The shaft kiln, also known as the vertical kiln, vertical shaft kiln, is generally used for calcining limestone, clay, high alumina clinker, dolomite, magnesia, and cement clinker. Vertical shaft kiln refers to the thermal equipment that continuously calcines clinker with upper feeding and lower discharging. It is composed of a kiln body, feeding and discharging device, and ventilation equipment. Vertical shaft kilns are widely used for calcining various refractory raw materials and lime. Its advantages are less capital investment, less floor space, high efficiency, low fuel consumption, and easy automation. Rongsheng Refractory Materials Factory can provide high-quality refractory materials for vertical shaft kiln for sale, thermal insulation refractory fillers, etc. Contact us for free samples and pricing information.
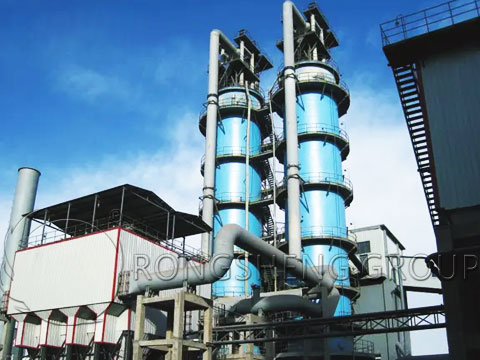
Requirements for Refractory Materials for Working Lining of Vertical Shaft Kilns
The size of the vertical shaft kiln is divided by its volume, and the volume of the commonly used shaft kiln is 100-300m3. The operating temperature in the vertical kiln varies with the calcined raw material, and the temperature of the calcined clay is 1250-1350℃. The temperature of calcining high alumina clinker and dense dolomite is 1500-1700℃. The masonry of the vertical shaft kiln is subject to high temperature and the wear effect of the falling charge, so the refractory material used should have basically the same chemical properties as the calcined raw material. Refractoriness is suitable for the calcination temperature of raw materials, and good high-temperature volume stability, mechanical strength, and slag resistance.
The vertical shaft kiln for calcining dolomite with a volume of 50m2 is lined with magnesia bricks in the high-temperature zone of the kiln. In general, clay shaft kilns can be lined with clay bricks due to their relatively low calcination temperature, generally at 1400°C. The calcination zone and cooling zone of the high-alumina vertical kiln should be built with high-alumina bricks, and clay bricks can be used for other parts. For the calcining vertical shaft kiln of basic refractory raw materials, due to the high calcination temperature, the calcination zone is generally built with high-quality magnesia bricks and magnesia alumina bricks. The vaporized cooling wall can also be used, and other parts can be built with clay bricks and high alumina bricks with higher strength.
The Working Principle of the Vertical Shaft Kiln
The vertical shaft kiln works according to the principle of countercurrent heat transfer. The material in the kiln moves from top to bottom, and the flue gas passes through the entire material column from bottom to top to preheat, calcine and cool in the kiln. Strict requirements for the block size of raw materials entering the kiln, generally 25-150mm. However, the kiln must be installed in stages, and the ratio of the maximum block size to the minimum block size should not exceed 2-3mm.
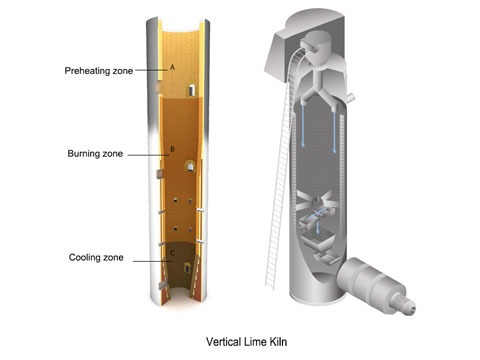
Refractory Lining Materials for Vertical Shaft Kiln
The cylinder body is a straight cylinder, the outer shell is a steel plate, and the inner lining is the refractory material. In the large lime shaft kiln using coke as fuel, the inner diameter of the kiln body in the lower part of the cooling zone is gradually reduced to connect with the discharge tray of the discharge machine. The upper center of the mechanized vertical kiln is equipped with a distributor, and two smoke exhaust ports are symmetrically opened on the side, which is connected with the dust collector or the chimney by pipes. The lower part of the kiln body is provided with a discharging machine. The chimney of the artificial vertical shaft kiln is located in the middle of the kiln roof, and the feeding doors are symmetrically arranged around the lower part of the kiln body. In order to avoid the phenomenon of materials sticking to the kiln wall, the shaft kiln for calcining dolomite and the shaft kiln for magnesia can be equipped with a vaporized cooling wall instead of the refractory brick lining in the calcining zone.
