Alumina Silica Fire Brick For Sale is the refractory brick which consists of Al2O3 and SiO2. Alumina silicate firebricks in Rongsheng Kiln Refractory Company are semi-silica bricks, fireclay bricks, high alumina bricks, mullite bricks and corundum bricks. If you want the high quality of Alumina Silicate Refractory Brick, please CONTACT RS Company! Quote us!
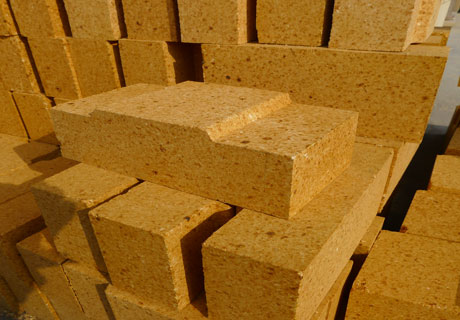
What Is Alumina Silica Fire Brick
Alumina Silica Fire Brick is the burned refractory brick which is mainly composed of Al2O3 and SiO2. The alumina silicate refractory brick is generally made of pyrophyllite, refractory clay, bauxite, sillimanite minerals and other natural raw materials, or the synthetic materials, like corundum and mullite.
Classification of Alumina Silica Fire Bricks
According to the content of the Al2O3 and SiO2, aluminium silicate bricks can be divided into semi-silica bricks, fireclay bricks, high alumina bricks, mullite bricks and corundum bricks.
Semi-silica brick
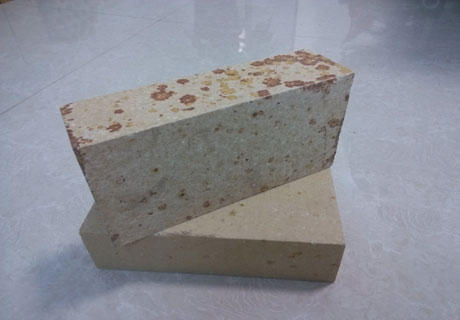
Semi-silica brick is an aluminum silicon refractory product with SiO2 content is more than 65%, and the Al2O3 content is between 15%~30%. Semi silica bricks are usually made of tailings and pyrophyllite obtained from the clay or kaolin containing quartz impurities. All the countries of the world use pyrophyllite to make semi silica bricks. As the most common refractory brick, the refractoriness of semi silica brick is about 1500~1610℃. The semi silica brick is widely used in coke oven, acid cupola, metallurgical furnace flue, ladle lining and hot metal tank.
Fireclay brick
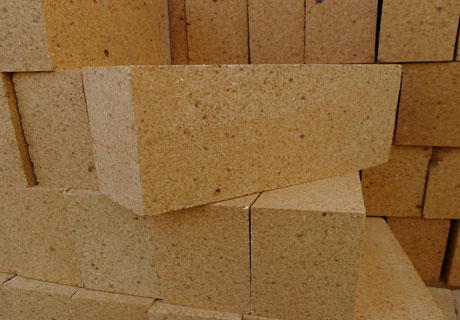
The mineral composition of fireclay bricks is kaolinite and 6~7% impurities. The firing process of fireclay bricks is the continuous dehydration of kaolinite and the crystallization process of mullite. SiO2 and Al2O3 in clay brick formed eutectic and low melting silicate during the sintering process, surrounded by mullite crystals.The refractoriness of fireclay brick is around 1690~1730℃. The thermal performance of fireclay brick is good and the fireclay brick can resist the extreme cold and extreme heat. The fireclay bricks are used in blast furnace, hot stove and glass kiln.
High alumina brick
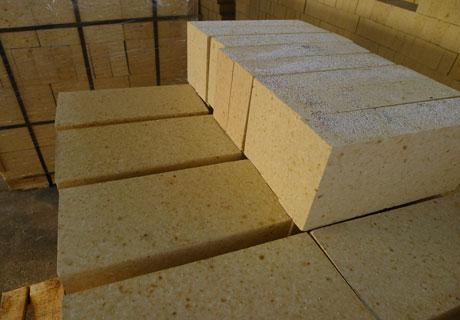
A neutral refractory brick with alumina content of more than 48%. The high alumina brick is formed and calcined from bauxite or other high alumina oxide raw materials. The thermal stability is good and the refractoriness is above 1770℃, with the characteristics of good slag resistance, high load soft and low creep. The high alumina brick is applied in the lining of steel making electric furnace, glass melting furnace and cement rotary furnace.
