Magnesium-aluminum dry vibrating materials can be used to line the melting grooves of power frequency induction furnaces used in foundry and nonferrous metal industries, and good results have been achieved. Dry vibrating materials and ramming materials are new types of amorphous refractory materials developed in the past 10 years, and are developed under the guidance of basic refractory theories. The key technology is that the product of self-reaction and self-sintering at high temperatures must be a high-temperature phase material, and the particle grading and binder are also very important. The material was initially brought in with the introduction of electric furnaces and was soon domestically produced. A certain factory’s 150t ultra-high power electric furnace uses Rongsheng dry vibrating materials, with an average annual life of 260 times and a maximum of 305 times. When domestic dry vibrating materials are used, the average annual life is 282 times and a maximum of 332 times.
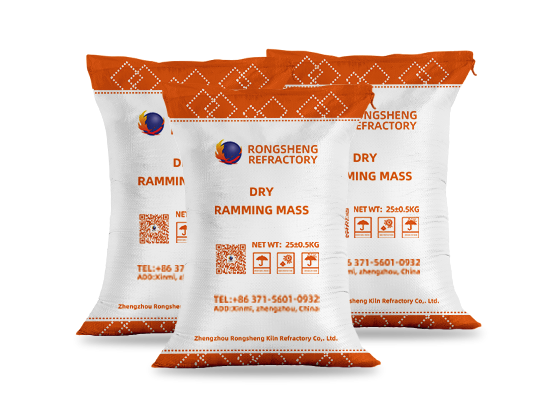
Dry Vibrating Mass Material
Dry vibrating material is a dry refractory mixture without any liquid added, which can be used directly without curing and baking after being vibrated to obtain a dense construction body. Its process principle is: adding various composite sintering agents to ensure the chemical reaction between materials at various temperatures to obtain high-temperature phase products and ceramic bonding. Carefully formulate the particle grading of the material to ensure that under the action of a small vibration force, the particles can move quickly and fill various gaps without surplus or shortage of each level of material, thereby obtaining a higher stacking density.
Dry vibrating materials are classified according to material types and parts of use. According to the material type, they are divided into dry vibrating materials such as siliceous, corundum, magnesium, magnesium-calcium, magnesium-aluminum, magnesium-aluminum spinel and Al2O3-SiC-C. According to the use part, they are divided into dry vibrating materials for the bottom of electric furnaces, dry vibrating materials for the melting groove of power frequency furnaces and dry vibrating materials for the working lining of the tundish, etc.
When the induction furnace melts cast iron and nonferrous metals, silica or fused quartz dry ramming mass is often used for the furnace lining. Boric anhydride is used as a sintering agent, and the amount is less than 2%. Although the melting point of boric anhydride B2O3 is 450℃, the low eutectic temperature with SiO2 is only 372℃, so it is not suitable as a sintering agent. However, quartz glass has a network structure and high viscosity, and B2O3 is also a network structure forming substance, which melts together to form a higher viscosity layer. Therefore, it can play a sintering role at medium and low temperatures, form a viscosity layer at medium and high temperatures, and can also improve the use effect of siliceous dry vibrating mass.
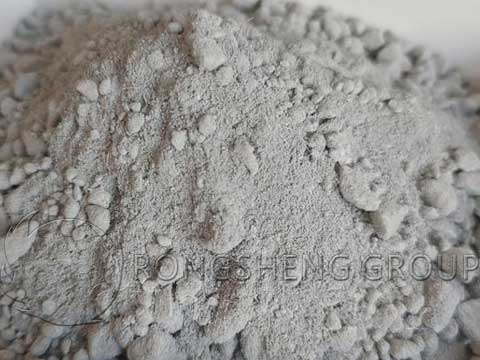
Corundum Dry Ramming Mix Material
Corundum dry ramming material also uses boric anhydride as a sintering agent, because AL2O3 and B2O3 can form an inconsistent molten compound 2AL2O3·B2O3 and a consistent molten compound 9A2O3·2B2O3. The former melts and decomposes at 1035℃, and the melting point of the latter is 1965℃. The low eutectic temperature is as high as 1920℃, which means it has good refractory properties. Its dosage is generally less than 8%, and the specific dosage should be determined based on experiments. In addition, AL2O3-SiC-C dry vibrating material also uses B2O3 as a sintering agent, which has no significant effect on its performance. Magnesium aluminum spinel dry vibrating material generally uses calcium aluminate material as a sintering agent, which has a better effect.
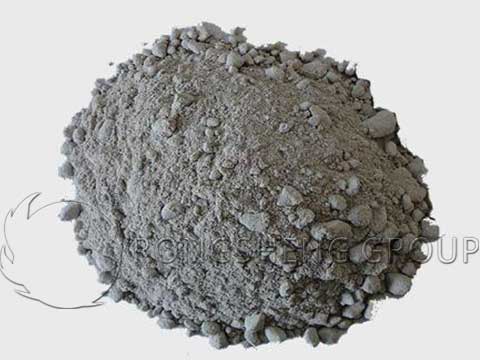
Aluminum-Magnesium Ramming Mass Material
Aluminum-magnesium ramming material is a semi-wet mixture that can be rammed and formed with alumina and magnesium oxide as the main components. It uses high-aluminum hot material (first-grade or special-grade alumina clinker) or corundum as aggregate and powder. It is a mud material prepared with water glass solution as a binder. The composition ratio of the ramming material is 88% to 92% of high-aluminum clinker (or corundum) aggregate and powder, 8% to 12% of sintered or fused magnesia powder, and 7% to 10% of water glass solution.
In the composition of the ramming material, sintered or fused magnesia is added to the matrix in the form of fine powder, with the purpose of allowing MgO and Al2O3 to react in situ to form aluminum-magnesium spinel (Al2O3·MgO). The formation of spinel can not only compensate for the sintering shrinkage of the ramming material, but also improve the permeability and erosion resistance to high-temperature slag.
The binder should be a high modulus water glass solution, because the smaller the modulus, the higher the Na2O content, which will reduce the high temperature slag resistance of the ramming material. Generally, a water glass solution with a modulus greater than 2.6 and a density of 1.2-1.3 g/cm3 is used as a binder.
General physical and chemical properties of aluminum-magnesium ramming materials made with special high-aluminum clinker and medium-grade sintered magnesia. Chemical composition Al2O3 70%-75%, MgO 6%-10%. After drying, the bulk density is 2.60 ~2.75 g/cm3, and the compressive strength is 45-55 MPa. After sintering at 1400℃ for 3 h, the porosity is 22%-23%, the compressive strength is 70-85 MPa, and the linear change rate is -(2.0-0.8)%.
Aluminum-magnesium ramming materials can be used as integral ramming linings for ladle, linings for induction furnaces, linings for electric furnace tapping troughs, and high-temperature containers in contact with high-temperature metal solutions and solutions.