The production process of magnesia carbon bricks is mainly made of electrofused magnesia and flake graphite as main raw materials, phenolic resin as binder, and some antioxidants added through the processes of heat maturation mixing, high pressure molding and heat treatment. Magnesia carbon brick sales even by ultra-high arc burning, the loss of quality is very small, linear expansion coefficient is very small. The strength of graphite increases with the increase of temperature. At 2000℃, the strength of graphite doubles.
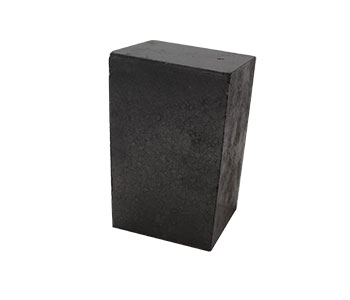
The excellent performance of magnesia carbon brick depends on the existence of the carbon in the brick. The oxidation of the carbon in the process of using the brick is easy to cause the tissue deterioration of the product, which makes the slag penetrate into the brick along the gap, corrode the magnesia particles and reduce the service life of the magnesia-carbon bricks. At present, the antioxidant properties of magnesia carbon bricks are improved mainly by adding antioxidants. The principle of choosing antioxidants for magnesia carbon brick sales is mainly to judge the possible coalescence phase and the vapor pressure of each gas phase based on thermodynamic data and service conditions, compare the possibility of CO reaction between each coalescence phase and oxygen affinity capacity, and analyze the influence of various reactions on the microstructure of refractory brick.
Magnesia-carbon brick is made of magnesia, re-fired magnesia, electrofused magnesia, high purity magnesia, high quality graphite and bauxite additive. Magnesia carbon brick sales performance and refractory brick graphite content has a great relationship. With the increase of graphite content, the strength of brick decreases, thermal expansion rate decreases and residual expansion rate increases. Therefore, the graphite content of refractory bricks should be controlled at 20% or so. Magnesia-carbon refractory brick has low wettability to slag, excellent resistance to spalling and erosion, and is suitable for slag line of ladle, especially for multi-furnace casting. In order to meet the needs of producing clean steel, its application has been expanded from slag line to side wall during the refining of ladle. It is mainly used for lining and outlet of steelmaking oxidation reformer, hot spot of furnace wall of high power electric furnace, lining of refining furnace and slag line of steel barrel.
Magnesia-carbon brick, as a kind of composite refractory material, makes good use of the strong slag resistance of magnesia and the high thermal conductivity and low expansibility of carbon, and compensates for the poor spallation resistance of magnesia. It has good high temperature resistance, slag resistance, thermal shock resistance and low temperature creep. Magnesia is the main raw material for producing magnesium carbon brick. The quality of magnesia has a very important influence on the performance of magnesia carbon brick. How to choose magnesia rationally is the key to produce this series of refractory brick. The magnesite includes fused magnesite and sintered magnesite, which have different characteristics. Electrofused magnesite has large grain size, less impurity, less silicate phase, higher direct grain bonding degree and less grain boundary. The grain size of sintered magnesite is fine, the impurity and silicate are relatively more, and the direct bonding degree is poor.
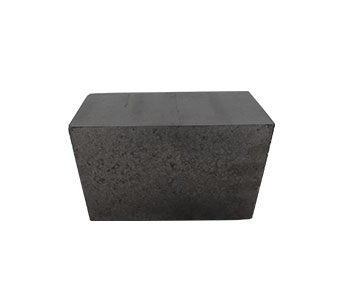
Zhengzhou Rongsheng Kiln Refractory Co.,Ltd. is professional refractory material manufacturer. We are committed to the production of high quality refractory products, and more than 60 countries and regions of customers to achieve long-term friendly relations of cooperation, product quality is stable and reliable, complete qualification certification, worthy of customer trust, welcome everyone to come to our consultation and procurement, we will serve you wholeheartedly.