Mullite brick
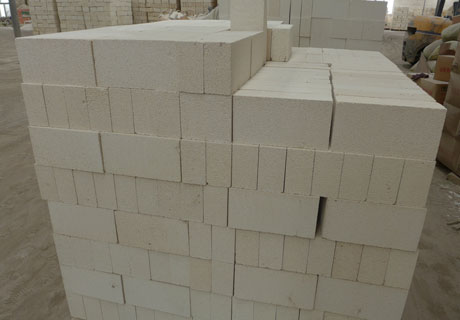
Mullite brick is the high alumina refractories with mullite as main crystal phase. The alumina content is 65~75%. the refractoriness is higher than normal high alumina brick, up to 1790℃. The softening of load starts at 1600~1700℃. The compression strength at normal temperature is 70 ~ 260MPa. The thermal shock resistance of mullite brick is good. Mullite brick is widely used in the top of hot blast stove, the hearth and bottom of blast furnace, the regenerator of glass furnace, the sinter kiln of ceramics, the dead angel furnace lining of petroleum cracking system, etc.
Corundum brick
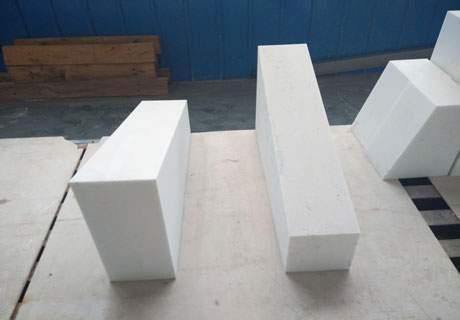
The content of Al2O3 of corundum brick is over 90% and the main crystalline phase in it is corundum. The corundum brick can resist the high pressure 340MPa at normal temperature. The high load softening start temperature is above 1700℃. The corundum brick has good chemical stability and strong resistance to acid or alkaline slag, metal and glass liquid. The corundum brick is mainly used in blast furnace, hot blast stove, steel refining furnace, sliding water device, glass furnace and petrochemical industrial furnace.
Properties of The Alumina Silica Fire Brick
- Light weight.
- Good heat resistance.
- Good thermal stability.
- Low thermal conductivity.
- Small heat capacity.
- Good chemical vibration.
- Good heating and heat preservation performance.
- Good expansibility.
Applications of The Alumina Silica Fire Brick
Alumina silica fire brick is commonly applied in all kinds of furnace lining.
The lining of molten steel ladle is built by alumina silica refractory bricks. In the iron and steel industry, a lot of mullite or corundum bricks are used in the hearth, the waist, the bosh and the other parts.
The main parts of the blast furnace are usually applied with ordinary fireclay bricks or high alumina bricks. The content of Al2O3 of fireclay bricks for blast furnace in Japan has increased from 38% to 42% and the apparent porosity has decreased from 20% to 10%, doubled the compression strength.
RS Cheap Alumina Silica Fire Brick For Sale! Interested? Contact Us Now!
The high density fireclay brick or kaolin brick used in Russia has a life span of more than 10 years. In America, the medium-sized blast furnace wall is made of dense fireclay bricks or high alumina bricks. High alumina bricks and fireclay bricks are also used in the blast furnace in Germany, France, UK, Australia and Italy. Most of the hot blast furnaces in every country are made of aluminum silicate bricks.
When the blast temperature is below 900℃, ordinary fireclay bricks are usually used. When the blast temperature is above 900℃, the lining is made of high alumina bricks, mullite bricks or sillimanite bricks.
Specifications of Alumina Silica Fire Bricks
Semi-silica brick | Fireclay brick | High alumina brick | Mullite brick | Corundum brick | |
Al2O3 | 15%~30% | 30%~48% | >48% | 72% | >90% |
SiO2 | >65% | 28% |
Alumina Silica Fire Brick Supplier
RS Kiln Refractory Company, as a leading alumina silica fire brick supplier in China, can provide all kinds of alumina silica fire bricks that you want. Customer satisfaction is RS company’s consistent tenet, ensuring the on site test rate of alumina silica fire brick is 100%. RS Kiln Company can guarantee you the best pre-sale, in sale and after-sale service! Any need? Just Email us for Price List.