Although there are many types of industrial furnaces, in terms of basic structure, they mainly include three parts. ①The heating system, which includes the equipment system that provides various heat sources to the materials in the industrial furnace. For example, energy medium pipelines and equipment systems, power transmission system transformer equipment, etc. ②Industrial furnace body, which is the basic structure of industrial furnace. Generally include a frame support structure, furnace body structure, material conveying system, etc. ③The smoke exhaust system, which mainly includes flue, chimney, heat exchanger and smokes exhaust auxiliary equipment, etc. ④ Other supporting equipment.
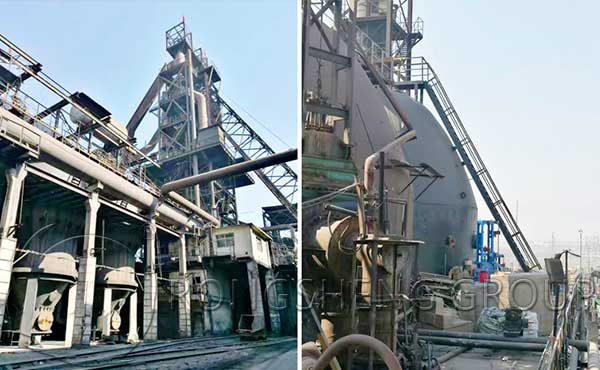
When designing the lining structure of an industrial furnace, it is a key procedure to realize the purpose of the equipment process by completing the basis of the building materials to the lining structure. This article mainly introduces the structure of the furnace lining with refractory materials as the main material. In the design process of the furnace lining, usually, the following aspects need to be paid attention to.
- (1) Reasonable furnace size. This is determined by the production process served by the industrial furnace, and the furnace type size is subject to the process requirements and the overall design of the equipment. Furnace size is the basic condition of the industrial furnace production process. Whether the lining size is reasonable or not directly affects the production of the entire process.
- (2) Stable structure. Due to the special purpose of industrial furnaces, the furnace lining is generally heated on one side. When the furnace lining is exposed to such an extreme temperature difference environment for a long time, the result will be structural damage, or stress deformation, or the formation of a molten layer on the hot surface, and the furnace lining structure will be greatly tested. Therefore, the stability of the lining structure is a key indicator of the lining design.
- (3) Economical and effective material configuration.
Configuration of Refractory Materials for Refractory Lining of Industrial Furnaces
Generally speaking, the lining structure of the industrial furnaces mainly has 4 forms.
- Refractory brick masonry lining.
- Unshaped refractory lining.
- Refractory ceramic fiber lining.
- Mixed lining body.
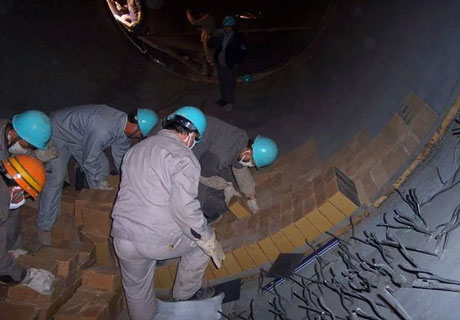
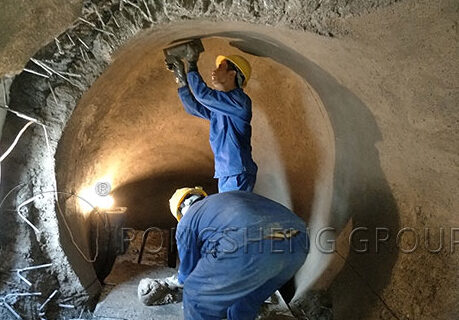
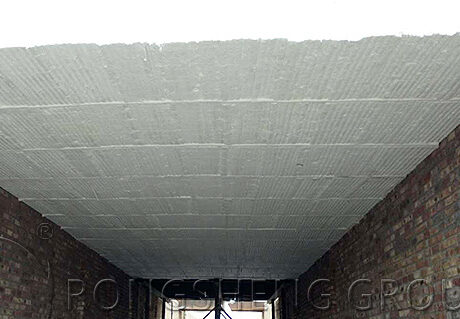
(1) Refractory Bricks Masonry Lining
Refractory brick masonry lining is composed of refractory bricks and refractory mortar. It is the most traditional and widely used form of masonry structure in industrial furnace body structure. When constructing or constructing an industrial furnace body structure with refractory bricks, first select refractory bricks and refractory mud according to the design or original structure requirements. Then, the construction of the masonry structure was completed according to the design drawings. Generally, there is masonry made of refractory bricks, which are mainly used for walls, furnace roofs, furnace bottoms, and pipes in the furnace body structure of industrial furnaces.
