What kind of material is used to paste acid-resistant bricks? Acid-resistant glue, epoxy resin glue? The material for pasting acid-resistant bricks needs to be based on the needs of the environment:
- If it is a general environment, then KP-1 type acid-resistant glue can be used, and the price is favorable.
- If it is in a specific environment, then epoxy glue is required, and the bonding strength will be stronger.
- In an alkaline environment, furan glue is required to ensure the bonding characteristics of the material.
Epoxy resin glue is used for glue, and industrial anti-corrosion special acid-resistant tiles are used for brick panels. Among them, epoxy resin glue is composed of epoxy resin, quartz powder, curing agent, etc. The manufacturer has launched modified epoxy glue, which is resistant to acid and alkali corrosion, can be constructed in a humid environment, and can be used after premixing on site.
Construction process: Old base treatment → brushing epoxy resin primer twice → epoxy glue preparation → epoxy glue bonding acid-resistant bricks → surface defect repair and maintenance.
Types of Cement for Acid-Resistant Bricks
There are many types of cement for laying acid-resistant bricks on industrial anti-corrosion floors. The most commonly used ones are: water glass acid-resistant cement, furan resin cement, epoxy resin cement, phenolic resin cement, etc. According to the site requirements and budget, which cement is suitable to use.
Water glass acid-resistant cement is divided into potassium water glass cement and sodium water glass cement. In terms of cost, it is the most cost-effective and widely used cement.
Epoxy cement is suitable for anti-corrosion floors in food workshops. The cost of directly laying acid-resistant bricks is higher. If acid-resistant cement is used to lay acid-resistant bricks, the cost of only using epoxy resin cement to fill the seams can be reduced, and the overall effect is the same.
Furan cement is suitable for chemical plants and can withstand environments within 150°C, but it has a strong reaction smell.
Water glass acid-resistant cement can withstand corrosion from various concentrations of phosphoric acid, oxidizing media, agricultural production systems, and dilute acids, but is not resistant to corrosion from fluorides and alkalis. Potassium water glass mortar has better water resistance than sodium water glass mortar, and its mechanical strength, bonding force and anti-penetration are better than sodium water glass mortar. It cures at room temperature, is easy to construct, and has a use temperature of <900℃.
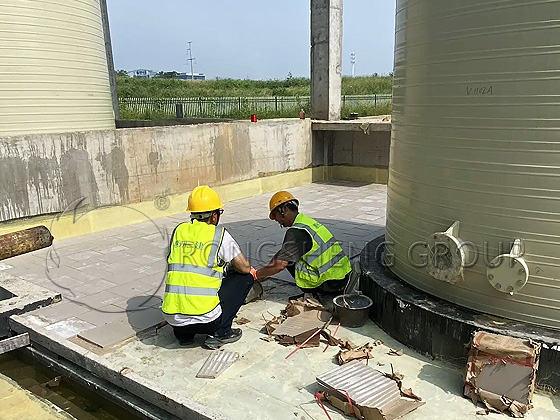
What are the Methods for Acid-Resistant Bricks Construction?
The construction methods of acid-resistant bricks mainly include the following:
-
Wet laying method:
Base treatment: Ensure that the surface of the base is flat, clean, and free of oil and floating dust. For uneven parts, cement mortar or fine stone concrete should be used for leveling.
Line positioning: Pop out cross lines on the base to control the laying direction and position of acid-resistant bricks.
Pre-impregnated bricks: Soak the acid-resistant bricks in water in advance to ensure that the bricks absorb water fully, but there is no visible water on the surface.
Laying mortar: Apply a thin layer of wet mortar on the base as a bonding layer.
Laying bricks: Lay the acid-resistant bricks on the wet mortar in sequence according to the predetermined position and direction, and tap gently with a rubber hammer to ensure that the bricks are tightly combined with the mortar.
Filling treatment: Use acid mortar or acid-resistant glue with a color similar to that of the acid-resistant bricks to fill the gaps to ensure that the gaps are filled and flat.
-
Dry paving method:
The base treatment and line positioning are the same as the wet paving method.
Laying a dry hard mortar leveling layer: Lay a layer of dry hard mortar on the base and smooth it with a wooden trowel.
Laying bricks: Place the acid-resistant bricks directly on the dry hard mortar leveling layer and tap them gently with a rubber hammer to make the bricks and mortar tightly combined.
Seam filling treatment: Also use acid mortar or acid-resistant glue for seam filling.
-
Empty paving method:
Base treatment and line positioning are the same as above.
Laying isolation layer: Lay a layer of isolation material, such as plastic film or linoleum, on the base.
Laying bricks: Place acid-resistant bricks directly on the isolation layer and tap them gently with a rubber hammer to fix them.
Filling treatment: Use acid-resistant materials to fill the joints.
-
Pasting method:
Mainly suitable for wall construction.
Use special acid-resistant glue or tile adhesive as a binder to paste the acid-resistant bricks on the wall.
Make sure the wall is flat, clean, and free of oil and dust.
Paste the acid-resistant bricks on the wall in sequence according to the predetermined position and direction, and tap them gently with a rubber hammer to ensure that the bricks are tightly combined with the wall.
Also use acid-resistant materials to fill the gaps.