The alkali vapor corrosion of refractory materials is mainly related to the pore structure and chemical composition of the material. The pore structure mainly affects the penetration process of alkali vapor, while the chemical composition affects the chemical reaction process in the erosion process. Therefore, the method to improve the resistance of refractory materials to alkali vapor erosion should mainly be based on the perspective of the pore structure and chemical composition of the refractory materials.
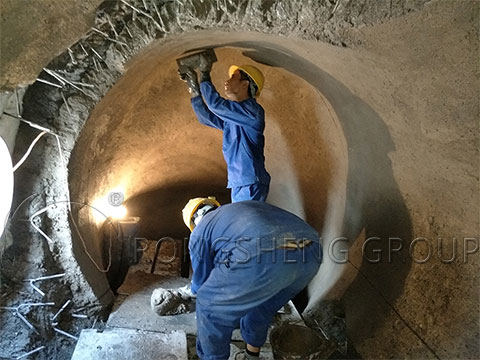
In order to improve the alkali corrosion resistance of refractories, in addition to the main components, certain additional components have also been introduced into the refractory system. This is because, on the one hand, the addition of ingredients can increase the densification of the material during the sintering process and reduce the penetration of corrosive substances. On the other hand, it can also change the viscosity of the slag during the erosion process or absorb some corrosive substances. For example, spinel can dissolve certain components in the slag during the slag erosion process, such as Fe2O3 and CaO. Increase the viscosity of the alkaline slag, thereby reducing the penetration of the slag into the refractory. Therefore, the introduction of spinel into the magnesia refractory material can significantly improve its resistance to penetration. In addition, by introducing the alumina component into the magnesia refractory material, a certain amount of spinel is formed in situ at high temperature, and the alkali slag penetration resistance will be further enhanced.
Chemical Components
Generally, the chemical composition of refractory materials is divided into main components, additive components, and impurity components according to the content and function of each component. The main component refers to the component that plays a decisive role in the properties of the refractory material and constitutes the matrix of the refractory material. As we all know, both refractory materials and slag can be divided into two types: acidic and alkaline. In order to improve the corrosion resistance of the material, the acidity and alkalinity of the corrosive medium need to be matched with the main component of the material. The basicity of slag is usually expressed by the ratio of alkaline oxide content to acidic oxide content. The most common is the ratio of CaO content to SiO2 content in the slag, namely:
The slag with high alkalinity is alkaline slag, and the slag with low alkalinity is acidic slag. Acidic slag contains more acidic oxides such as SiO2, B2O3, P2O5, V2O5, and fluoride. It is easier to melt and lose basic refractories, but it has weaker melting loss to acidic refractories. Alkaline refractories are more resistant to alkaline slag erosion, while acidic refractories are more resistant to acid slag erosion. For example, in cement rotary kilns, garbage incinerators, and glass kilns, most of them will use periclase-spinel, magnesia-chromium, dolomite, and other refractory materials as kiln linings.
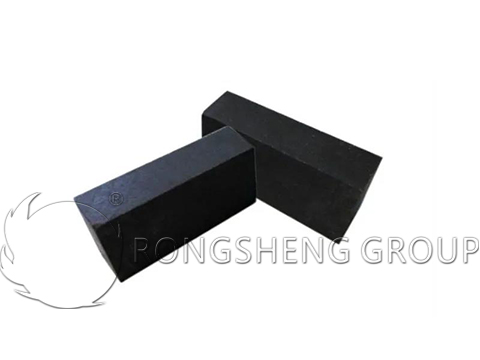
In order to improve the alkali corrosion resistance of refractories, in addition to the main components, certain additional components have also been introduced into the refractory system. This is because, on the one hand, the addition of ingredients can increase the densification of the material during the sintering process and reduce the penetration of corrosive substances; on the other hand, it can also change the viscosity of the slag during the erosion process or absorb part of the corrosive substances.
For example, spinel can dissolve certain components in the slag, such as Fe2O3 and CaO, during the slag erosion process to increase the viscosity of the alkaline slag, thereby reducing the penetration of the slag into refractory materials. Therefore, the introduction of spinel into the magnesia refractory material can significantly improve its resistance to penetration. In addition, by introducing the alumina component into the magnesia refractory material, a certain amount of spinel is formed in situ at high temperature, and the alkali slag penetration resistance will be further enhanced.
Pore Structure
The pore structure of refractory materials includes porosity, pore diameter, closed porosity, micropore ratio, and pore curvature. The pore structure can affect the air permeability of the refractory material and then affect the permeation process of corrosive gas in the refractory material. The fewer the through pores of the refractory material, the smaller the pore diameter, and the more complex the pore structure of the material, the lower the air permeability of the material, which means the better the alkali vapor permeability of the material.
