Magnesia-carbon bricks are made of high-melting-point basic oxide magnesia (melting point 2800°C) and high-melting-point carbon materials that are difficult to be infiltrated by slag as raw materials and various non-oxide additives are added. A non-burning carbon composite refractory material combined with a carbonaceous binder. Magnesia carbon bricks are mainly used in the lining of converters, AC electric arc furnaces, DC electric arc furnaces, and slag lines of ladles. Magnesia carbon brick model, content 99%, density 2.95~3.05, can be customized according to the specifications provided by customers. Magnesia-carbon bricks are used for ladles for electric furnaces, and magnesia-carbon bricks for converters are available from Rongsheng refractory manufacturers with complete specifications. Converter magnesia carbon bricks, ladle magnesia carbon bricks, high purity, and high quality. Magnesia-carbon bricks, and aluminum-magnesia-carbon bricks, for converters, electric furnaces, and ladles, with complete specifications.
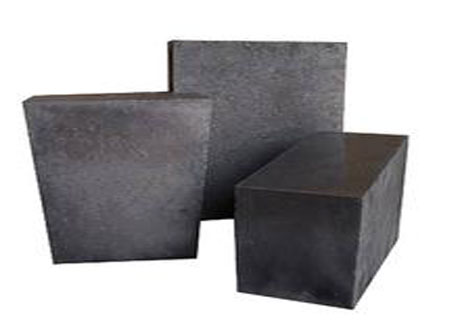
Magnesia Carbon Bricks Specification Requirements
As a composite refractory material, magnesia carbon brick effectively utilizes the strong slag erosion resistance of magnesia and the high thermal conductivity and low expansion of carbon to compensate for the biggest shortcoming of magnesia’s poor spalling resistance. Its main features are good high-temperature resistance, strong slag resistance, good thermal shock resistance, and low high-temperature creep.
Magnesia carbon brick size specification is a key topic because it is very important for steel production. Magnesia carbon brick is an important material commonly used in the lining of steel furnaces such as converters and electric arc furnaces. Its performance directly affects the production efficiency and quality of the steel industry. Therefore, the standard of magnesia carbon brick specifications is also very important.
Magnesia-carbon bricks for electric furnace converters, ladle refractory bricks, magnesia-carbon bricks for refining furnaces, and magnesia-carbon bricks are directly supplied by manufacturers. Refractory material manufacturers directly supply magnesia carbon bricks, and magnesia basic refractory materials MgO-C bricks, and can customize index specifications. SK-39 corundum magnesia carbon brick manufacturers and aluminum factories are available with complete supply. Magnesia-carbon brick special-shaped refractory brick for working lining of ladle electric furnace converter has stable performance. Carbon 12/14/16/18 Magnesia Carbon Brick Anti-flaking Anti-corrosion Basic refractory brick for ladle converter. Magnesia carbon brick thermal conductivity 1.12 compressive strength 35 specifications can be customized. Supply aluminum-magnesia-carbon bricks, refractory bricks, and carbon bricks for ladle converters, corrosion-resistant high-strength blast furnace lining refractory products.
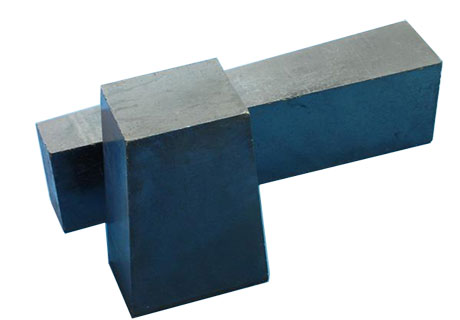
According to international standards, magnesia carbon bricks generally adopt a rectangular shape, and the size and specifications are also different. details as follows.
- Rectangular magnesia carbon brick
Rectangular magnesia carbon brick is the most widely used brick type at present, and its size is generally 340mmx 270mmx 55mm, 340mm x 270mmx 65mm, 400mm x 300mmx 55mm, and 400mm x 300mmx 65mm, etc. These specifications are formulated according to international standards and can be sold at home and abroad.
- Square magnesia carbon brick
Square magnesia carbon bricks are also very common, the size is generally 230mmx 230mmx 50mm, 230mm x 230mm x 65mm, 270mm x 270mmx 55mm, 270mmx 270mmx 65mm, etc. The specifications and standards for these sizes also follow international standards and have been widely used around the world.
