96A silica refractory bricks for glass kiln. Glass kiln is a key equipment for glass production. Its internal temperature is as high as 1500℃, which has extremely high requirements for refractory materials. 96A silica refractory bricks are an ideal choice for glass kiln lining due to their excellent performance. Rongsheng refractory material manufacturer can provide refractory bricks for glass kiln, such as glass kiln silica bricks, corundum bricks, AZS bricks, etc. Contact Rongsheng for free samples and quotes.
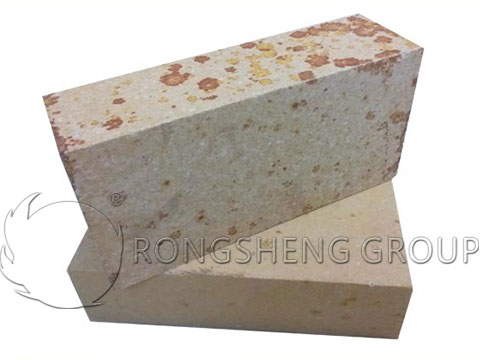
Performance characteristics of 96A silica refractory bricks
High refractoriness: The refractoriness of 96A silica refractory bricks is as high as 1750℃, which is much higher than the refractoriness of other refractory materials and can meet the use requirements of glass kilns in high temperature environments.
High strength: The compressive strength and flexural strength of 96A silica refractory bricks are both high, which can withstand the huge pressure and impact force inside the glass kiln and ensure the stability and safety of the furnace.
Good thermal shock resistance: 96A silica refractory bricks have good thermal shock resistance, can maintain structural stability under rapid temperature changes, and are not prone to cracks, peeling and other damage.
Low porosity: The porosity of 96A silica refractory bricks is low, which is conducive to reducing heat loss and improving the thermal efficiency of the furnace.
Good erosion resistance: 96A silica refractory bricks have good resistance to acid, alkaline and oxidative erosion, and can resist the erosion of corrosive gases and substances inside the glass kiln, ensuring the long-term use of the furnace.
Application of 96A silica refractory bricks in glass kilns
Glass kiln furnace lining: 96A silica refractory bricks are the main material for the lining of the glass kiln furnace, which can withstand thermal and mechanical stresses at high temperatures to ensure the stability and safety of the furnace.
Glass kiln combustion chamber lining: 96A silica refractory bricks are the main material for the lining of the glass kiln combustion chamber, which can withstand thermal and mechanical stresses at high temperatures to ensure the stability and safety of the furnace.
Glass kiln cooler lining: 96A silica refractory bricks are the main material for the lining of the glass kiln cooler, which can withstand thermal and mechanical stresses at high temperatures to ensure the stability and safety of the furnace.
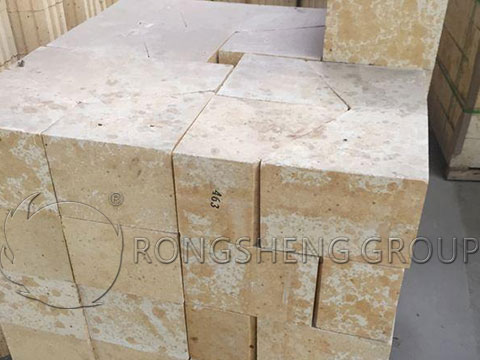
Construction method of 96A silica refractory bricks
Clean the foundation: Before construction, the inner wall of the furnace needs to be cleaned to remove oil, rust and other debris to ensure that the foundation surface is clean and flat.
Laying refractory bricks: According to the design requirements, lay 96A silica refractory bricks on the inner wall of the furnace layer by layer, and pay attention to controlling the thickness and levelness of the brick joints.
Anchor connection: During the masonry process, anchors are needed to firmly connect the refractory bricks to the inner wall of the furnace to improve the overall stability.
Baking treatment: After the masonry is completed, the furnace needs to be baked to make the refractory bricks gradually adapt to the high temperature environment and increase their service life.
