We think the refractories for hot blast stove sales can use high aluminum brick, because high aluminum brick is one of the common refractory bricks for high temperature kiln and thermal equipment. Some parts of the temperature sharp cooling hot or temperature variation of the larger area, which requires high aluminum brick to have excellent thermal shock resistance.
We generally think that the thermal shock resistance of refractories for hot blast stove refers to the resistance of the refractory material to the damage caused by the rapid change of temperature. In fact, thermal shock resistance can also be referred to as thermal shock stability, thermal shock resistance, thermal shock resistance and thermal resistance. Examples: ladle in the process of steel, pouring or stop pouring;In the process of feeding, smelting and producing steel;During the intermittent process, due to the sharp change of temperature, the furnace lining refractories crack, flake and even damage, which is one of the main causes of lining refractory damage.
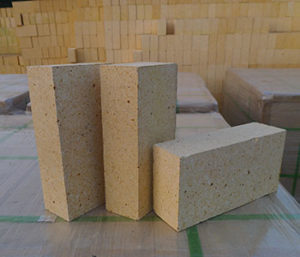
So, what are the technological measures to improve the thermal shock resistance of refractories? We’ve sorted out a few ways.
1. Selection of raw materials and admixtures: refractories for hot blast stove sales and manufacturing should choose raw materials with small linear expansion coefficient and high thermal conductivity. On the premise of not affecting other properties of refractory materials, additives with small linear expansion coefficient and high thermal conductivity should be used.
2. Microstructure optimization of materials: it is suggested that the second phase is added to the refractories for hot blast stove, and the phase transition is used to produce micro-crack to enhance toughness and improve thermal shock resistance.
3. Under the premise of satisfying the use conditions, the specification and size of firebrick are required to be accurate.
The refractories for hot blast stove sales and manufacturing, we believe that high alumina clinker and white fused alumina powder as raw materials, adding an appropriate amount of expansion agent, after molding and 800 degrees of heat treatment, can be made to high aluminum brick thermal shock resistance.In addition, the mixing is carried out in the mixer. Firstly, 50% chemical binder is added into the coarse particles. The particle size composition of the mud is as follows: 5-3mm18.4%,3-1mm26.7%,1-0.5mm3.5%, 0.5-0.1mm8.2%, less than 0.1mm43.2%, moisture 3%, and trapped material for over 2H. The refractory bricks are formed on a 300T friction press to increase The Times of pressure and the maximum impact force to ensure the quality of the bricks. The volume density is greater than 2.85g/cm3.After the bricks were dried at 160 degrees, the firing temperature in the inverted furnace was 1430-1450 degrees and the holding time was 40H.It can be used for the top of 5T electric furnace without spalling and chip dropping.
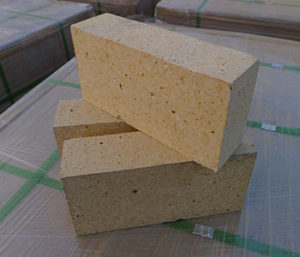
This is the content of refractory material we share with you today. If you want to know more about refractory material, you can call us. I will serve you with all my heart.