The high-temperature kiln is the main core equipment in industrial production. It is all made of steel, and the interior of the kiln steel shell cannot be used without a refractory lining material. Because the strength of the steel cylinder of the kiln will decrease with the increase of temperature, especially when the temperature fluctuates greatly, the cylinder will be deformed. In this way, the high-temperature kiln will no longer be able to be used. Therefore, refractory lining materials, such as LZ-65 High Alumina Fire Bricks – High Alumina Refractory Bricks in South Africa, should be laid on the lining of the high-temperature kiln to cut off the high-temperature burning and protect the steel cylinder structure.
In order to reduce the consumption cost of refractory materials and improve the equipment operation rate and product quality, general enterprises will choose LZ-65 high-alumina bricks, which are cheap and high-quality, rich in raw material resources, and extensive reserves. In order to improve the service life of the kiln, strict quality inspection is required for each batch of bricks purchased into the factory. Because the use of high-alumina bricks that have passed the quality inspection is an important basis for the long-term safety of the rotary kiln.
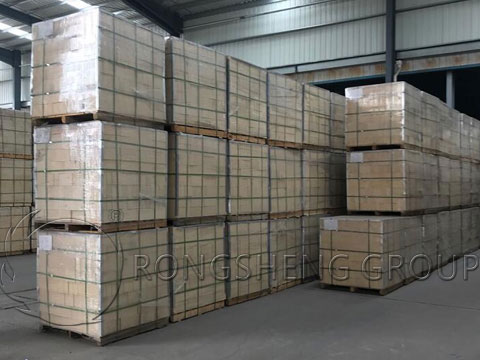
Advantages of LZ-65 High Aluminium Fire Bricks
In terms of price, LZ-65 high-alumina bricks are between the middle price of first-grade high-alumina bricks and third-grade high-alumina bricks. High Alumina Refractory Bricks in South Africa. In terms of material, the AL2O3 content of LZ-65 high-alumina bricks is nearly 12 percentage points higher than the 55% content of third-grade high-alumina bricks, and the content of AL2O3 produced by many manufacturers is basically close to 70%. In terms of the operating temperature environment, it can meet 80% of the high-temperature kilns with a working temperature between 1300 °C and 1400 °C, so many customers will prefer LZ-65 high alumina bricks when purchasing high alumina bricks.
Alumina is the main high-temperature resistant component in high alumina brick products. Moreover, alumina is one of the main oxides sintered at high temperatures to form mullite. Mullite is the only binary compound that exists stably under normal pressure in the AL2O3-SiO2 binary system. The chemical formula is 3AL2O3 2SiO2, and its theoretical composition is AL2O371.8%, SiO228.2%. It has the characteristics of uniform expansion, excellent thermal shock stability, high load softening point, small high temperature creep value, high hardness, and good chemical corrosion resistance. The AL2O3 content of LZ-65 high alumina bricks is generally around 67%. Therefore, the brick is a mullite brick, mainly because the mullite crystal is needle-shaped, forming a cross-network structure, and a small amount of glass phase is filled in it. The structure is dense, can withstand stress, and high-temperature resistance is not easy to deform, and has good high-temperature strength. LZ-65 High Aluminium Fire Bricks. When the brick is used in the kiln, it is re-fired again to produce secondary mullite, which is beneficial to improve thermal stability and compressive strength. It also promotes the increase of the starting temperature of softening under load and enhances the stress generated during the load and operation of the kiln. At high temperatures, it does not lose structural strength, does not soften, deform or collapse, has a small thermal expansion, and is stable in volume at high temperatures.
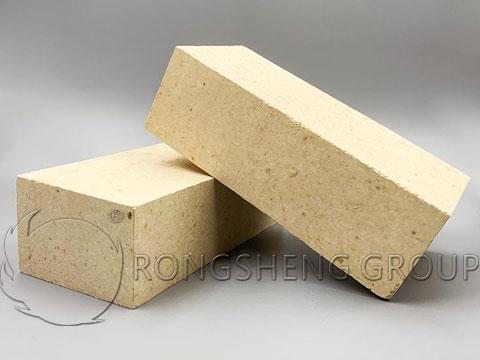
LZ-65 High Aluminium Fire Bricks Physical Change Advantages
The room temperature compressive strength of LZ-65 high alumina brick is a parameter of its structure, especially a sensitive parameter of its fiber structure. The formation of material microstructure is restricted by various technological factors in the material preparation process. Such as the characteristics of raw materials and the proportion of ingredients, particle size, and gradation, as well as the bonding between particles, the molding method, and the sintering state, all have an important impact on the microstructure of the material. The normal temperature compressive strength is a reliable method to test the current process conditions. In addition, other mechanical properties can be indirectly evaluated by the compressive strength at room temperature of the material. Good wear resistance and impact resistance are all corresponding to its high normal temperature compressive strength. Therefore, the compressive strength at room temperature is an important indicator for judging the quality of the product. After testing, the compressive strength of LZ-65 high aluminum Fire Bricks will have high wear resistance in the range of 55MPa.
LZ-65 High Alumina Fire Bricks – High Alumina Refractory Bricks in South Africa have three types of porosity, including apparent porosity, closed porosity, and true porosity. Since it is difficult to directly measure the volume of closed pores, the porosity index of materials is usually expressed as open porosity, that is, apparent porosity. Porosity not only reflects the density of high alumina bricks but also reflects whether the manufacturing process is reasonable. He affects almost all properties of high alumina bricks, especially strength, thermal conductivity, corrosion resistance, thermal shock resistance, etc. Generally speaking, porosity increases, strength decreases, thermal conductivity decreases, and erosion resistance decreases. Therefore, the apparent porosity of LZ-65 high alumina brick is generally between 21-22 as a suitable index.
Contact us for free samples and quotes for LZ-65 High Alumina Fire Bricks – High Alumina Refractory Bricks in South Africa.