- Other specifications
In addition to the above two commonly used specifications, magnesia carbon bricks also have other specifications and sizes. Such as rectangles, sectors, circles, etc. However, the specific use of these specifications of magnesia carbon bricks needs to be customized according to specific usage scenarios, and cannot be generalized.
Ladle magnesia carbon brick product name magnesia carbon brick moisture ≤ 0.5 Cr2O3% 35-45. Electric furnace magnesia-carbon bricks and magnesia-iron bricks are recognized by powerful refractory manufacturers with good product quality and high purity. Magnesia carbon brick, magnesia carbon brick for electric furnaces, magnesia carbon brick for converters, refractory brick for ladles, and magnesia carbon bricks manufacturers. Electric Furnace Magnesia Carbon Bricks Magnesia Aluminum Carbon Bricks have good slag resistance. Converter magnesia carbon bricks Ladle magnesia bricks have good purity and high quality. Magnesia carbon brick Unburned charcoal composite basic refractory material Used in ladle slag lines with strong slag resistance. Ladle magnesia carbon bricks require good thermal shock stability, corrosion resistance, and spalling resistance.
In short, the size and specification of magnesia carbon bricks are very important in actual use. The formulation of specifications and sizes that meet international standards can be promoted and applied globally, improving the efficiency and quality of steel production, which is of great significance to the entire steel industry.
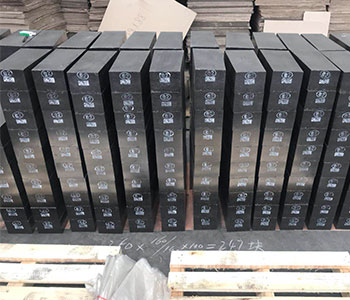
How to Prevent Oxidation of Carbon in Aluminum Carbon Refractory Products
Apply a layer of paint on the surface of aluminum-carbon refractory products to prevent carbon oxidation. The coating is a glassy material containing K2O, Na2O, and other fluxes, and its chemical composition is as follows: Al2O3>20%, SiO2>60%, R2O10~14%, and additives 5~10%. The optimum density of the coating is 1.6~1.8g/cm3, with a coating granularity: of 70~90% of the fine powder of <0.04mm.
Coating process: remove the dust on the surface of the coated product, and then apply the paint evenly. The thickness of the coating is preferably about 0.2mm. The products coated with paint are baked at 1000°C, which can make the products have better anti-oxidation performance.
Development of carbon-containing refractory products
Since the 1980s, the use of magnesia carbon bricks in oxygen converters has achieved great results. In recent years, carbon-containing magnesia dolomite bricks have attracted the attention of many countries because they are good for making clean steel. my country is rich in magnesite and dolomite resources. In the 1990s, while developing magnesia carbon bricks, magnesia dolomite carbon bricks should also developed accordingly.
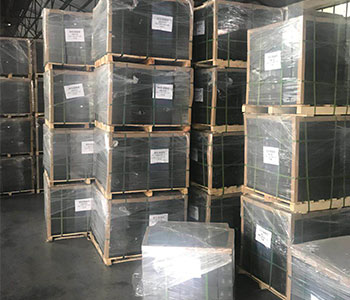
Magnesia-carbon bricks for working lining of ladle converters and electric furnace refractory bricks have stable metallurgical properties. Ladle magnesia carbon brick Refractory temperature 1790 ℃ Product name magnesia carbon brick Moisture ≤ 0.5. Converter magnesia-carbon bricks mainly use high-purity magnesia and synthetic magnesia-aluminum spinel sand as the main raw materials. Electric furnace magnesia carbon brick Thermal conductivity 0.4 Compressive strength 1MPa Product name magnesia carbon brick. Ladle magnesia carbon brick size 100MM single weight 5KG temperature 1200. G-3 Magnesia Carbon Brick – Dimensions can be customized on request. Electric furnace magnesia carbon brick thermal conductivity 1.04 compressive strength 9.6 refractory temperature 1750 ℃. Ladle magnesia carbon brick Product Features High-temperature resistance, heat resistance, slag resistance, refractory temperature 1800 ℃.
In terms of refractory materials for continuous casting, carbon-bonded products have been greatly developed. However, the oxidation resistance of carbon-bonded products is still poor and has a certain carburizing effect on molten steel. Therefore, oxide and non-oxide composite materials with good properties such as high-temperature strength, creep resistance, thermal shock resistance, and oxidation resistance. For example, zirconium corundum-mullite and SiC and BN composite materials will have broad development prospects.