Magnesia brick is a kind of alkaline refractory material with magnesium oxide content above 90% and magnesite as main crystalline phase. It can be divided into sintered magnesia brick and chemically bonded magnesia brick. The magnesite brick with high purity and high firing temperature is called directly bonded magnesite brick due to its direct contact with the granule of magnesite. The brick made of fused magnesite is called fused magnesite brick. Magnesia brick manufacturing has high fire resistance, good alkali slag resistance, high initial temperature of load softening, but poor thermal shock resistance. Sintered magnesia brick is made of magnesia brick as raw material. After grinding, batching, mixing and shaping, the sintered magnesia brick is made at a high temperature of 1550 ~ 1600℃, and the sintering temperature of high purity products is above 1750℃.
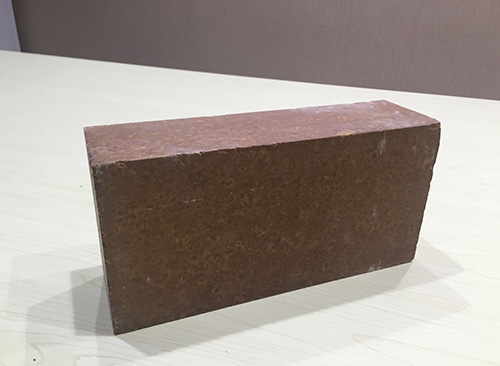
Magnesia brick is made by mixing, forming and drying magnesia sand with appropriate chemical binder. It is mainly used for making basic open hearth furnace, electric furnace bottom and wall, permanent lining of oxygen converter, non- ferrous metal smelting furnace, high-temperature tunnel kiln, lining of calcined magnesia brick and cement rotary kiln, bottom and wall of heating furnace, grid brick of regenerator chamber of glass kiln, etc. The appearance of magnesite is brownish yellow or tan, crystal density, burning <0.3%, no lumps, less black is better. After the sintering of brucite has been carefully selected, in order to completely remove the light burned composition and impurities of free lime, the digestion method can be adopted. Also, a certain amount of water can be added to the calcined brucite, and the lime can be removed with a sieve after weathering.
Various materials composed of different particles including waste brick, sintering agent and water were batched. In the manufacture of magnesia brick, in addition to sintered magnesite, often add less than 20% of the waste brick. Using sulfite pulp as binder. In addition, iron oxide, manganese ore, and clay minerals can also be added as binder. Minerals such as iron oxide, manganese ore and clay can be added to magnesite with low melting point solution to promote the crystallization of olitite and spinel in magnesite brick. The main function of olivine and spinel in magnesia brick is to enhance the mechanical strength of magnesia brick. Other impurities such as SiO2, Al2O3, Fe2O3 and other oxides can form a number of solid solutions around the magnesite calcite crystal to increase the density of brick tissue. In the magnesia brick manufacturing, organic matter may also be used as a binder in order to reduce the amount of solution.
The thermal friction property of magnesia brick is better than that of clay brick and silicon brick. Its highest value is around 900°C, above 900°C, due to low melting point impurities start melting and gradually decrease. The compressive strength is much higher than that of silicon brick and clay brick. In contrast to other refractory materials, the higher the temperature, the lower the thermal conductivity. The slag resistance of magnesia brick is very important because of its continuous contact with steel slag during use. Magnesia brick manufacturing slag resistance is very good, especially for alkaline slag has better performance than other materials.
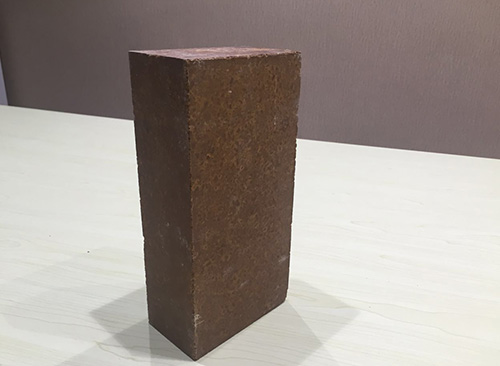
Magnesia refractory brick has been studied and applied more and more because of its good properties and rich raw materials. With the progress and development of science and technology, magnesia brick will be more and more widely used. It is mainly used for making basic open hearth furnace, electric furnace bottom and wall, permanent lining of oxygen converter, non-ferrous metal smelting furnace, high-temperature tunnel kiln, lining of calcined magnesia brick and cement rotary kiln, bottom and wall of heating furnace, grid brick of regenerator chamber of glass kiln, etc.