The kiln body refractory lining bricks are divided into 3 layers. The inner layer is the working layer, which is in direct contact with the material and is subjected to material impact, abrasion, and chemical erosion at operating temperature. In the middle is a protective layer, which protects when the working layer is excessively worn or burned through. The outer layer is a thermal insulation layer, and the high-temperature performance requirements of the calcined belt used as a lining brick material are relatively strict. Dolomite and magnesia shaft kiln calcination zone is 300-380mm thick, and the inner layer is made of magnesia brick or magnesia alumina brick and clay. The inner layer of the calcination zone of the high-alumina shaft kiln is 230-300mm thick, and high-alumina bricks are used. The inner layer of the satin-fired belt of the lime shaft kiln is 300-350mm thick and is built with clay bricks, high-alumina bricks, or magnesia bricks. The middle protective layer is generally 230mm thick, and the large lime vertical shaft kiln is 580mm thick and built with clay bricks. The thickness of the insulation layer is 60-70mm, using light clay bricks and insulation fillers.
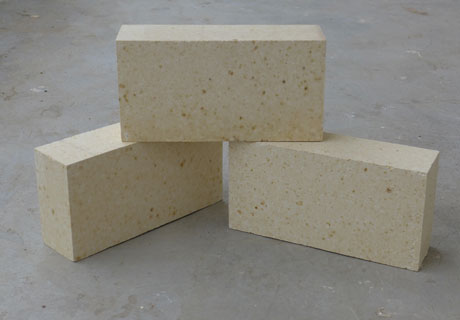
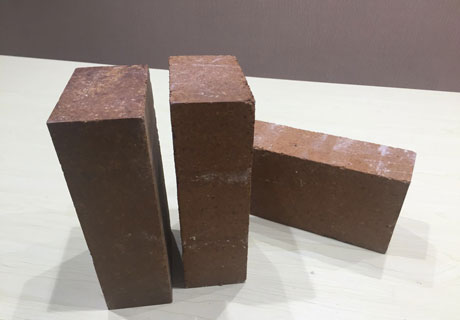
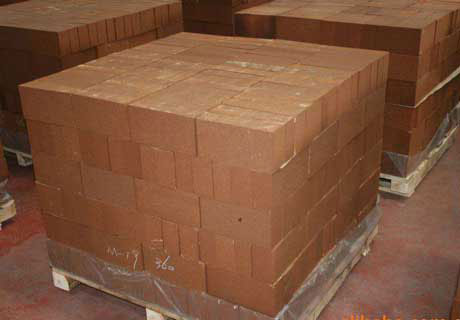
Refractory Material for Vertical Shaft Kiln for Sale from RS Factory
Rongsheng refractory production and sales manufacturer is a refractory manufacturer with rich kiln lining solutions. In many years of operation, we have accumulated a lot of working conditions of the kiln, as well as the demand for the refractory lining. This provides an effective reference for our improvement of refractory quality. Currently, our clients have edited more than 70 countries all over the world, such as South Africa, Philippines, Chile, Malaysia, Indonesia, Vietnam, Kuwait, Turkey, Zambia, Peru, Mexico, Qatar, Egypt, Russia, Kazakhstan, etc. If you need to buy refractory material for the vertical shaft kiln, or you need to buy high-quality magnesia bricks, magnesia alumina bricks, high alumina bricks, and other refractory bricks, refractory castables, refractory cement, thermal insulation fillers, and other refractory lining materials. Please contact us. We will evaluate the working conditions of your thermal equipment and then provide you with the most suitable refractory configuration for your production needs.