Silicon Carbide Mullite Bricks have high strength, wear resistance, and are not easy to peel off and corrode. Especially in the transition zone of the cement kiln, the effect is remarkable. The characteristics of Silicon Carbide Mullite Bricks are high strength, wear resistance, and good seismic stability, and the service life in the firing zone and transition zone of cement rotary kiln is better than that of spinel bricks.
Silicon Carbide Mullite Bricks for Cement Rotary Kiln
The “silicon” in the Silicon Carbide Mullite Bricks refers to silicon carbide, and “mo” refers to mullite. In fact, Silicon Carbide Mullite Bricks are refractory bricks made by sintering high alumina bauxite and silicon carbide as the main raw materials. Essentially, Silicon Carbide Mullite Brick is just a high-alumina brick with silicon carbide added. Among them, some products may be mixed with refractory raw materials such as mullite, “three stones” and corundum.
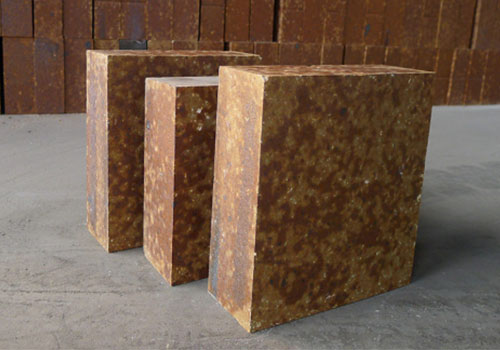
Product Performance of Silicon Carbide Mullite Bricks
Silicon Carbide Mullite Bricks have a dense structure, high high-temperature compressive strength, high-temperature structural strength, and good thermal shock stability. Moreover, it can continuously form a protective layer during use and has the advantages of good wear resistance and strong peeling resistance.
The Main Application of Silicon Carbide Mullite Bricks in Cement Rotary Kiln
Silicon Carbide Mullite Brick is suitable for the transition zone, preheating zone, tertiary air duct, five-stage preheater, and lime kiln discharge chute of cement rotary kiln.
Application of Modified Silicon Carbide Mullite Bricks in Cement Rotary Kiln
Silicon Carbide Mullite Brick is a kind of high alumina silicon carbide refractory brick. If different special refractory raw materials are added to the Silicon Carbide Mullite Bricks, some properties of the Silicon Carbide Mullite Bricks can be further improved. Therefore, these modified Silicon Carbide Mullite Bricks can be divided into different subclasses. For example, a part of andalusite can be used to replace bauxite in the bricks made of Silicon Carbide Mullite Bricks to produce Silicon Carbide Mullite Red Bricks. In addition to good high-temperature resistance and corrosion resistance, the Red Silicon Carbide Mullite Bricks also have better thermal shock resistance than Silicon Carbide Mullite Bricks.
The Red Silicon Carbide Mullite Bricks are refractory bricks developed according to the strict requirements of large and medium-sized cement rotary kilns for refractory materials in the transition zone and cooling zone. On the basis of conventional Silicon Carbide Mullite Red Bricks, the thermal shock resistance and thermal insulation effect are further strengthened, and the softening temperature under load is also increased. Therefore, when used in the transition zone and cooling zone of the rotary kiln above 3000-10000t/d, its excellent performance is outstanding, and its service life is higher than that of other products. The practice of many cement factories has proved that the upper transition zone of 5000t/d new dry process water kiln can obtain 12 months of service life. Used in the upper transition zone of 2500t/d new dry process cement kiln, the service life of 1 to 2 years can be obtained, which is equivalent to 150% to 200% of the service life of magnesia-aluminum spinel bricks.
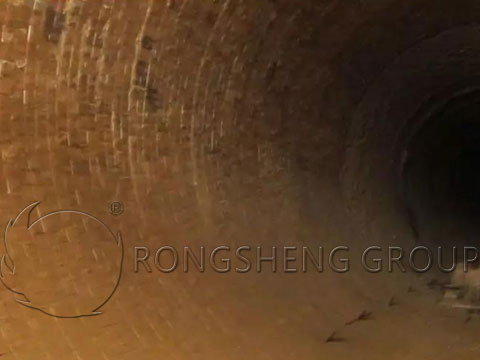
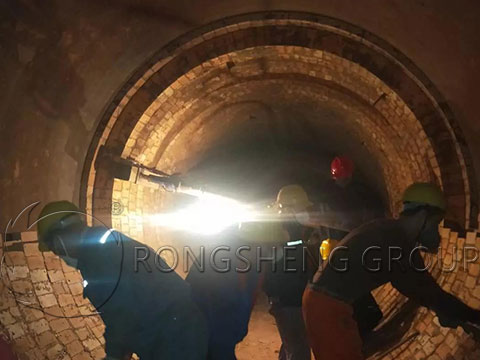
Why Can Silicon Carbide Mullite Bricks Improve the Service Life of Cement Rotary Kiln Lining?
