At present, the lining of the refining electric furnace is made of knotted magnesium ramming material, which is often used to produce medium and low carbon ferromanganese or medium and low carbon ferrochrome. The service life (furnace age) of the medium and low carbon ferromanganese lining is generally about 400 furnaces. If it encounters peak production, its service life will be shorter. The life of the lining plays a very important role in production. If the service life is too short, the product cost will increase significantly. At the same time, it will also reduce the production operation rate of the electric furnace and increase the labor intensity of the workers. What’s more, it will also bring major hidden dangers to the safety of the workers. Therefore, extending the service life of the electric furnace lining can not only reduce production costs but also increase production to achieve the purpose of improving labor productivity. At the same time, it can reduce some safety hazards of workers and create greater economic benefits for the enterprise. RS Refractory Materials Manufacturer, supplies knotted materials for refining electric furnace lining, contact Rongsheng for detailed information.
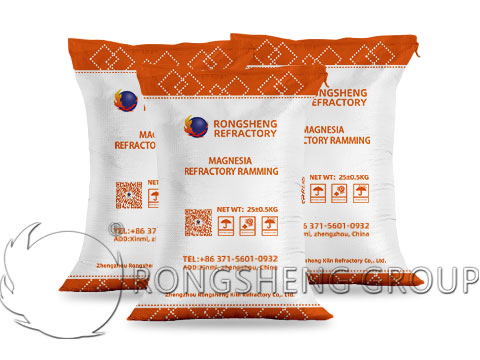
Requirements for knotting materials in refining electric furnace lining
The MgO content in the knotting material is 82% and the SiO2 content is 4%. Since MgO is an alkaline oxide and SiO2 is an acidic oxide, the two can easily combine to form silicates at high temperatures. In the process of forming silicates, a part of MgO can be consumed, which aggravates the damage to the furnace lining. If the MgO content in the knotting material is increased and the SiO2 content is reduced, the probability of forming silicates will be reduced, which can ensure the life of the furnace lining at the source. Therefore, it is necessary to select special magnesium ramming materials to ensure the extension of the service life of the furnace lining.
Requirements in the knotting process of electric furnace lining
During the knotting process, the furnace refractory lining is generally knotted layer by layer with dry ramming materials. In order to compact the knotting materials, the height of each layer is required to be no more than 200mm. Put a piece of colored strip cloth on it, and then divide it into multiple circles of different sizes from outside to inside according to the diameter of the vibrating rod along the circle of the furnace bottom on the colored strip cloth. After knotting, the vibrating rod is tied back and forth along the arc in a clockwise and counterclockwise direction. Many companies use one-way knotting or irregular knotting methods, but in fact, this method does not have a good knotting effect on the ramming materials. By adopting the clockwise and counterclockwise knotting method, the holes of the knotted materials can be knotted to the smallest, and the knotted materials are most reliable. After one layer is knotted, take out the colored strip cloth, and use a rake to rake out a “cross” groove about 20mm deep and 10mm wide on the knotted furnace bottom layer to facilitate the close combination between layers. In this way, the furnace bottom is not easily eroded during the production process, and its service life will naturally be extended.
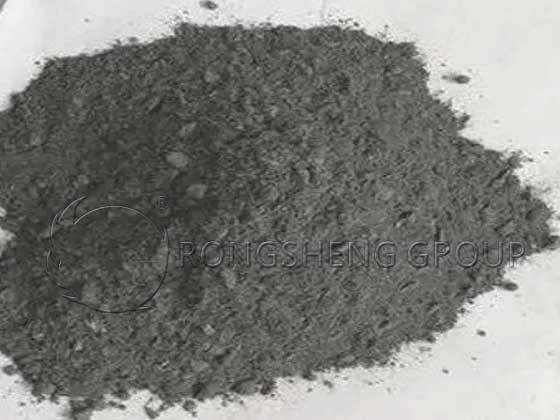
Requirements for raw materials used in medium and low carbon manganese iron
The raw materials used in medium and low-carbon ferromanganese are mainly manganese ore, manganese silicon processing powder and lime. Among these raw materials, manganese ore has the greatest impact on the life of the furnace lining. Generally, wet manganese ore will cause fire after entering the furnace, which will cause great damage to the furnace lining. Therefore, it is necessary to keep the raw materials entering the furnace dry, which can extend the life of the furnace lining.
Raw materials generally contain moisture to varying degrees, especially in the south. Due to heavy rain, manganese ore will be wetted by rain during transportation or storage. In order to ensure the dryness of the raw materials entering the furnace, a rotary kiln can be used for drying before entering the furnace for smelting. This can not only reduce production costs, but also reduce the erosion of raw materials on the furnace lining.
Process requirements in the production process of refining furnace
Requirements for bottom pile materials
Using ferromanganese silicon processing powder to start arc at the bottom pile can reduce the damage of the electrode arc to the furnace bottom. Under normal circumstances, 40% of the ferromanganese silicon consumption can be extracted from the bottom pile, which can prevent the rapid consumption of the furnace bottom.
However, when the furnace bottom is consumed slowly and the furnace wall is consumed too quickly, the life of the furnace lining will also be reduced. At this time, the bottom pile material should be cancelled immediately, and all the mixed materials should be put into the furnace, so as to ensure the reasonable consumption of the furnace bottom and the furnace wall at the same time.
Requirements for the smelting time of the first three furnaces
In order to ensure that the furnace bottom sintering meets the requirements and the furnace bottom does not turn over in the subsequent production process, the smelting time of the first furnace should be extended by 2 hours compared with the normal furnace time. The second furnace can be appropriately extended, and normal production can be resumed from the third furnace.
Timely furnace repair
During the consumption of the furnace bottom, there will be a phenomenon of rapid damage to the furnace wall. If the furnace is not repaired in time, the entire furnace lining will be destroyed. Therefore, when it is found that the furnace wall is severely damaged locally, it is necessary to stop and clean the slag hanging on the furnace lining around the damaged part, and then fill the configured furnace repair material into it and tamp it, and then unload the material and send electricity for production. Especially on both sides of the iron outlet, the molten iron is severely eroded here when the iron is tapped, and the furnace must be repaired frequently.
Rongsheng Refractory Material Factory is a refractory material manufacturer with rich production and sales experience. For various high-temperature industrial furnace lining refractory materials, Rongsheng manufacturers can provide suitable refractory lining material solutions according to actual road conditions. Whether it is refractory brick lining materials, refractory ramming materials, or thermal insulation refractory materials for insulation layers, you can find suitable lining material solutions at Rongsheng manufacturers. Looking forward to establishing cooperation with you.