The top of the tower is a spherical dome or a suspended flat top, made of directly bonded magnesia-chrome bricks.
Ausmelt furnace and Isa furnace
Ausmelt and Isa smelting methods were both invented in Australia, and both have top-blowing submerged lance technology. The two smelting furnaces only differ in furnace structure and fuel replenishment. A water-cooled copper (or steel) sleeve is installed between the lower shell of the two furnaces and the refractory material to reduce and stabilize the furnace temperature and reduce the corrosion of the furnace lining.
A smelter introduced two Ausmelt furnaces, one for copper smelting and the other for copper converting. The matching bricks at the time of introduction were magnesia-chrome bricks produced by RHI (about 20,000 yuan per ton). This brick is used in the Ausmelt smelting furnace, and the lining life is only 90 days. But when used in the Ausmelt converting furnace, the life span is more than half a year. Based on the results of this chemical thermodynamic analysis, the refractory company developed chromium-aluminum spinel bricks and used them on the Ausmelt smelting furnace of the Houma smelter for trial use. Experimental results show that the life of the furnace lining using this type of brick has now reached more than one and a half years.
Noranda furnace and silver furnace
The Noranda smelting furnace was developed by Canada. It is a horizontal long cylindrical molten pool smelting furnace. Daye smelting plant in my country has built this type of furnace. The Noranda furnace has a large production capacity and low energy consumption, and mainly relies on self-heating smelting. The vulnerable parts of the Noranda furnace are the tuyere, tuyere area, slag line in the precipitation area and the matte outlet. Originally, these parts were built with cast magnesia-chrome bricks. Now, except for the matte outlet, they have been replaced with molten grain rebonded magnesia-chrome bricks. The rest of the parts mainly use direct bonded magnesia-chrome bricks.
The silver furnace was developed by my country. Its principle is similar to that of the Noranda furnace. The vulnerable parts of the silver furnace are the tuyere and arch in the smelting area, and the partition wall and slag line in the precipitation area. Cast magnesia-chrome bricks or molten grain rebonded magnesia-chrome bricks are used in the tuyere area, and semi-rebonded magnesia-chrome bricks are used in the slag line area.
Converter
P-S converter is mostly used for copper and nickel smelting. P-S converter is a cylindrical horizontal converter. In order to improve the thermal and structural spalling resistance of magnesia-chrome bricks in the tuyere area of nickel smelting converters and reduce the penetration and erosion of ferrosilicon slag and nickel matte, the Cr₂O₃ and Al₂O₃ contents in magnesia-chrome bricks can be appropriately increased, and the Fe₂O₃ and impurity CaO and SiO₂ contents can be reduced. The increase in the Cr₂O₃ and Al₂O₃ contents in the bricks can increase the intergranular spinel content in the bricks, increase the degree of direct bonding and the strength of the bricks, and thus improve the bricks’ resistance to penetration and erosion of ferrosilicon slag and matte.
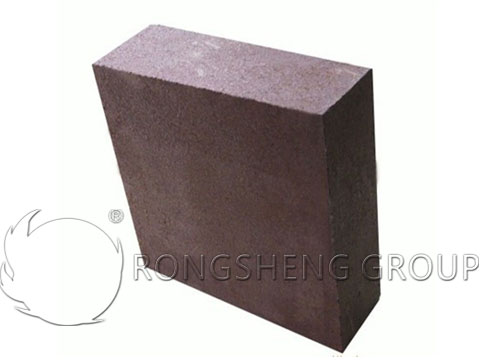
Refractory Materials for Lead and Zinc Pyrometallurgy
my country has rich reserves of lead and zinc ores. The minerals used for lead and zinc smelting are: galena (PbS), lead-zinc ore and sphalerite (ZnS). If it is a lead-zinc symbiotic ore, a process that can produce crude lead and crude zinc at the same time is required. If it is a single lead sulfide ore, a direct lead smelting method is used.
Oxidation bottom blowing molten pool direct lead smelting furnace (QSL method)
This method is to complete the sintering and roasting of sulfide ore and reduction smelting in one furnace at the same time. The furnace is closed and has a high sulfur recovery rate, which meets environmental protection requirements. The most severely corroded part of the QSL furnace is the magnesia-chrome bottom blowing brick (including the seat brick) of the oxidation zone nozzle. The reason for the severe corrosion may be that the oxygen pressure in this part is high, and Cr₂O₃ in the magnesia-chrome brick may be converted into CrO₃. However, due to its high density (10.6g·cm⁻3) and good fluidity, the lead liquid is easy to penetrate into the bottom blowing brick, and the infiltrated Pb is oxidized to PbO. The melting point is 886℃, and PbO is an alkaline oxide and forms a low-melting lead chromate compound (melting point is only about 800℃) with Cr2O2. This causes the structure and strength of the magnesia-chrome brick to deteriorate, so it is easily eroded. Therefore, zirconium corundum bricks are used as oxygen nozzles and seat bricks in this area.
Lead-zinc closed blast furnace (ISP method)
The lead-zinc closed blast furnace was developed by the British Imperial Smelting Company, also known as the ISP method, that is, the Imperial Smelting Method. This method can process lead-zinc paragenetic ores, but is not suitable for high-iron lead-zinc ores extracted by wet method. The body of the closed blast furnace is built with high-alumina bricks or andalusite bricks with good wear resistance. According to the chemical composition of the slag, it is obvious that the furnace hearth and front bed should be built with Cr₂O₃-containing refractory materials. Generally, the furnace hearth uses direct-bonded magnesia-chrome bricks, and the front bed is built with chrome slag bricks. The condenser and rotor are made of silicon carbide refractory materials because they require good thermal conductivity, erosion resistance and corrosion resistance.
Vertical tank zinc smelting distillation furnace
The vertical tank zinc smelting distillation furnace consists of a vertical tank (including the upper extension, tank body and lower extension), a combustion chamber, a heat exchanger, a condenser, etc. The tank body is built with silicon carbide refractory materials. The condenser has good thermal conductivity and is also made of silicon carbide materials.
Zinc Refining Furnace
The zinc distillation furnace consists of a melting furnace, a combustion chamber, a distillation tower and a condenser. Silicon carbide refractory materials are suitable for reducing atmospheres due to their good chemical stability, high high temperature strength, high thermal conductivity, good thermal shock resistance, wear resistance, erosion resistance, poor wettability of metal melts, and resistance to metal vapor erosion. Therefore, the trays, condensers and rotors of the zinc distillation furnace are made of high-quality silicon carbide refractory materials. The service life of the zinc distillation furnace is about 10 years, and the service life of the combustion chamber clay bricks is 2 to 3 years.
Zinc leaching residue volatilization kiln
In the production of zinc, wet extraction of zinc accounts for a large proportion. However, after wet extraction of zinc, its dilute sulfuric acid leaching residue still contains a lot of valuable metals such as Zn, Pb, In, Ge and some oxides or sulfides. The leaching residue contains up to 15%~20% zinc and 0.7%~6.0% lead. The volatilization kiln is used to recover zinc from the leaching residue.
The volatilization reaction section of the volatilization kiln is now better to build magnesia-aluminum-chrome bricks (bricks made of MgO-MgO·Al₂O₃ as large particles, magnesia sand and chrome concentrate as medium particles and fine powder) or chrome slag bricks.