Silicon carbide is synthesized by the reaction of carbon and silica under ultra-high temperature and strongly reducing conditions. The characteristic of synthesis is that the carbon particles do not move, and SiO2 and intermediate substances (SiO, Si) first become gas phase and then contact and react with carbon.
Influence of Silicon Carbide on Properties of High Alumina Bricks
After adding silicon carbide to high-alumina bricks, the wear resistance, thermal shock resistance, load softening temperature, and corrosion resistance of high-alumina bricks can be greatly improved. A new type of refractory brick with superior comprehensive performance is manufactured.
Silicon carbide has a Mohs hardness of up to 9.5. Adding silicon carbide to high alumina bricks increases the hardness of refractory bricks. In this way, when the abrasive particles are in contact with the refractory brick, the depth of the abrasive particles chiseled into the refractory brick is limited. The possibility of cutting certain substances from the surface of the refractory brick by abrasive particles when sliding on the surface of the refractory brick is reduced, thereby improving the wear resistance of the refractory brick. Silicon carbide has high thermal conductivity and moderately low thermal expansion coefficient. Adding silicon carbide to high-alumina bricks increases the thermal conductivity of the material and reduces the thermal expansion coefficient of the material, thereby significantly improving the thermal shock resistance of the high-alumina brick.
Silicon carbide is oxidized to form SiO2 and CO, and SiO2 reacts with AI2O3 to form mullite. Both reactions were accompanied by a large volume increase. The reaction product mullite also has good high-temperature properties. Therefore, adding an appropriate amount of silicon carbide can help compensate for the refiring shrinkage of refractory bricks and increase the softening temperature and creep resistance under load.
Cheap Silicon Carbide Mullite Bricks For Sale In RS Factory! Interested? Contact Us Now!
At the earliest, some technicians believed that the upper limit of the use temperature of high-alumina bricks in cement kilns was 1300~1350℃. If it exceeds 1300°C, the products rich in CAS2 and C2AS formed by the reaction of CaO in the cement clinker with AI2O3 and SiO2 in the refractory bricks will be burned, and the refractory bricks without protection will be quickly damaged. Therefore, the high-temperature zone of the cement kiln, including the firing zone and the transition zone, needs to use alkaline bricks. At present, this view needs to be revised due to the invention of Silicon Carbide Mullite Bricks by Chinese companies.
After adding silicon carbide, the erosion mechanism of high alumina bricks is changed. This change is due to the oxidation of SiC.
- First, the SiC on the surface of the silicon carbide mullite bricks is oxidized to SiO2, which blocks the pores on the surface of the brick and changes the atmosphere in the brick to a reduced state.
- Second, the SiC inside the Silicon Carbide Mullite Bricks is activated and oxidized, and the formed SiO gas diffuses to the surface of the refractory brick and is further oxidized to form SiO2.
- Third, the newly formed SiO2 forms a high-viscosity glass phase together with other substances, which blocks the pores, slows the entry of oxygen, and maintains the reducing atmosphere in the brick. Therefore, when the original high-viscosity glass phase protective layer on the surface of the Silicon Carbide Mullite Bricks is eroded and thinned, oxygen enters the Silicon Carbide Mullite Bricks, and the SiC inside the brick is activated and oxidized. The generated SiO gas is oxidized to SiO2 on the surface of the refractory brick to establish a new protective layer. In this way, the erosion of the refractory brick is greatly slowed down and the life of the refractory brick is improved.
RS Refractory Materials for Sale can provide a variety of high-quality refractory lining materials for cement rotary kilns. Including refractory bricks, refractory castables, etc. We also have rich experience in the application of Silicon Carbide Mullite Bricks for cement rotary kilns. RS Refractory Materials Factory can provide high-quality refractory bricks such as Silicon Carbide Mullite Bricks, Red Silicon Carbide Mullite Bricks, spinel bricks, and high alumina bricks for the lining of cement rotary kilns. Contact us for free product samples and quotes.