Refractory materials are the main components of glass melting furnaces, which have a decisive influence on glass quality, energy consumption, and product costs. The future of glass melting technology depends to a certain extent on the progress of refractory materials’ manufacturing technology and the improvement of product quality. Therefore, understanding the common cracks on the surface of silica bricks for glass kilns will help improve the yield rate of high-quality silica bricks in production.
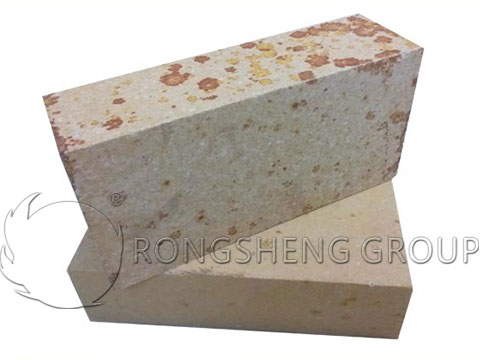
Silica Bricks for Glass Kiln
Silica bricks are widely used in glass melting furnaces, and the main component is silicon dioxide (SiO₂). The silica brick used in the glass melting furnace requires a SiO₂ content of 94% or more, a maximum operating temperature of about 1600~1650℃, and a density of 1.8~1.95g/cm³. The apparent porosity is required to be less than 22%. The larger the porosity, the worse the quality of the silica brick. The appearance of silica bricks is mostly white crystals, and the microscopic composition is tridymite crystals. Because silicon bricks undergo crystallization conversion and volume expansion at high temperatures, especially at 180~270℃ and 573℃, the crystallization conversion becomes more intense. Therefore, in the process of baking kilns and cold repairs, appropriate measures such as elastic strips should be adopted to adapt to the crystal transformation of silica bricks. The silicon brick masonry should be left with expansion joints.
The working temperature of silica bricks is about 200℃ higher than that of clay bricks, but the corrosion resistance to molten glass and alkaline flying materials is poor. Therefore, it is used for masonry structures such as a big chute, parapet, and a small furnace. When masonry, use high-silicon refractory mud or silica brick powder and other materials close to the composition of silica bricks as the cementing material.
For the large-scale float glass furnace production line, the composition of the glass furnace and the configuration of refractory bricks are as follows. Generally, L-shaped suspended walls usually use silica bricks. In the melting part, the area that is in direct contact with the molten glass should use fused bricks, and the silicon bricks or fused bricks near the top. For card necks, silica bricks are usually used. The cooling part includes the ear pool. Corundum materials are usually used where they are in direct contact with molten glass, and silica bricks or corundum are used where they are not in direct contact with molten glass. The annealing kiln and regenerator are built with high alumina bricks, fireclay bricks, and directly combined with magnesia-chrome bricks.
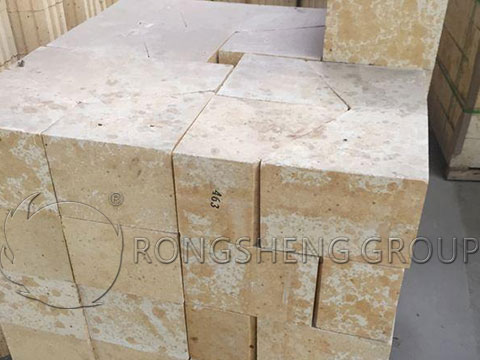
Common Cracks on the Surface of Silica Bricks for Glass Kilns
The cracks of silicon brick products can be divided into surface cracks and internal cracks, the latter is also called spalling. Surface cracks are divided into transverse cracks, longitudinal cracks, and network cracks. Silica bricks for glass kilns are prepared by using a semi-dry press molding method to prepare compact bodies. The cracks produced along the direction of the brick press are transverse cracks, and the cracks perpendicular to the direction of the brick press are vertical cracks. The surface of the silicon brick product is composed of several cracks, which are distributed in the form of spider webs, that is, web cracks. See Figure 1.
Generally, for a standard type of silica brick, the direction of pressing the body is generally the thickness direction. The molding process of silica brick products is essentially a process in which the particles in the blank are dense and the air is discharged to form a compact body. After the brick is pressed and formed, it has the advantages of high density, high strength, small drying shrinkage and firing shrinkage, and easy control of product size. However, when the press molding process is improperly controlled, the clay brick body will form layered cracks perpendicular to the pressing direction during the pressing process. Therefore, the layered cracks inside the silicon brick, or spalling for short, are also longitudinal cracks.
Large spalls can be detected as soon as the bricks are formed or after the bricks have dried. However, the small spalls in the bricks can only be clearly detected after the firing process when the silica bricks for glass kilns continue to expand with the action of thermal stress. Silicon bricks with crack defects, especially spalling, are prone to breakage, which can not be used and reduces the yield of silicon brick products.
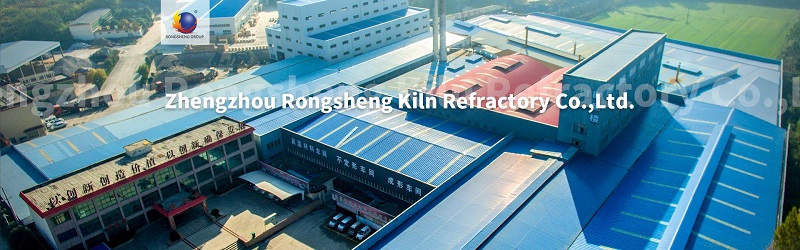
Purchase High-Quality Refractory Bricks for Glass Kilns
Rongsheng refractory material manufacturer is an experienced refractory brick and refractory castable manufacturer and sales company. Our refractory products have been sold to more than 60 countries around the world. And received constant praise and return orders from customers. Rongsheng refractories manufacturers provide high-quality silica bricks, AZS bricks, corundum bricks, high alumina bricks, large fireclay bricks, and other refractory materials for glass kilns. To purchase high-quality refractory bricks for glass kilns, such as silica bricks for glass kilns, please contact us. We will provide you with services according to your specific needs.