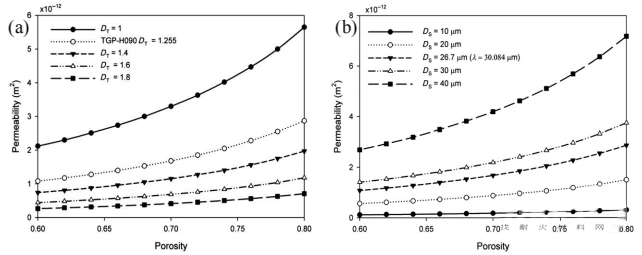
The optimization of the pore structure of the refractory material can be achieved by adjusting the particle gradation of the refractory material and adding a certain amount of micro-nano powder to it. Studies have shown that the use of physical and chemical reactions within the material to reduce the pore size and the degree of pore connectivity of the material is also one of the important means of adjusting the microstructure of the material.
In the field of refractory materials, micro-nano particles such as carbides, borides, and nitrides have been added. High-temperature diffusion or oxidation in an oxidizing atmosphere can be achieved to close a part of the pores in the refractory material, giving these materials excellent high-temperature performance.
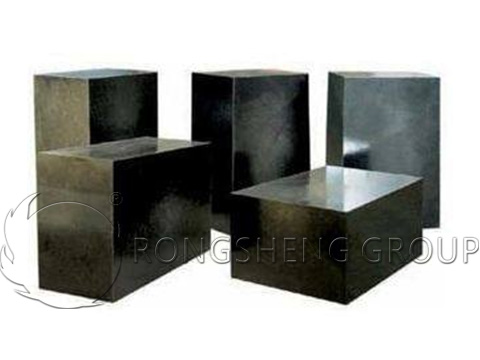
In carbon-containing refractories, some additives such as metals, metal alloys, carbides, or nitrides are also used in the microporation design of refractories. These substances form certain compounds or produce a certain volume expansion effect during the preparation and service process to block some pores, reduce the porosity and form a protective layer on the surface of the material, all of which can improve the anti-permeability performance of the refractory.
Among carbonaceous materials, microporous carbon bricks are prepared by the principle of the closest packing of particles and the principle of in-situ decomposition and expansion. Further studies have shown that if the pores in blast furnace carbon bricks are less than 1 μm or less, it is difficult for molten iron and zinc to penetrate into the material and cause a chemical attack. Subsequently, the average pore diameter and the pore volume ratio of <1 μm became important indicators for evaluating its quality.
Similarly, the introduction of silicon micro powder has also achieved microporosity of the aluminum-carbon refractory. Refractories with different pore diameters were tested for air permeability, and it was found that refractories with smaller pore diameters had lower air permeability. Therefore, this type of refractory also exhibits excellent corrosion resistance.
Zircon was introduced into mullite refractories and periclase-spinel refractories, respectively. The results show that zircon can block the pores in the material during the decomposition process and improve the densification of the material matrix. At the same time, the ability of the material to resist alkali corrosion has also been improved.
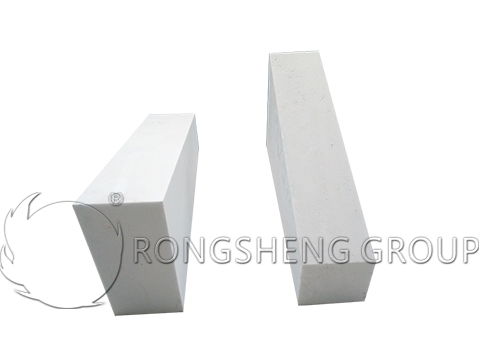
Through the research on the anti-alkali vapor erosion mechanism of andalusite, it is found that when sodium vapor erodes the andalusite material, the corrosion products formed will be locked in the mullite network, limiting the further occurrence of erosion. Therefore, this type of material exhibits relatively excellent resistance to alkali corrosion.
From the perspective of the percolation of corrosive gases in the refractory, the above work reduced the diameter of the pores in the refractory and blocked a part of the pores. This is beneficial to increase the complexity of the pore structure, reduce the connectivity of the pores, and increase the additional resistance and inertial force of the corrosive gas seepage in the refractory material, thereby significantly reducing the erosion of the material.
Rongsheng Refractory Materials Manufacturer
Rongsheng refractory material manufacturer and sales manufacturer is a refractory material manufacturer with rich experience and strong strength. Rongsheng’s refractory products have been sold to more than 60 countries and regions all over the world, for example, etc. And received praise and return orders from customers. Rongsheng also has rich experience in the development and design of refractory bricks and various unshaped refractory materials. Our mature technical team has already submitted satisfactory answers to the special refractory requirements of different high-temperature kilns. Whether you need to buy standard refractory brick products or need to buy refractory brick products of special materials and shapes, our technical team will provide you with satisfactory services. In addition, Rongsheng’s advanced environment-friendly and fully automatic monolithic refractory production line have an annual output of tons. It provides a reliable guarantee for the needs of various unshaped refractory materials for the lining of high-temperature kilns. Your inquiry is always welcome.