Refractory Lining is a layer of material which can resist high heat temperature in the kiln or furnace. The refractory lining can also resist thermal shocks, erosion, physical attack and chemical attack. If you are going to buy refractory lining in kilns, furnace or electric arc furnace, please contact RS Kiln Refractory Company! RS can provide you all the needed refractories materials for refractory lining.
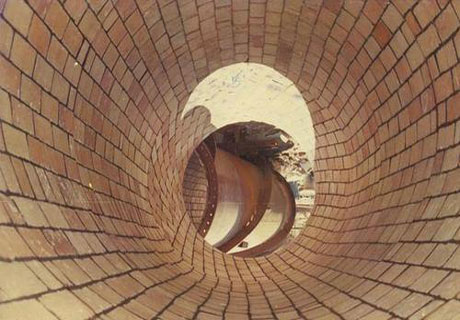
What Is Refractory Lining
Refractory lining is a kind of refractories, composed of refractory bricks and monolithic refractory materials. Refractory lining is used in the inner of kiln, furnace, incinerator, oven and so on. The commonly used refractory bricks in refractory lining are high alumina bricks, silica carbide bricks, silica mullite brick, etc. The widely applied monolithic refractory lining is aluminium silicate castable.
Refractory Lining Properties
- Heat damage resistance.
- Slag erosion resistance.
- Chemical corrosion resistance.
- Physical corrosion resistance.
- Wear resistance.
- Thermal storage.
Types Of Refractory Lining Materials
- Refractory lining bricks
- Monolithic refractory lining materials
Refractory Lining Drying-out Design
Speaking of the refractory lining design, the drying-out process is the most important step concerning the service life of a new lining. In the process, when the heating temperature exceeds 100 degrees Celsius, free water will leave the lining. But the chemically bound water in the plastic refractories won’t leave until the temperature reaches 500 degrees Celsius. And the installation of a new lining shouldn’t be heated up so quickly or it may cause steam explosion. After 24 hours of initial maintain, the lining should be heated to 550 degrees Celsius. During the period of temperature rise, the proper temperature gradient is maintained and the main burner should be directly applied to the drying process. Once lighted the fire, it shouldn’t be suspended. The lining temperature rises by 15℃/h to 150℃ and it should be maintained for 24 hours. Then the temperature increases by 25℃/h to 350℃, keeping it for at least 12 hours. After that, the temperature continues to go up at the same speed and reaches the temperature of 550℃.
Qualified Refractory Lining For Sale In RS Factory! Any Need? Contact RS!
Refractory Lining Of Blast Furnace
During the production of blast furnace, series of severe physical and chemical reactions are taking place.These reaction cause serious corrosion to refractory lining, particularly when these erosion occur under the high temperature or violent temperature fluctuations. Common chemical erosion are gas erosion,alkali metal erosion, slag erosion and molten iron erosion. There are also some mechanical wear. These erosion occur at the same time and promote each other. None of the refractories has comprehensive advantages over others to solve the erosion problem in a round way. Considering the variety and the performance of refractory material used in blast furnace lining, the corresponding material should be selected for different parts due to the erosion reason in order to get the suitable performance.
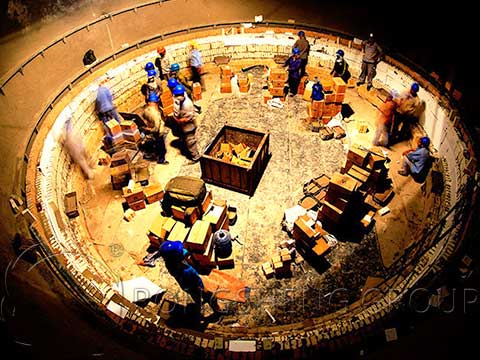
Hearth and hearth bottom: carbon brick, micro-pore carbon brick, aluminum carbon brick and mullite masonry
Belly and bosh of blast furnace: Si3N4-SiC brick, aluminum carbon brick
The middle and upper part of the furnace body: aluminum carbon brick and fire-clay brick (resist the the mechanical wear of the furnace material and gas flow).
Cheap Refractory Lining For Sale In RS Factory! Interested? Quote RS!
Ladle Refractory Lining
With the increasing demand for clean steel, the development of ladle defining and continuous casting technology, the function of ladle is expanding. The ladle refractory lining seems significant for its good function performance.
