Self-flowing refractory castables are materials that flow and degas by their own gravity, called self-flowing monolithic refractory castable. Its characteristic is that the performance of the self-flowing refractory castable is similar to or slightly better than that of the vibrating low cement refractory castables. No vibration equipment is needed, and no steel brazing is used to ram or strike the outer mold. Therefore, it can reduce construction costs, no noise pollution, and reduce labor intensity. The matrix material of self-flowing castable is of high quality and large amount. The aggregate needs to be processed to a round shape and use a material with a low water absorption rate, so as to ensure its self-flowing, exhausting, and compactness. Free to get prices of refractory monolithics, please email to RS Refractory Materials Manufacturer right now!
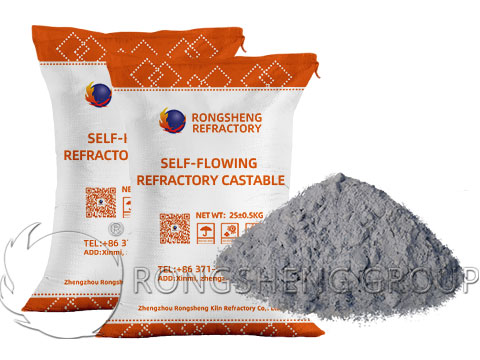
Get Free Quote
Flowability of Self-Flowing Refractory Castable Material
Under normal circumstances, the fluidity of self-flowing refractory castables is expressed by self-flowing value. Under normal circumstances, the self-flow value is controlled between 50%-100%. If the self-flow value is too small, the material fluidity is poor, and the castable cannot fill the model during construction, forming a dense lining. If the self-flow value is too large, materials may segregate during construction.
Realization of Self-Flowing Properties of Self-Flowing Monolithic Refractory Castables
The fluidity of self-flowing monolithic refractory material depends on the particle size composition and liquid phase properties, that is, the friction between the aggregates, and the viscosity and yield stress of the slurry.
Because in the refractory monolithic castables, the powder is mixed with water to become a pure slurry. Then, the fine aggregate is suspended in the pure slurry to become a mortar. Finally, the coarse aggregate is suspended in the mortar to become refractory castable.
In low cement castables, the proportion of aggregates is large, and there are many direct contact points between the aggregates, which hinder the flow of materials. Therefore, vibration is required to make the castable flow. On the contrary, the self-flowing monolithic refractory castable contains less aggregate and more matrix. In this way, there is little direct contact between the aggregate particles, the fine powder and water form a continuous fluid, and the material can flow under the action of gravity.
In order to have a certain degree of segregation resistance, there must be enough fine aggregate in the self-flowing refractory castable. In this way, it helps to increase the density and viscosity of the mortar. As the density of the mortar increases, the buoyancy of the mortar also increases, which offsets part of the gravity of the coarse aggregate and helps delay the sinking of the coarse aggregate. The viscosity of the mortar increases, which makes the mortar easier to enwrap the coarse aggregate to flow, and also helps to reduce segregation.
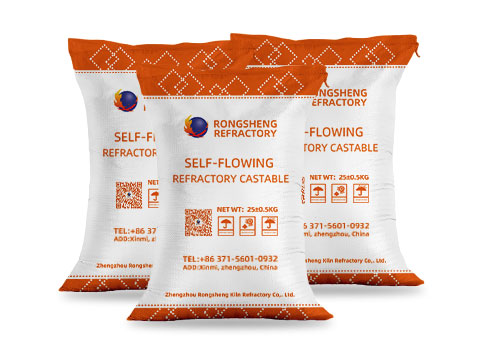
Get Free Quote
How to Keep Self-Flowing Monolithic Refractory Castables with Good Fluidity?
The main feature of the self-flowing refractory castable is that it can be poured into various shapes of self-flowing monolithic refractory castable without reducing or significantly reducing the performance of the castable by adding water appropriately and without vibration and ramming. What determines the fluidity of self-flowing castables?
In order to maintain good fluidity, self-flowing castables are mixed with more fine powder and micro powder. In this way, after curing, drying and calcination, the self-flowing monolithic castable refractory material is prone to greater shrinkage or “porcelain”. Therefore, self-flowing refractory castables need to be added with expansive substances such as “three stones” to offset the firing shrinkage. It is also necessary to control the proportion of the micro powder, control the composition and formation process of the binding phase, and prevent over-densification after burning. If controlled properly, self-flowing refractory castables can obtain physical and chemical properties close to low-cement castables.
Silicon powder is usually used as an additive in the preparation of self-flowing monolithic refractory castables. The quality of silicon powder will not only affect the fluidity of the self-flowing castable but also affect the performance of the castable. However, what we need to pay attention to is that there are still many types of silicon powder in refractory monolithics. Among them, silica fume has better performance and wider application. The main component of silica fume is amorphous silicon dioxide, which is spherical in shape and has a large flow. And because of the fine particle size of silicon powder, adding silicon powder to the self-flowing castable has a good effect on the voids formed between the particles in the refractory monolithic castables.