(2) Unshaped Refractory Lining
The so-called monolithic refractory lining means that the main material constituting the furnace lining is monolithic refractory. These unshaped refractory materials mainly include refractory castables, refractory plastics, refractory spray coatings, and so on.
Refractory castable. When refractory castable is used as the main material of the furnace body structure, it is used for the sidewalls, furnace roof, pipelining, and outer wrapping layer of the furnace body structure. It is also used as an insulation layer between the working layer and the furnace steel structure (such as the furnace shell).
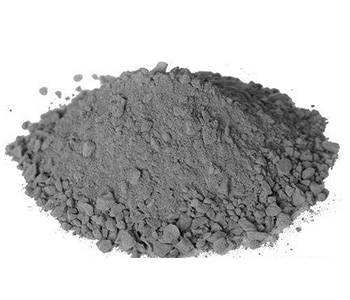
Refractory plastics. In theory, refractory plastics can replace the function of refractory bricks in the main structure of various industrial furnaces. But in actual application, you still need to study the following issues before making a decision.
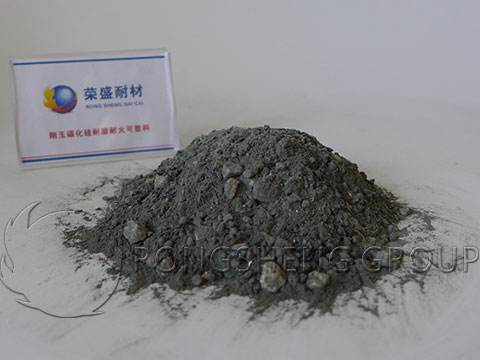
- ①The type and form of the stove. The furnace type to be considered is a melting furnace, a reaction furnace, or a heating furnace.
- ② Furnace structure. Whether the refractory material is required to be used is the top, sidewall, or bottom of the furnace. The construction thickness also needs to be considered. The presence or absence of insulation materials, the height of the furnace wall, and the load conditions are all factors that need to be considered.
- ③Operation of the furnace. Common road conditions information roughly include furnace temperature and its changes, whether the operation mode is continuous or intermittent, whether the state of the heated material is solid or liquid or gas, and the impact load in the furnace.
- ④Economy and construction conditions, etc. In the actual industrial furnace body structure, the most widely used refractory plastics are in the furnace roof and furnace walls.
Refractory spray paint. Because spraying construction has the advantages of being able to be at any angle, any position, and forming any geometric shape. Therefore, in the lining design of industrial furnaces, linings formed by spray coating are often used.
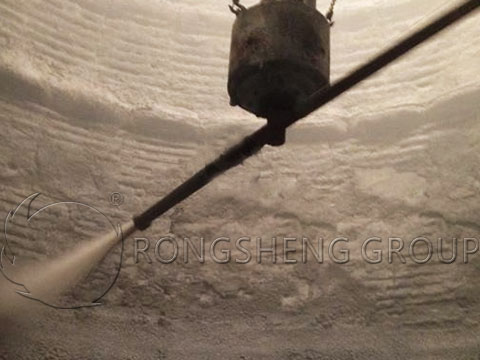
Since the characteristics of the spray coating are basically the same as the castable, the structure is also the same as the castable lining. The parts used in industrial furnace bodies include furnace walls, furnace roofs, pipelining walls, and insulation layers. In order to stabilize the structure of the spray coating lining, different forms of metal anchors or anchor bricks are usually arranged in the lining according to specific structural requirements.
(3) Refractory Ceramic Fiber Lining
As a kind of semi-finished raw material, refractory ceramic fiber is loose and can be processed into finished products such as fiber blankets, fiber ropes, fiber paper, fiberboards, and fiber bundles (foldable modules or stacked modules). After adding a binder, it can become fiber spray coating or fiber castable. Ceramic fiber can be used directly in loose form. But when it exists as a kind of lining, the ceramic fiber is often processed into products such as blankets, boards, or bundles for use.
Therefore, in the existing lining of industrial kilns, it can basically be determined that refractory materials must be used to protect the melting changes of the outer shell. To learn more about refractory lining materials, please continue to pay attention to our website. If you need to buy refractory materials for refractory furnace lining, please feel free to contact us.