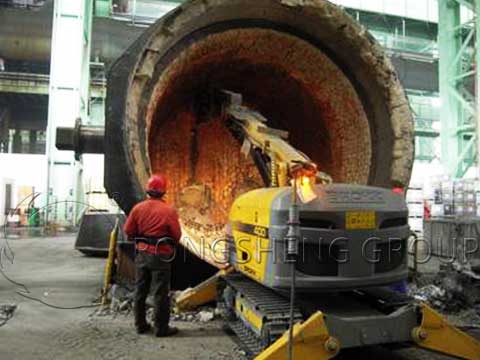
Cheap Refractory Lining For Sale In RS Factory! Interested? Quote RS!
Refractory lining used in steelmaking are used in harsh conditions which includes higher temperature and thermal shocks when the temperature changes abruptly. When molten steel is pour in from a converter or electric arc furnace, the temperature sometimes reaches an extremely high value 1700℃. Before the pour in of molten steel, the temperature of the lining of the ladle is usually between 800℃-1200℃, which causes stress in the lining layer, and this may lead to the stripping of the working layer.
It is well known that the reaction of slag at high temperature can cause erosion of refractory materials. The change of slag composition mainly depends on the smelting process. In the existing smelting process, it is mainly related to alkaline slag, which is likely to react with corundum brick lining. At present, corundum magnesia brick or corundum spinel brick is often used in the entire lining of ladle.
When castable refractory containing spinel (10%-25%) is used for a ladle lining, its resistance to damage is particularly important because its crystalline structure helps to capture a series of two or trivalent cations (Fe2+, etc.). Refractories containing spinel have very low porosity and excellent mechanical properties. However, Magnesium Oxide’s materials are replacing these spinel refractories now, because of cost reduction. But it is also because of its good anti permeability.
The preheating of the permanent layer of the ladle lining is an important factor which affects its performance. This phase is also a very important. At this time, any deviation from the ideal heating curve will cause greater stress in the lining, and sometimes may cause the mechanical stress on the burst layer, which are the most dangerous cause of the lining use. Prime. The sequence of thermal cycling during the treatment of molten steel and during the use of ladle will also cause some lining to become fragile and spalling.
Refractory Lining In Cement Rotary Kiln
The cement rotary kiln is one of the most important core equipment in the building industry. The length of its service life depends on the quality of the refractory lining brick, which is the key to ensure continuous production and the calcination quality of the products.
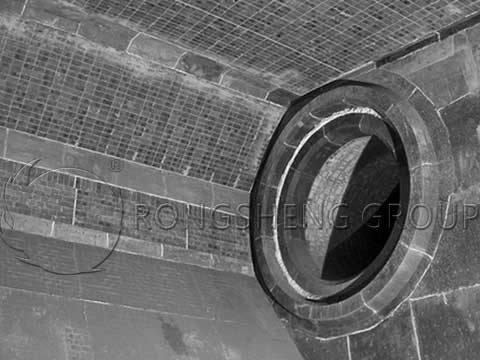
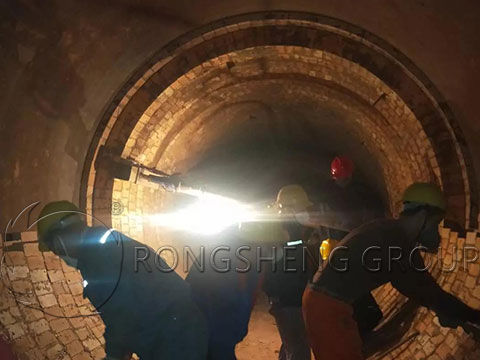
The function of the refractory lining brick in the cement rotary kiln are follows.
- To prevent the direct damage of the high temperature flame or air flow damage to the kiln body and protect the kiln barrel.
- To prevent harmful substances (CO, SO2) from eroding the kiln.
- To prevent the erosion of the kiln body by material and air flow.
- To reduce kiln temperature and prevent kiln body from being oxidized and eroded.
- To preserve heat.
- To improve the coatability.
Qualified Refractory Lining For Sale In RS Factory! Any Need? Contact RS!
The silica mullite wear-resistant brick, made of high alumina bauxite clinker and silicon carbide, is mainly applied in building refractory lining in cement rotary kiln, especially in the transition zone, cooler and kiln eye. It has the characteristics of high pressure strength at normal temperature, high structure strength at high temperature, good thermal shock stability and so on. In the course of using, the protective layer is gradually formed, which has good abrasion resistance and strong peel resistance.
Refractory Lining Manufacturers
RS Kiln Refractory Company is one of the leading refractory lining manufacturers in China, who is good at producing both refractory lining bricks and monolithic refractory lining materials. RS Company can provide you the quality refractory lining materials with the cheap price! RS Kiln Company, as a refractory lining manufacturer, can also offer you the best refractory lining design! Please don’t hesitate to Contact RS for the quote!