In short, 96A silica refractory bricks have become an ideal choice for glass kiln linings due to their high refractoriness, high strength, good thermal shock resistance, low porosity and good erosion resistance. During the construction process, it is necessary to pay attention to controlling the quality of masonry to ensure the stability and safety of the furnace. By rationally selecting and applying 96A silica refractory bricks, the production efficiency and service life of glass kilns can be improved, maintenance costs can be reduced, and reliable support can be provided for the glass industry.
96A silica refractory bricks for glass kilns refer to silica bricks with SiO2≥96%, code: GB-96A. Silica bricks for glass kilns have the characteristics of high purity, high density, high strength, high load softness, and high refractoriness. They are resistant to acidic and alkaline steam erosion and have strong erosion resistance.
Refractory bricks for float glass kilns
The glass industry, especially the shaped refractory products used in float glass kilns, mainly include fused cast refractory materials, silica bricks and magnesia refractory products. Silica bricks are traditional products of refractory materials for glass kilns, which refer to refractory products with SiO2 content of not less than 93%. Silica bricks are made of silica with SiO2 content greater than or equal to 96% as raw materials, adding mineralizers and binders, and are made through mixing, molding, drying, and firing. The higher the SiO2 content in silica, the higher the refractoriness of the product. Silica bricks are acidic refractory products with strong acid corrosion resistance. Silica bricks have the characteristics of high load softening temperature, low density and low price. They are widely used in thermal equipment such as carbonization chambers, combustion chambers and partitions of coke ovens, glass tank kilns and kiln roofs, tank walls, high-temperature load-bearing parts of hot blast furnaces, and carbon roasting furnaces.
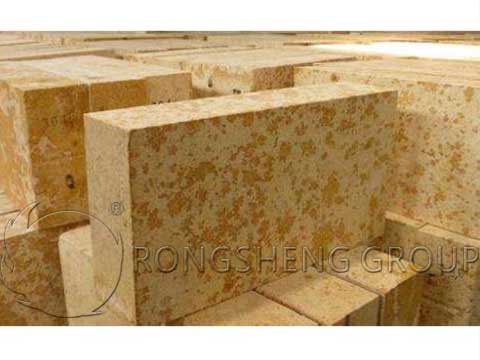
Introduction to the performance of silica bricks for glass kilns
(1) The volume is stable at high temperatures, and the furnace body will not change due to temperature fluctuations. Because the load softening temperature of silica bricks is high and the creep rate is small, the glass kiln can maintain the furnace body without deformation at 1600℃ and the structure is stable.
(2) No pollution to the glass liquid. The main component of silica bricks is SiO2. If there are pieces falling off or surface droplets during use, it will not affect the quality of the glass liquid.
(3) Chemical corrosion resistance. The silica bricks of the upper structure are corroded by the R2O gas in the glass mixture, and a lubricating degradation layer will appear on the surface, which will reduce the corrosion rate and play a protective role.
(4) The volume density is small, which can reduce the weight of the furnace body.
The main component of 96A silica refractory bricks used in glass kilns is silicon dioxide (SiO2). The silica bricks used in glass melting furnaces require an SiO2 content of more than 94%, an operating temperature of about 1600~1650℃, and a density of 1.8~1.95g/cm3. The apparent porosity is required to be less than 22%. The greater the porosity, the worse the quality of silica bricks. The appearance of silica bricks is mostly white crystals, and the microscopic composition is the crystals of tridymite. Because silica bricks undergo crystal transformation at high temperatures and expand in volume, especially at 180-270℃ and around 573℃, the crystal transformation is more intense. Therefore, during the kiln baking and cold repair process, it is necessary to adapt to the crystal transformation of silica bricks and adopt appropriate measures such as elastic tension bars. Expansion joints should be left in silica brick masonry.
The working temperature of silica bricks is about 200℃ higher than that of clay bricks, but the corrosion resistance to glass liquid and alkaline flying materials is poor. Therefore, it is used to build structures such as large arches, breast walls and small furnaces. When building, high-silicon refractory mud or silica brick powder and other materials close to the composition of silica bricks should be used as bonding materials.