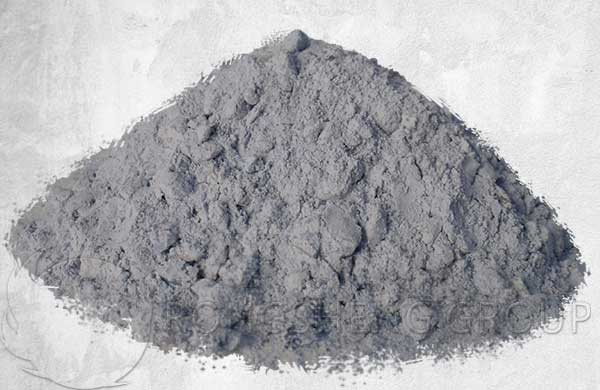
Get Free Quote
Self-Flowing Monolithic Refractory Castable Performance
Compared with low-cement castables, self-flowing castables have more water, lower bulk density, and higher apparent porosity. The self-flowing monolithic refractory castable has low strength after being treated at 105°C and 1400°C but has high strength at 1600°C. The self-flowing castable has good fluidity and can flow in a space with a complex shape or a narrow size. With the help of self-weight molding, a dense integral lining material can be obtained. Therefore, self-flowing castables are suitable for special parts that are inconvenient for construction or difficult to use other molding methods to obtain dense linings.
Features of Self-Flowing Refractory Castable
Self-flowing refractory castable is a castable refractory that can flow and degas without vibration. Its characteristic is that under the condition of not reducing or significantly reducing the performance of the castable, proper water is added, and it can be cast into various shapes of construction bodies without vibration. Self-flowing castables are especially suitable for thin-walled or complex shapes that cannot be formed by vibration.
The composition of self-flowing castables is developed on the basis of low cement and ultra-low cement castables. It is composed of refractory aggregate, powder, and high-efficiency dispersant with a certain particle size gradation. The key is the rational use of ultrafine powder particle size, quantity and high-efficiency dispersant so that the refractory monolithic castables can achieve self-flowing and automatic spreading.
In order to obtain good fluidity, the self-flowing castable has increased the powder content, and used a large amount of micro powder and additives. In this way, the cost is significantly increased. On the other hand, self-flowing refractory monolithics materials still cannot completely solve the problems of large water demand, high porosity, low bulk density and strength, and strong sintering ability.
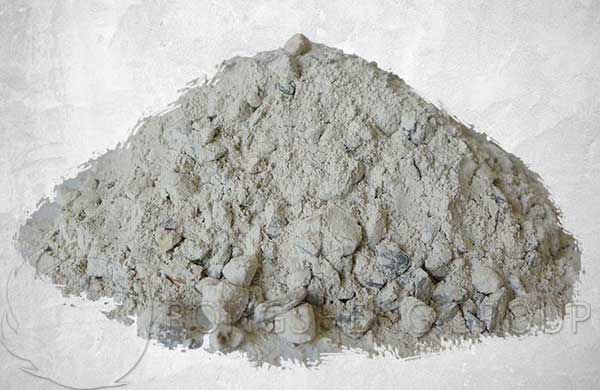
Get Free Quote
Compared with vibrating castables, high-performance self-flowing castables have the following advantages.
- (1) It can flow under its own weight without vibration.
- (2) It can automatically spread out and reach the parts that cannot be reached by the vibrating castable.
- (3) It can better ensure that the performance of the castable is fully reflected in actual use.
- (4) It can be pumped for construction, reducing labor intensity and speeding up the construction cycle.
- (5) Reduce noise pollution.
- (6) It is easy to carry out construction performance tests on site.
Application of Self-Flowing Refractory Castable
Self-flowing castables have many advantages that other types of castables cannot compare. Therefore, their use range is quite wide. It can be used for continuous casting tundish lining, electric furnace top triangle area, tap hole, ladle, heating furnace, blast furnace tap chute, CAS-OB furnace, cast iron induction furnace, boiler protection tube, etc.
On thermal equipment such as thin linings that are difficult to construct or repair, the economic benefits of using self-flowing castables are significant. At the same time, it has been applied to thermal equipment such as ladle and tundish, blast furnace tap and trench, boiler tube protection layer and incinerator protection row, heating furnace, and a cement kiln, and has achieved initial results. Since the self-flowing castable has good fluidity, it is mostly used in the circulating fluidized bed where it is difficult to construct and the erosion is more serious. The more commonly used is corundum self-flowing refractory castable.
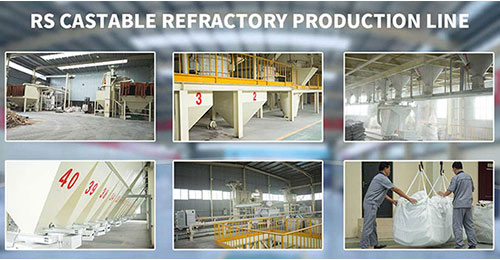
Get Free Quote
Rongsheng Refractory Monolithics Manufacturer
Rongsheng refractory monolithics manufacturers have rich experience in the production and sales of refractory monolithic castables. Rongsheng’s advanced and fully automatic monolithic refractories production line with an annual output of 80,000 tons. Rongsheng’s refractory materials products already have customers in more than 60 countries, for example, Russia, South Africa, Kazakhstan, Philippines, Chile, Malaysia, Indonesia, Vietnam, Kuwait, Turkey, Zambia, Peru, Mexico, Qatar, Egypt, etc. And these customers keep returning orders. If you need to buy high-quality refractory monolithic products, self-flowing monolithic refractory castables, high-alumina refractory castables, refractory plastics, refractory ramming materials, etc. Please contact the refractory manufacturer.