As the lining refractory material of cement kiln walls, monolithic refractory material has been effectively used in various parts due to its advantages. As far as the types of refractory materials are concerned, in addition to general castables, castables such as dry spray coatings and wet spray coatings are mainly used. On the contrary, refractory plastics have outstanding advantages such as no maintenance after construction and no bursting. However, due to reasons such as construction efficiency and labor intensity of operators, its use is limited. Now, in order to overcome these shortcomings in construction, a plastic spraying construction method has been developed, which has been applied in various kilns and incinerators in the cement kiln and steel industry.
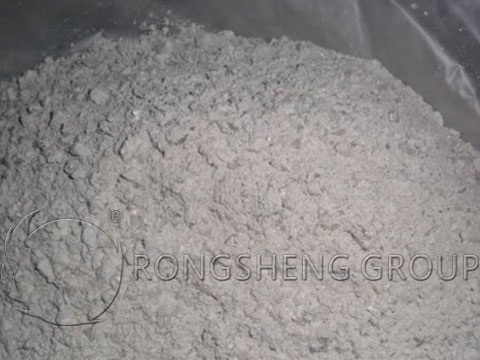
Characteristics of Refractory Spray Plastic
Refractory plastics are generally rammed with air hammers, so there are problems such as low construction efficiency and large vibration hazards. For the purpose of improving construction efficiency and improving the working environment, refractory sprayable plastic and its construction device have been developed and provided for use. The results show that this not only overcomes the disadvantages of construction but also brings into play the advantages of refractory sprayable plastic.
Compared with ramming construction, refractory plastic spraying construction has the following advantages.
- (1) High construction efficiency (several times that of ramming construction).
- (2) Construction personnel are not harmed by vibration.
- (3) No model is required, and furnace walls with complex shapes can also be constructed.
- (4) It is possible to produce heat-insulating material products using lightweight aggregates that are difficult to use due to damage caused by impact during ramming construction.
Practical Application of Refractory Sprayable Plastic in Cement Kiln
In the past, the cement kiln feed port that could be plasticized by ramming was sprayed and plasticized, and its actual use effect was tested. At the same time, refractory plastic is sprayed on the preheater and the inner cylinder of the cyclone dust collector to test its use.
- Simplify the installation position in the preheater and cyclone dust collector
Previously, ramming could be used for refractory plastic construction. But in order to shorten the construction period, refractory sprayable plastic is used. Compared with ramming construction, the comprehensive construction efficiency including construction preparation is about 2.5 times. After spraying construction, it has been used for one and a half years, and no obvious corrosion and peeling have been found. In good condition and still in use.
- Feed inlet part
In the past, the air hammer was used to pound the refractory plastic. After about a year of use, although some corrosion was found, it was still in good condition. After partial repair with the same material, it can continue to be used. In order to shorten the construction period, refractory sprayable plastic is used, and the effect of its use is as follows.
This time, the spraying is done according to the refractory plastic construction. The spraying machine is arranged on the channel on the lower side of the preheater. In order to make the supply hose rise vertically from the sprayer to the upper part, a hose is arranged, and the hose is extended into the kiln from the manhole at the upper part of the kiln tail. When spraying, divide the feed port into 8 equal parts in the circumferential direction. In order to prevent the rebound material from falling, use a partition to separate the left and right diagonally at two intervals of about 45 degrees. After spraying, turn the kiln in sequence, stop the kiln when turning to the same position at the next interval, and start construction. After spraying, process the surface of the construction body, and open a discharge hole every 100mm.
According to the actual use effect of refractory sprayable plastic, it can be seen that its construction efficiency is higher than that of ramming construction. In terms of quality, it also exerts the advantage of being refractory plastic.
Other Examples of Refractory Plastic Sprayable Construction
Furnace maintenance is carried out using a refractory plastic spraying process. Because the refractory plastic spraying ability is very strong, it can spray 3.4 tons per hour. In the originally planned 3-day renovation of the furnace roof, it took only 1 day to complete the refractory plastic spraying process. After four months of use tracking, it was found that the furnace roof with plastic spraying construction works well, and there is no shrinkage cracking. According to the calculation, the economic benefit of this transformation is more than 1 million yuan because of the shortened construction period of the spraying process and the indirect increase in production output.
Development of Refractory Plastic Spraying Technology
Plastic spraying technology is a new and efficient construction technology in the process of heating furnace maintenance. It can not only achieve the effect of traditional refractory plastic construction but also shorten the construction period and flexibly apply it to complex structural parts. In the actual maintenance work, this method has great advantages, and it is an important development direction of refractory and refractory plastic construction in the future.